Brazing filler metals are critical components in the brazing process, as they form the bond between the base materials being joined. These metals must have a lower melting point than the base materials and exhibit good wetting and flow properties to ensure a strong joint. The types of filler metals used in brazing vary depending on the base materials, application requirements, and operating conditions. Common categories include aluminium-silicon alloys, copper-based alloys, silver-based alloys, nickel-based alloys, and precious metals like gold and palladium. Each type has unique properties that make it suitable for specific applications, such as aerospace, electronics, or stainless steel brazing.
Key Points Explained:
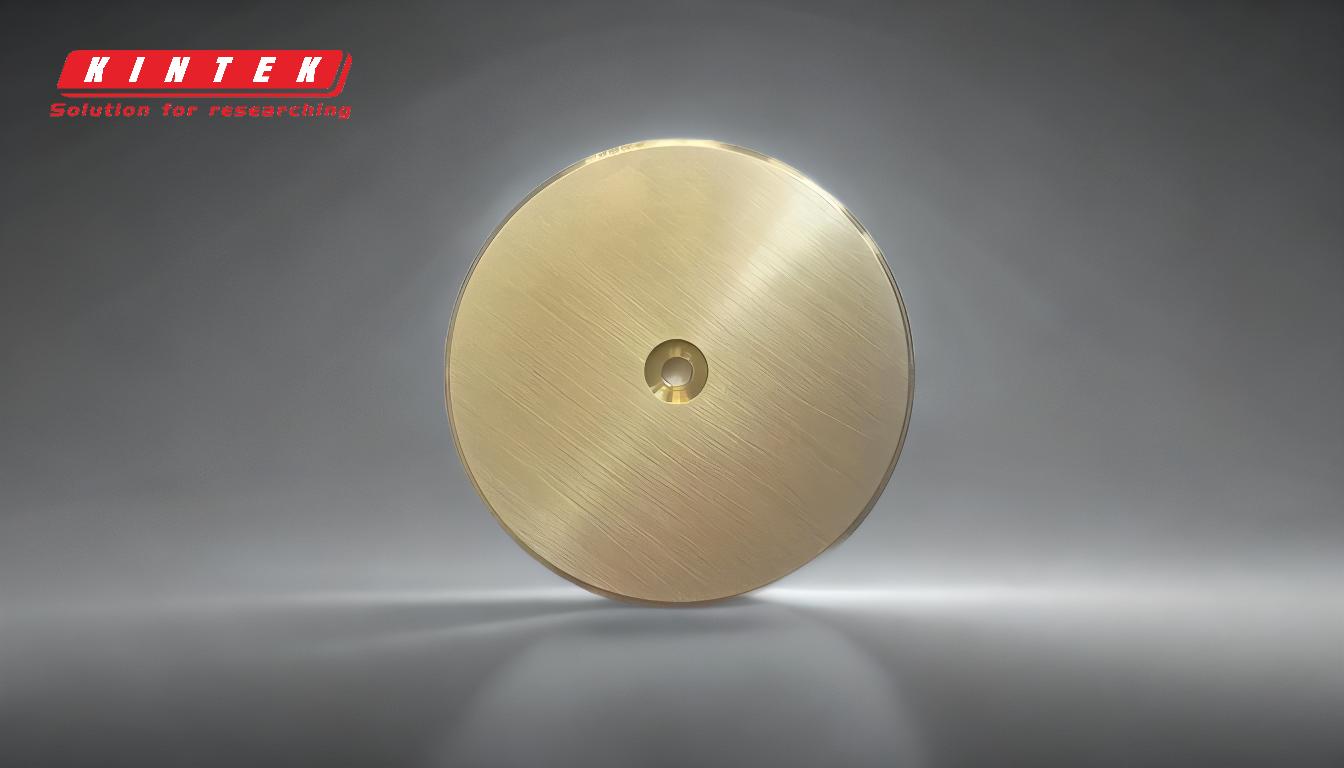
-
Aluminium-Silicon Alloys
- These alloys are widely used for brazing aluminium and its alloys due to their compatibility and excellent wetting properties.
- They typically contain 7-12% silicon, which lowers the melting point and improves fluidity.
- Applications include heat exchangers, automotive components, and aerospace structures.
-
Copper-Based Alloys
- Copper and its alloys (e.g., copper-zinc, copper-phosphorus, copper-silver) are commonly used for brazing ferrous and non-ferrous metals.
- Copper-Phosphorus: Suitable for brazing copper and brass, as it is self-fluxing (requires no additional flux).
- Copper-Zinc (Brass): Often used for brazing steel and cast iron due to its high strength and corrosion resistance.
- Applications include plumbing, refrigeration, and electrical components.
-
Silver-Based Alloys
- Silver filler metals, such as silver-copper and silver-copper-zinc, are versatile and widely used for brazing stainless steel, copper, and nickel alloys.
- They offer excellent flow properties, high strength, and good corrosion resistance.
- Applications include HVAC systems, medical devices, and electronics.
-
Nickel-Based Alloys
- Nickel filler metals are ideal for high-temperature applications and brazing stainless steel, nickel alloys, and superalloys.
- They provide excellent oxidation and corrosion resistance, making them suitable for aerospace and power generation industries.
- Examples include nickel-chromium and nickel-phosphorus alloys.
-
Precious Metals
- Gold and palladium-based filler metals are used in specialized applications requiring high reliability and corrosion resistance.
- Gold-Silver-Nickel Alloys: Commonly used in aerospace and electronics for brazing critical components.
- Palladium-Based Alloys: Suitable for high-temperature and vacuum applications.
-
Amorphous Brazing Foils
- These foils are made from metals like nickel, iron, copper, silicon, boron, and phosphorus.
- They are used in precision brazing applications, such as electronics and medical devices, due to their uniform composition and excellent wetting properties.
-
Manganese-Based Alloys
- Manganese filler metals are used for brazing stainless steel and other high-strength alloys.
- They offer good mechanical properties and are suitable for high-temperature environments.
-
Tin-Lead Solder
- Although primarily used in soldering, tin-lead alloys can also be used for low-temperature brazing of stainless steel and other metals.
- They are less common in modern applications due to environmental concerns about lead.
-
Specialized Alloys for Aerospace
- Aerospace applications often require filler metals like nichrome, gold, and silver due to their high performance in extreme conditions.
- These alloys ensure strong, reliable joints in critical components like turbine blades and heat exchangers.
By understanding the specific properties and applications of these filler metals, purchasers can select the most appropriate material for their brazing needs, ensuring optimal performance and durability of the final product.
Summary Table:
Filler Metal Type | Key Properties | Common Applications |
---|---|---|
Aluminium-Silicon Alloys | 7-12% silicon, excellent wetting, low melting point | Heat exchangers, automotive, aerospace |
Copper-Based Alloys | High strength, corrosion resistance, self-fluxing (copper-phosphorus) | Plumbing, refrigeration, electrical components |
Silver-Based Alloys | Excellent flow, high strength, corrosion resistance | HVAC systems, medical devices, electronics |
Nickel-Based Alloys | High-temperature resistance, oxidation and corrosion resistance | Aerospace, power generation |
Precious Metals | High reliability, corrosion resistance, suitable for extreme conditions | Aerospace, electronics, critical components |
Amorphous Brazing Foils | Uniform composition, excellent wetting | Precision brazing in electronics, medical devices |
Manganese-Based Alloys | Good mechanical properties, high-temperature suitability | Stainless steel, high-strength alloys |
Tin-Lead Solder | Low-temperature brazing (less common due to environmental concerns) | Stainless steel, general low-temperature applications |
Specialized Aerospace Alloys | High performance in extreme conditions, reliability | Turbine blades, heat exchangers, aerospace components |
Need help choosing the right brazing filler metal? Contact our experts today for tailored solutions!