Sintering is a versatile pyrometallurgical process with a wide range of applications across various industries. It involves heating small particles of metal or other materials below their melting points to weld them together, forming dense and durable structures. This method is particularly useful for creating complex shapes, producing alloys, and working with high-melting-point metals. Sintering is extensively used in ceramics, additive manufacturing, and metallurgy, enabling the production of materials with enhanced mechanical strength, thermal stability, and density. Additionally, it plays a critical role in modern manufacturing techniques like 3D printing, where it allows for precise control over material properties and energy efficiency.
Key Points Explained:
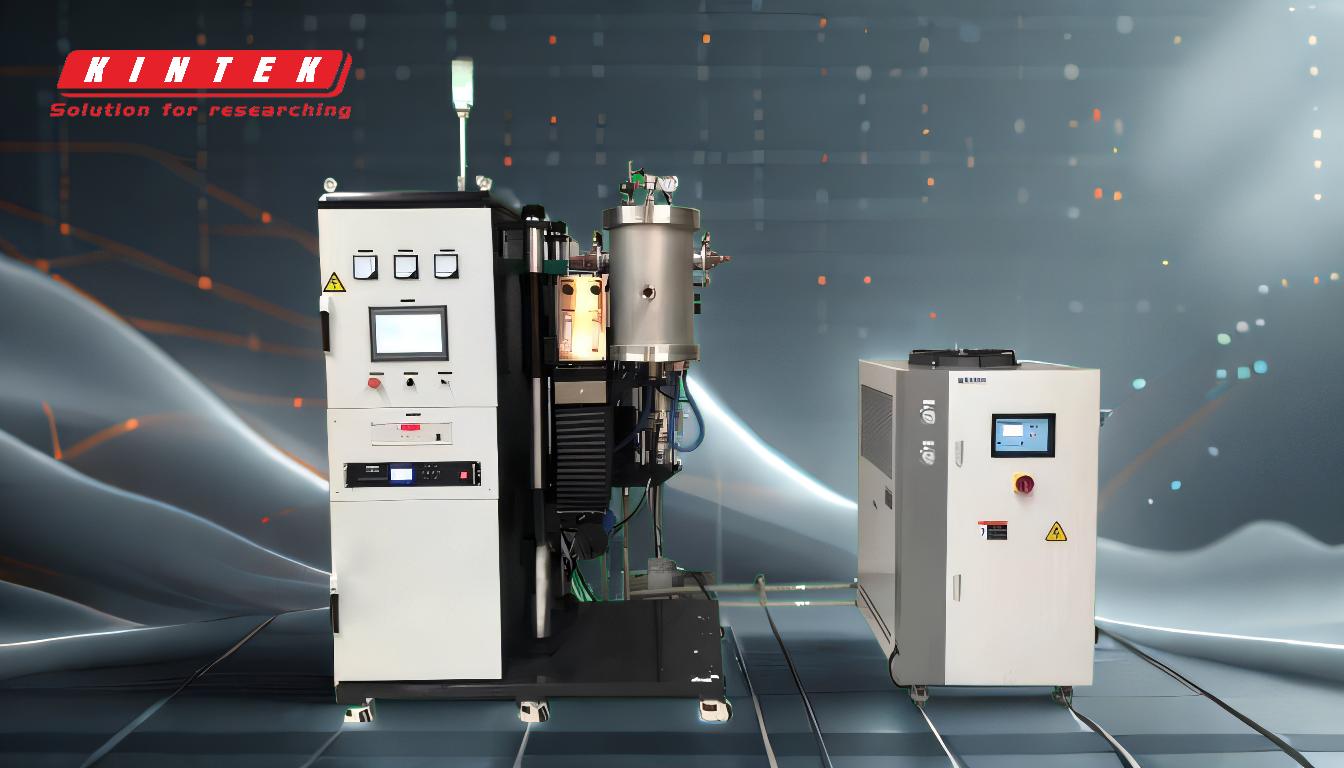
-
Formation of Complex Shapes
- Sintering is widely used to create intricate and custom shapes that are difficult to achieve through traditional manufacturing methods. By welding small particles together below the melting point, sintering allows for precise control over the final geometry of the product. This is particularly beneficial in industries like aerospace and automotive, where complex components are often required.
-
Production of Alloys and High-Melting-Point Metals
- Sintering is essential for producing alloys and working with metals that have high melting points, such as tungsten and molybdenum. Since sintering does not require reaching the melting temperature, it saves energy and reduces the risk of material degradation. This makes it a preferred method for manufacturing steel and other high-performance alloys.
-
Applications in Ceramics
- In the ceramics industry, sintering is used to produce materials with improved mechanical strength, hardness, and thermal stability. Common applications include ceramic tiles, sanitaryware, cutting tools, refractory materials, and electrical insulators. By carefully controlling sintering parameters like temperature and duration, manufacturers can achieve the desired density, porosity, and microstructure.
-
Role in Additive Manufacturing
- Sintering is a cornerstone of additive manufacturing techniques such as selective laser sintering (SLS) and electron beam sintering (EBS). These processes use powdered materials that are selectively sintered layer by layer based on digital designs to create complex 3D objects. Sintering ensures the consolidation and bonding of the powdered material, resulting in fully dense and functional parts. This technology is revolutionizing industries like healthcare, where custom implants and prosthetics are produced with high precision.
-
Improvement of Material Properties
- Sintering can significantly reduce the porosity of material surfaces, enhancing their mechanical and thermal properties. This is particularly important in applications where material density and durability are critical, such as in filters, bearings, and structural components. For example, sintered plastic and pe filters are widely used in filtration systems due to their high efficiency and durability.
-
Energy Efficiency and Consistency
- Compared to traditional melting processes, sintering is more energy-efficient because it operates at lower temperatures. This not only reduces energy consumption but also allows for greater consistency and control over the final product. This advantage is particularly valuable in industries like 3D printing, where precision and repeatability are essential.
-
Research and Development of New Materials
- Sintering is increasingly being applied in the research and development of new materials, including advanced ceramics and composites. Induction sintering technology, for instance, enhances the bonding of solid particles on special ceramics, promoting grain growth and increasing material density. This opens up new possibilities for creating materials with unique properties for specialized applications.
In summary, sintering is a critical process with diverse applications in manufacturing, ceramics, metallurgy, and additive manufacturing. Its ability to create complex shapes, improve material properties, and save energy makes it an indispensable technique in modern industry.
Summary Table:
Key Applications | Benefits |
---|---|
Formation of Complex Shapes | Enables precise control over geometry, ideal for aerospace and automotive. |
Production of Alloys and Metals | Saves energy and avoids material degradation, perfect for high-melting-point metals. |
Ceramics Manufacturing | Improves mechanical strength, hardness, and thermal stability. |
Additive Manufacturing (3D Printing) | Creates fully dense and functional parts for industries like healthcare. |
Material Property Enhancement | Reduces porosity, enhancing durability in filters, bearings, and components. |
Energy Efficiency | Operates at lower temperatures, ensuring consistency and reducing energy use. |
Research & Development | Enables the creation of advanced ceramics and composites with unique properties. |
Unlock the potential of sintering for your industry—contact our experts today to learn more!