The sintering process is influenced by a variety of variables that determine the quality, density, and mechanical properties of the final product. Key variables include temperature, heating rate, pressure, particle size, composition, atmosphere, cooling rate, and process-specific parameters such as layer thickness and machine speed. Each variable plays a critical role in sintering kinetics, densification, and the elimination of porosity. Understanding and optimizing these variables is essential for achieving the desired material properties and ensuring the efficiency of the sintering process.
Key Points Explained:
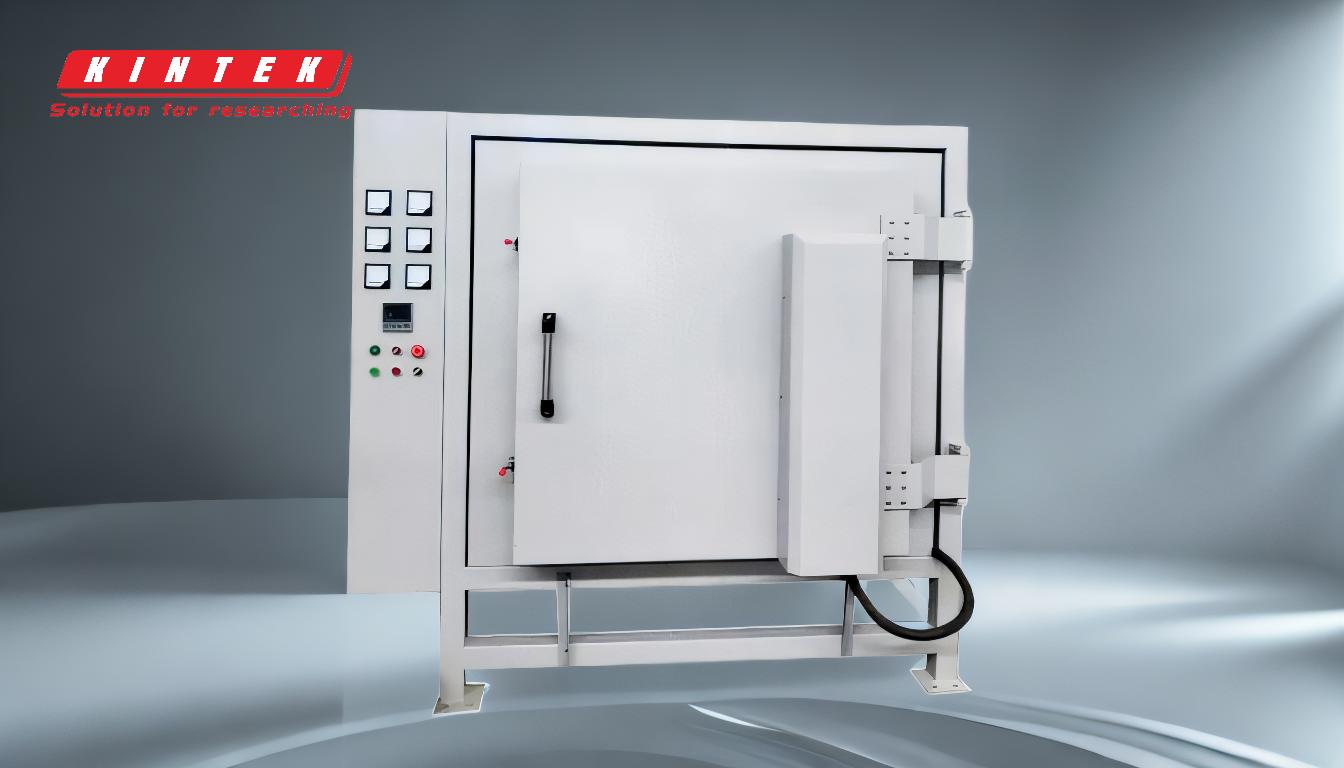
-
Temperature:
- Role: Temperature is a critical variable that determines sintering kinetics and the final material properties. It affects the rate of diffusion and the formation of bonds between particles.
- Impact: Higher temperatures generally increase the rate of densification and improve mechanical properties such as tensile strength and impact energy. However, excessively high temperatures can lead to unwanted grain growth or melting.
- Optimization: The sintering temperature must be carefully controlled based on the material composition and desired properties.
-
Heating Rate:
- Role: The heating rate influences the densification process by controlling the time available for particle rearrangement and bond formation.
- Impact: A slower heating rate allows for more uniform densification, while a faster rate can lead to uneven sintering and residual porosity.
- Optimization: The heating rate should be adjusted to balance densification efficiency and uniformity.
-
Pressure:
- Role: Applied pressure enhances particle rearrangement and helps eliminate porosity by forcing particles into closer contact.
- Impact: Higher pressure can significantly improve densification and reduce the sintering time. However, excessive pressure may cause deformation or cracking.
- Optimization: The applied pressure must be tailored to the material and sintering conditions to achieve optimal results.
-
Particle Size:
- Role: Particle size affects sintering behavior, with smaller particles promoting faster densification due to their higher surface area and energy.
- Impact: Finer powders generally result in better densification and improved mechanical properties. However, very fine particles may agglomerate, leading to uneven sintering.
- Optimization: The particle size distribution should be controlled to ensure uniform sintering and avoid agglomeration.
-
Composition:
- Role: The chemical composition of the material influences sintering behavior, including the formation of liquid phases and the stability of the solid phase.
- Impact: Homogeneous compositions promote better densification and more consistent material properties. Impurities or inhomogeneities can lead to defects or uneven sintering.
- Optimization: The composition should be carefully selected and controlled to achieve the desired sintering outcomes.
-
Atmosphere:
- Role: The sintering atmosphere (e.g., air, vacuum, argon, nitrogen) affects oxidation, reduction, and other chemical reactions during sintering.
- Impact: Inert or reducing atmospheres can prevent oxidation and improve sintering quality, while reactive atmospheres may introduce unwanted chemical changes.
- Optimization: The choice of atmosphere depends on the material and the desired properties of the final product.
-
Cooling Rate:
- Role: The cooling rate influences the microstructure and mechanical properties of the sintered material.
- Impact: Controlled cooling can prevent thermal stresses and improve material properties, while rapid cooling may lead to cracking or residual stresses.
- Optimization: The cooling rate should be adjusted based on the material and sintering conditions to achieve the desired microstructure.
-
Process-Specific Parameters:
-
Layer Thickness:
- Role: The thickness of the sintering layer affects heat distribution and densification.
- Impact: Thicker layers may lead to uneven sintering, while thinner layers allow for more uniform heating.
- Optimization: Layer thickness should be controlled to ensure uniform sintering and avoid defects.
-
Machine Speed:
- Role: The speed of the sintering machine determines the residence time of the material in the sintering zone.
- Impact: Faster speeds may reduce sintering time but can lead to incomplete densification, while slower speeds ensure thorough sintering.
- Optimization: Machine speed should be adjusted to balance efficiency and sintering quality.
-
Air Volume and Vacuum:
- Role: Air volume and vacuum levels influence heat transfer and gas flow during sintering.
- Impact: Proper control of air volume and vacuum ensures efficient heat distribution and gas removal, leading to better sintering outcomes.
- Optimization: These parameters should be adjusted based on the sintering setup and material requirements.
-
Layer Thickness:
By carefully controlling and optimizing these variables, manufacturers can achieve high-quality sintered products with the desired mechanical properties and microstructural characteristics.
Summary Table:
Variable | Role | Impact | Optimization |
---|---|---|---|
Temperature | Determines sintering kinetics and material properties. | Higher temps improve densification; excessive heat causes grain growth. | Control based on material and desired properties. |
Heating Rate | Influences densification and uniformity. | Slow rates ensure uniform sintering; fast rates may cause porosity. | Balance densification efficiency and uniformity. |
Pressure | Enhances particle rearrangement and eliminates porosity. | Higher pressure improves densification; excessive pressure causes cracks. | Tailor to material and sintering conditions. |
Particle Size | Affects sintering behavior; smaller particles densify faster. | Finer powders improve densification; agglomeration can cause unevenness. | Control particle size distribution for uniform sintering. |
Composition | Influences sintering behavior and material stability. | Homogeneous compositions promote better densification and properties. | Select and control composition carefully. |
Atmosphere | Affects oxidation, reduction, and chemical reactions. | Inert atmospheres prevent oxidation; reactive atmospheres may alter properties. | Choose atmosphere based on material and desired outcomes. |
Cooling Rate | Influences microstructure and mechanical properties. | Controlled cooling prevents stress; rapid cooling may cause cracking. | Adjust cooling rate based on material and sintering conditions. |
Layer Thickness | Affects heat distribution and densification. | Thicker layers may cause uneven sintering; thinner layers ensure uniformity. | Optimize layer thickness for uniform sintering. |
Machine Speed | Determines residence time in sintering zone. | Faster speeds reduce time but may cause incomplete densification. | Balance speed for efficiency and quality. |
Air Volume/Vacuum | Influences heat transfer and gas flow. | Proper control ensures efficient heat distribution and gas removal. | Adjust based on sintering setup and material requirements. |
Optimize your sintering process today—contact our experts for tailored solutions!