An induction coil is a versatile device that leverages electromagnetic principles to achieve various applications. At its core, it consists of a conductive coil, typically made of copper, which generates a magnetic field when an electrical current passes through it. This magnetic field can be used for heating metals, generating high voltages, or powering ignition systems. The effectiveness of the coil depends on its design and the current flowing through it. Induction coils are widely used in industries such as manufacturing, automotive, and electronics, making them essential for processes like metal melting, ignition systems, and high-voltage generation.
Key Points Explained:
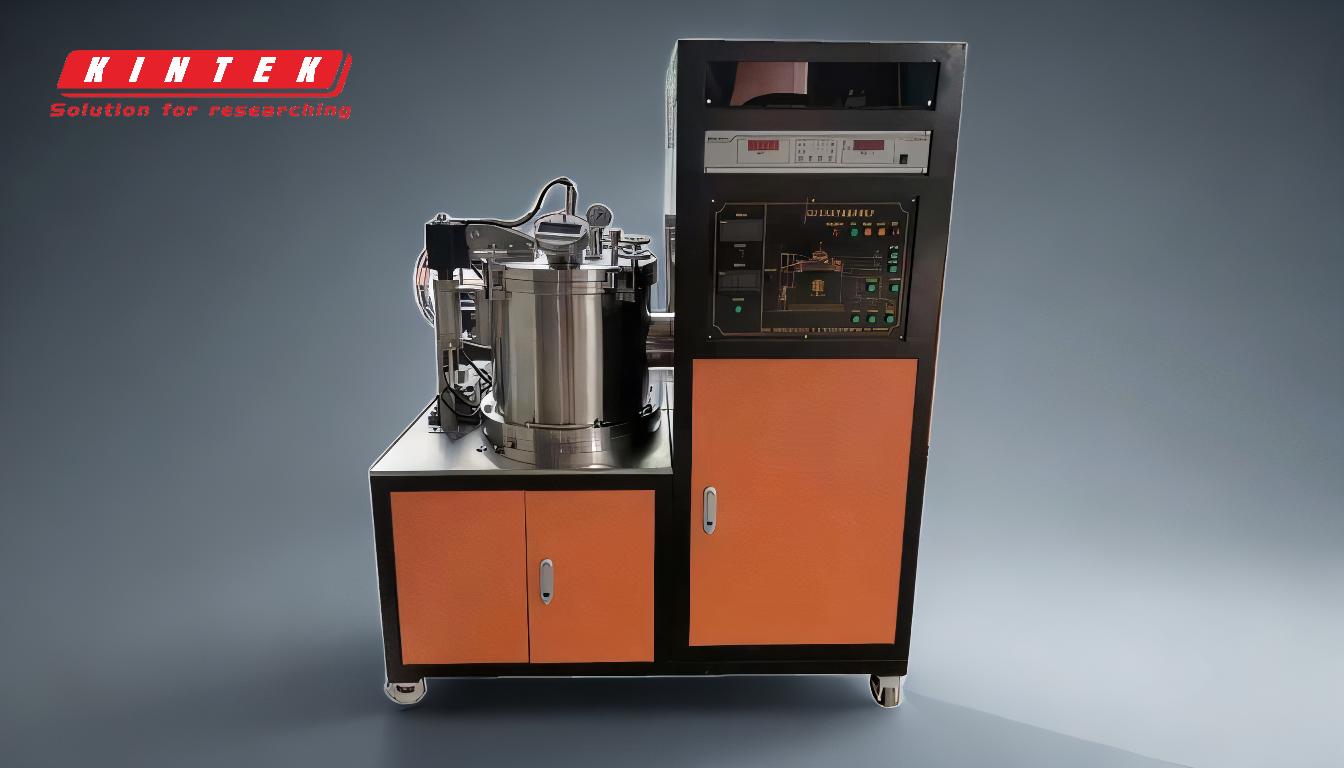
-
Principle of Operation
- Induction coils operate based on electromagnetic induction. When an electrical current flows through the coil, it generates a magnetic field.
- The magnetic field transfers energy to conductive materials (e.g., metals) placed within or near the coil, inducing eddy currents that heat the material.
- The strength and effectiveness of the magnetic field depend on factors like coil design, material, and the amount of current supplied.
-
Applications in Heating and Melting
- Induction coils are commonly used in industrial settings for heating and melting metals.
- The magnetic field induces eddy currents in the metal, causing it to heat up rapidly and uniformly.
- This process is highly efficient and precise, making it ideal for applications like metal casting, forging, and heat treatment.
-
High-Voltage Generation
- Induction coils can generate high voltages through mutual inductance.
- When a changing current flows through the primary coil, it induces a high voltage in the secondary coil.
- This principle is used in applications like ignition systems (e.g., spark plugs in gasoline engines) and high-voltage power supplies for scientific equipment.
-
Use in Ignition Systems
- In automotive applications, induction coils are critical components of ignition systems.
- They generate the high voltage needed to create a spark in the spark plug, enabling the combustion of fuel in gasoline engines.
- This ensures efficient and reliable engine performance.
-
Design and Customization
- The performance of an induction coil depends on its design, including the number of turns, coil diameter, and material.
- Custom coils can be designed for specific applications, such as high-frequency heating or low-frequency power generation.
- Proper cooling and insulation are also essential to maintain efficiency and prevent overheating.
-
Advantages of Induction Coils
- Efficiency: Induction heating is highly energy-efficient compared to traditional methods like gas or resistance heating.
- Precision: The process allows for precise temperature control, reducing the risk of overheating or underheating.
- Safety: Since the coil itself does not get hot, the risk of burns or fires is minimized.
- Versatility: Induction coils can be adapted for a wide range of applications, from small-scale laboratory setups to large industrial systems.
-
Limitations and Considerations
- Induction coils require a power source capable of delivering the necessary current and frequency.
- The effectiveness of the coil depends on the material being heated; non-conductive or weakly conductive materials may not respond well.
- Proper maintenance and cooling are essential to ensure long-term reliability and performance.
By understanding these key points, users can make informed decisions about selecting and using induction coils for their specific needs, whether in industrial, automotive, or scientific applications.
Summary Table:
Aspect | Details |
---|---|
Principle of Operation | Electromagnetic induction generates a magnetic field, inducing eddy currents in conductive materials. |
Applications | Heating and melting metals, high-voltage generation, and automotive ignition systems. |
Advantages | High efficiency, precise temperature control, safety, and versatility. |
Limitations | Requires compatible power sources; less effective for non-conductive materials. |
Design Considerations | Coil turns, diameter, material, cooling, and insulation are critical factors. |
Need a custom induction coil for your application? Contact our experts today to find the perfect solution!