Hydraulic pressure spikes are sudden, sharp increases in pressure within a hydraulic system that can lead to equipment damage, reduced efficiency, and safety hazards. These spikes are typically caused by rapid changes in fluid flow, mechanical failures, or system design flaws. Understanding the root causes of hydraulic pressure spikes is essential for preventing them and ensuring the longevity and reliability of hydraulic systems. Common causes include rapid valve closures, trapped air, pump cavitation, and improper system design. By addressing these issues, operators can minimize the risk of pressure spikes and maintain optimal system performance.
Key Points Explained:
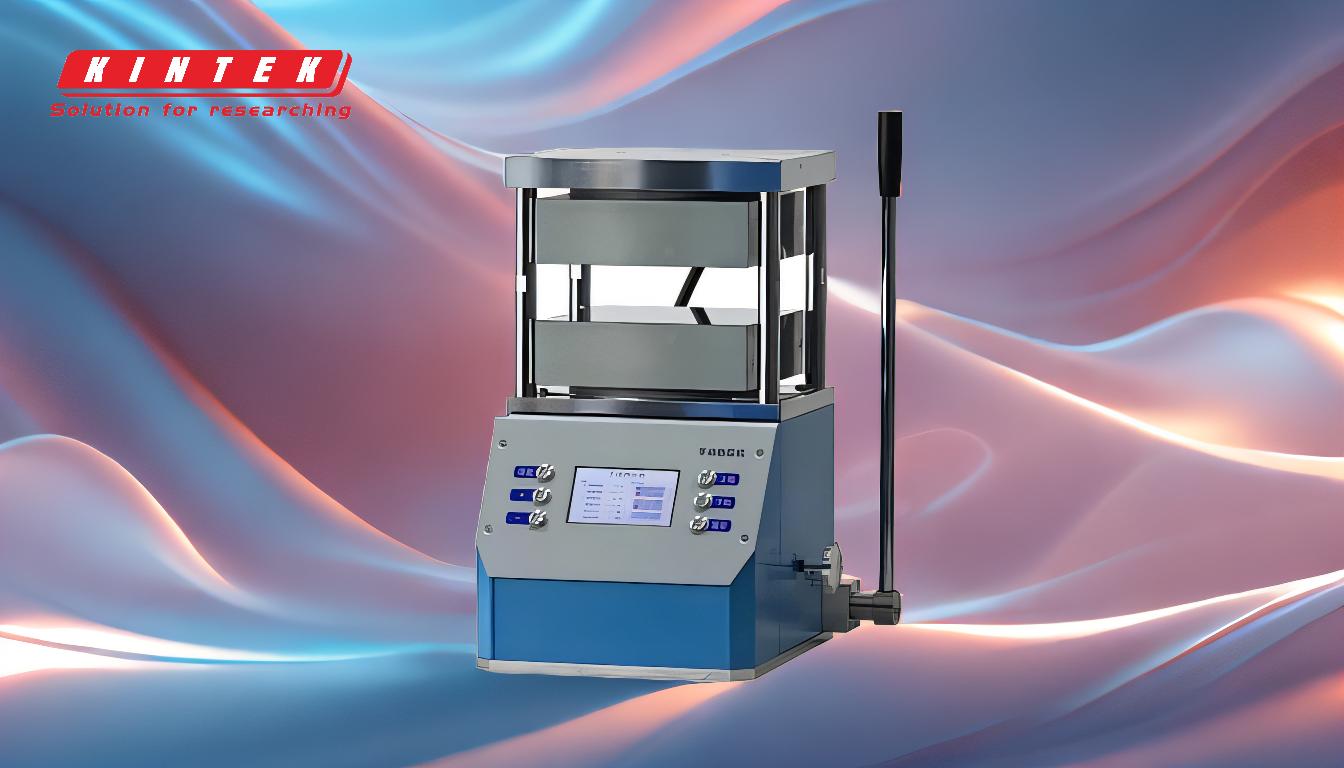
-
Rapid Valve Closure:
- When a valve in a hydraulic system closes too quickly, it can cause a sudden stoppage of fluid flow, leading to a pressure spike. This phenomenon is known as water hammer.
- The kinetic energy of the moving fluid is converted into pressure energy, resulting in a sharp increase in pressure that can damage system components.
- To mitigate this, use valves with slower closing times or install accumulators to absorb the shock.
-
Trapped Air in the System:
- Air trapped in the hydraulic fluid can compress and expand rapidly, causing pressure fluctuations and spikes.
- Air can enter the system through leaks, improper bleeding, or during maintenance.
- Regularly bleeding the system and ensuring proper sealing can help prevent air from entering and causing pressure spikes.
-
Pump Cavitation:
- Cavitation occurs when the pressure in the hydraulic fluid drops below its vapor pressure, causing bubbles to form and collapse rapidly.
- This collapse generates shock waves that can lead to pressure spikes and damage to pump components.
- Ensuring adequate fluid supply, maintaining proper pump speed, and using fluids with appropriate viscosity can help prevent cavitation.
-
Improper System Design:
- Poorly designed hydraulic systems can lead to pressure spikes due to inadequate sizing of components, improper placement of valves, or insufficient damping mechanisms.
- A well-designed system should include properly sized pipes, valves, and accumulators to handle expected pressure variations.
- Consulting with hydraulic system experts during the design phase can help avoid these issues.
-
Fluid Contamination:
- Contaminants in the hydraulic fluid, such as dirt, water, or metal particles, can cause blockages or wear on system components, leading to pressure spikes.
- Regular maintenance, including fluid filtration and replacement, is essential to prevent contamination-related issues.
- Using high-quality fluids and filters can also help maintain system integrity.
-
Temperature Fluctuations:
- Extreme temperature changes can affect the viscosity and compressibility of hydraulic fluid, leading to pressure spikes.
- Maintaining a stable operating temperature through proper cooling and insulation can help prevent these fluctuations.
- Monitoring temperature and adjusting system parameters as needed can also mitigate the risk of pressure spikes.
-
Mechanical Failures:
- Worn or damaged components, such as seals, hoses, or cylinders, can fail unexpectedly, causing sudden pressure changes.
- Regular inspection and maintenance of system components can help identify and address potential failures before they cause pressure spikes.
- Replacing worn parts and ensuring proper installation can also reduce the risk of mechanical failures.
By understanding and addressing these key causes of hydraulic pressure spikes, operators can take proactive measures to protect their systems, improve performance, and extend the lifespan of hydraulic equipment. Regular maintenance, proper system design, and the use of high-quality components are essential for minimizing the risk of pressure spikes and ensuring the reliable operation of hydraulic systems.
Summary Table:
Cause | Description | Prevention |
---|---|---|
Rapid Valve Closure | Sudden stoppage of fluid flow causing pressure spikes (water hammer). | Use slower-closing valves or install accumulators. |
Trapped Air | Air compresses and expands, causing pressure fluctuations. | Regularly bleed the system and ensure proper sealing. |
Pump Cavitation | Bubbles form and collapse, generating shock waves. | Maintain adequate fluid supply, proper pump speed, and use appropriate viscosity fluids. |
Improper System Design | Poorly sized components or insufficient damping mechanisms. | Consult experts for proper system design and component sizing. |
Fluid Contamination | Contaminants block or wear components, leading to pressure spikes. | Use high-quality fluids, filters, and perform regular maintenance. |
Temperature Fluctuations | Extreme temperature changes affect fluid viscosity and compressibility. | Maintain stable operating temperatures with proper cooling and insulation. |
Mechanical Failures | Worn or damaged components fail, causing sudden pressure changes. | Regularly inspect and replace worn parts, ensuring proper installation. |
Need help preventing hydraulic pressure spikes? Contact our experts today for tailored solutions!