A vacuum furnace is a specialized heating device designed to operate in a vacuum environment, enabling precise control over temperature and atmospheric conditions. It is widely used in industries such as material science, electronics, metallurgy, and chemical engineering for processes like heat treatment, sintering, brazing, and annealing. By eliminating oxygen and other reactive gases, a vacuum furnace prevents oxidation and contamination, ensuring high-quality results. Its applications range from hardening metals to sintering refractory alloys and brazing delicate components. The furnace's structure typically includes a sealed chamber, heating elements, vacuum systems, and temperature control mechanisms, making it indispensable for advanced material processing and research.
Key Points Explained:
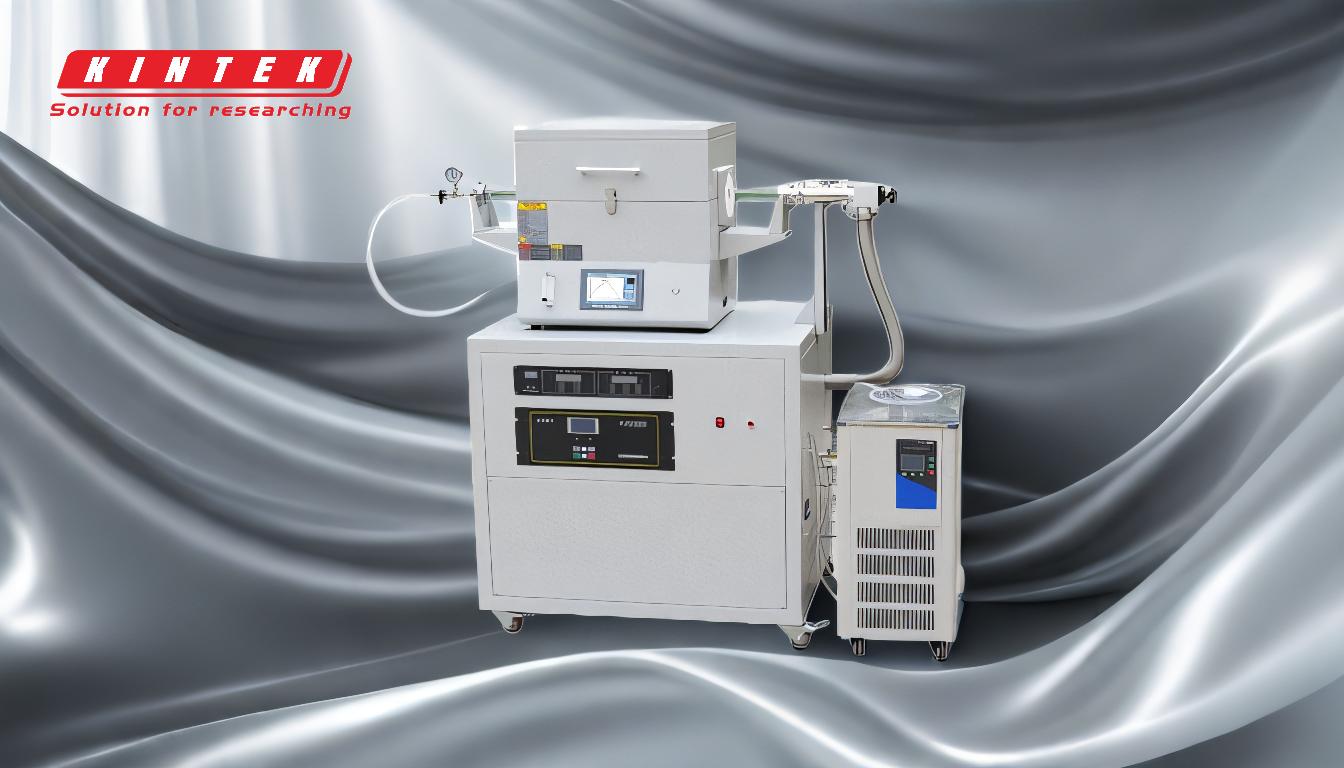
-
Purpose and Applications of a Vacuum Furnace
- A vacuum furnace is primarily used to heat materials to extremely high temperatures in a controlled, oxygen-free environment.
- Common applications include:
- Heat Treatment: Processes like vacuum quenching, tempering, and annealing to enhance material properties such as hardness, strength, and durability.
- Sintering: Heating metal powders in a vacuum to bond particles into solid components without melting the entire material.
- Brazing: Joining metals by heating them above the melting point of a filler metal but below the melting point of the base metals.
- Ceramic Firing and Metal Sealing: Used in advanced manufacturing for ceramics and semiconductor components.
-
Advantages of a Vacuum Environment
- Prevents Oxidation: The absence of oxygen eliminates the risk of oxidation, ensuring clean and uncontaminated surfaces.
- Reduces Contamination: A vacuum environment minimizes impurities, making it ideal for high-purity materials and processes.
- Uniform Heating: The vacuum allows for even heat distribution, critical for achieving consistent material properties.
-
Key Functions of a Vacuum Furnace
- Vacuum Quenching: Rapidly cooling heated materials to achieve desired mechanical properties, such as increased hardness.
- Vacuum Annealing: Heating materials to specific temperatures and then slowly cooling them to improve ductility and reduce internal stresses.
- Vacuum Sintering: Bonding metal powders into solid components by heating them below their melting point, often used for refractory metals like tungsten and molybdenum.
- Vacuum Brazing: Joining metal parts using a filler metal that melts at a lower temperature than the base metals, ensuring strong, clean joints.
-
Structural Components of a Vacuum Furnace
- Furnace Chamber: The sealed enclosure where materials are heated, designed to withstand high temperatures and maintain a vacuum.
- Heating Elements: Typically made of materials like graphite or tungsten, capable of reaching extremely high temperatures.
- Vacuum System: Includes pumps and seals to create and maintain the vacuum environment.
- Temperature Control System: Ensures precise regulation of heating and cooling cycles.
- Transport System: Allows for easy loading and unloading of materials.
-
Industrial Uses and Benefits
- Material Science: Used for research and development of advanced materials, including alloys and ceramics.
- Electronics: Essential for manufacturing semiconductors and other electronic components requiring high purity.
- Metallurgy: Critical for processing metals like titanium, stainless steel, and superalloys.
- Chemical Industry: Used for degassing and purifying materials.
-
Specialized Types of Vacuum Furnaces
- Vacuum Sintering Furnace: Designed for sintering refractory metals and alloys, often used in the production of cutting tools and aerospace components.
- Vacuum Brazing Furnace: Ideal for joining complex or delicate parts in industries like aerospace and automotive.
- Vacuum Heat Treatment Furnace: Used for hardening and tempering metals to improve their performance.
-
Operational Considerations
- Temperature Range: Vacuum furnaces can operate at temperatures ranging from a few hundred degrees to over 2000°C, depending on the application.
- Cooling Methods: Various cooling techniques, such as gas quenching or oil quenching, are used to achieve specific material properties.
- Maintenance: Regular upkeep of vacuum pumps, seals, and heating elements is essential to ensure consistent performance.
In summary, a vacuum furnace is a versatile and essential tool for high-temperature processing in a controlled environment. Its ability to prevent oxidation, ensure uniform heating, and handle a wide range of materials makes it indispensable in industries requiring precision and high-quality results. Whether for sintering, brazing, or heat treatment, a vacuum furnace plays a critical role in advancing material science and manufacturing technologies.
Summary Table:
Aspect | Details |
---|---|
Applications | Heat treatment, sintering, brazing, annealing, ceramic firing, metal sealing |
Advantages | Prevents oxidation, reduces contamination, ensures uniform heating |
Key Functions | Vacuum quenching, annealing, sintering, brazing |
Structural Components | Furnace chamber, heating elements, vacuum system, temperature control |
Industrial Uses | Material science, electronics, metallurgy, chemical engineering |
Specialized Types | Sintering furnace, brazing furnace, heat treatment furnace |
Learn how a vacuum furnace can elevate your material processing—contact our experts today!