Heat treatment is a controlled process used to alter the mechanical properties of metallic alloys by manipulating their microstructure. By carefully managing the rate of diffusion and cooling, heat treatment can enhance properties such as hardness, strength, toughness, ductility, and elasticity. This process is critical in industries where material performance under stress, wear, or temperature variations is paramount. Heat treatment techniques, such as annealing, quenching, and tempering, are tailored to achieve specific material characteristics, making it a versatile and essential process in manufacturing and engineering.
Key Points Explained:
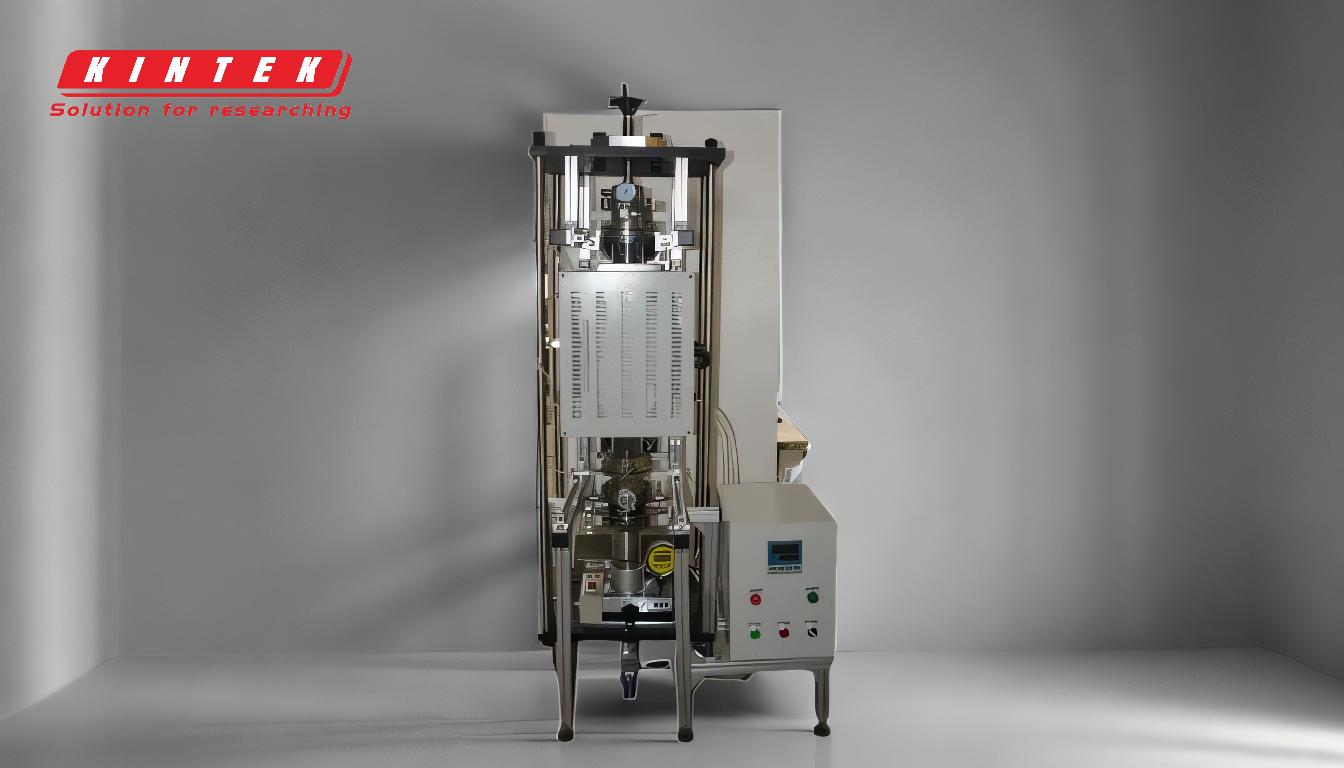
-
Alters Mechanical Properties:
- Heat treatment modifies key mechanical properties of metallic alloys, including hardness, strength, toughness, ductility, and elasticity. These changes are achieved by altering the material's microstructure through controlled heating and cooling processes.
- For example, increasing hardness often involves rapid cooling (quenching), while improving ductility might require slow cooling (annealing).
-
Manipulates Microstructure:
- The microstructure of a metal, which includes its grain size and phase composition, determines its mechanical properties. Heat treatment allows for precise control over these microstructural features.
- Processes like diffusion (movement of atoms within the material) and recrystallization (formation of new grains) are critical in achieving desired material characteristics.
-
Controlled Heating and Cooling Rates:
- The rate of heating and cooling is a critical factor in heat treatment. Faster cooling rates, such as in quenching, typically increase hardness and strength but may reduce ductility. Slower cooling rates, as in annealing, enhance ductility and reduce internal stresses.
- The ability to control these rates allows engineers to tailor materials for specific applications, such as high-strength components in aerospace or wear-resistant tools in manufacturing.
-
Enhances Material Performance:
- Heat treatment improves the performance of materials under various conditions, such as high stress, wear, or temperature fluctuations. For instance, tempered steel combines strength and toughness, making it suitable for tools and machinery.
- This process is essential in industries like automotive, aerospace, and construction, where material reliability and durability are critical.
-
Versatility in Applications:
- Different heat treatment techniques (e.g., annealing, quenching, tempering, case hardening) are used to achieve specific outcomes. This versatility makes heat treatment applicable to a wide range of materials and industries.
- For example, case hardening is used to create a hard outer surface while maintaining a tough inner core, ideal for gears and bearings.
-
Critical for Manufacturing and Engineering:
- Heat treatment is a cornerstone of modern manufacturing and engineering. It ensures that materials meet the required specifications for strength, durability, and performance.
- Without heat treatment, many advanced engineering applications would not be possible, as untreated materials often lack the necessary properties to withstand operational demands.
By understanding these key points, a purchaser of equipment or consumables can better appreciate the importance of heat treatment in ensuring the quality and performance of materials used in their applications.
Summary Table:
Key Aspect | Description |
---|---|
Alters Mechanical Properties | Modifies hardness, strength, toughness, ductility, and elasticity via microstructure changes. |
Manipulates Microstructure | Controls grain size and phase composition for desired material characteristics. |
Controlled Heating/Cooling | Adjusts rates to tailor properties (e.g., quenching for hardness, annealing for ductility). |
Enhances Performance | Improves material reliability under stress, wear, and temperature variations. |
Versatile Applications | Techniques like annealing, tempering, and case hardening suit diverse industries. |
Critical for Engineering | Ensures materials meet strength and durability requirements for advanced applications. |
Optimize your material performance with expert heat treatment solutions—contact us today!