Hydrogen annealing is a specialized heat treatment process conducted in a controlled hydrogen atmosphere, typically at elevated temperatures (200-300°C). It serves multiple purposes, including preventing oxidation, reducing surface oxides, relieving internal stresses, and addressing hydrogen embrittlement. The process is often referred to as "bright annealing" due to its ability to produce a clean, oxidation-free surface. However, it requires careful handling, as hydrogen can decarburize steel and is more expensive compared to other annealing atmospheres. Nitrogen-hydrogen blends are sometimes used as a cost-effective alternative. Additionally, low hydrogen annealing (or "baking") is employed to reduce hydrogen content in materials, preventing hydrogen embrittlement and improving mechanical properties.
Key Points Explained:
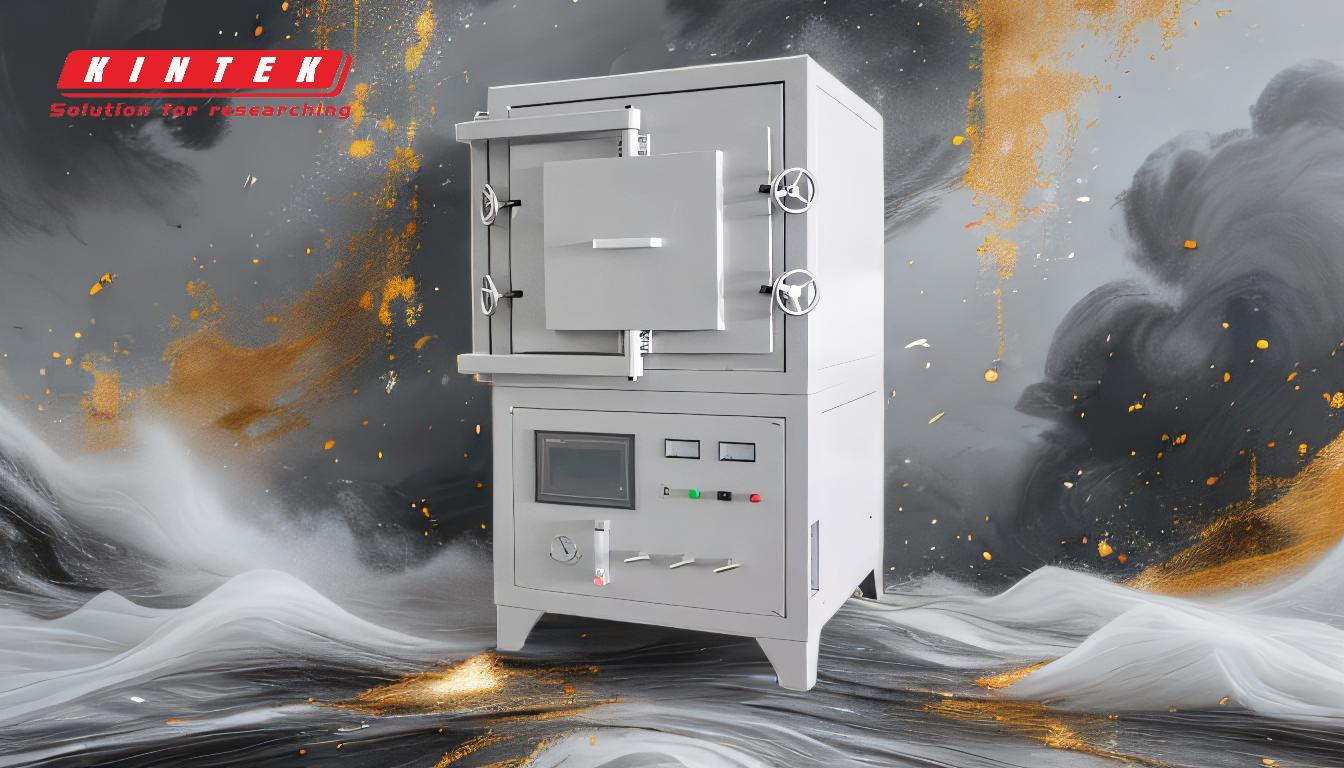
-
Definition and Purpose of Hydrogen Annealing:
- Hydrogen annealing is a heat treatment process performed in a 100% hydrogen atmosphere, typically at temperatures between 200-300°C.
- Its primary purposes include:
- Preventing oxidation and product discoloration.
- Reducing surface oxides through the reducing properties of hydrogen.
- Relieving internal stresses caused by fabrication processes like casting.
- Addressing hydrogen embrittlement in certain materials.
-
Bright Annealing and Surface Cleaning:
- Hydrogen annealing is often called "bright annealing" because it produces a clean, oxidation-free surface.
- Hydrogen acts as a reducing gas, removing oxides from the surface of metal parts, which is particularly useful for wires and other components requiring a pristine finish.
-
Potential Risks and Precautions:
- Hydrogen can decarburize steel, leading to a loss of carbon content and potentially weakening the material.
- Precautions must be taken to minimize this effect, especially when annealing carbon-rich steels.
- The process is expensive due to the cost of maintaining a pure hydrogen atmosphere, but nitrogen-hydrogen blends offer a more economical alternative.
-
Low Hydrogen Annealing (Baking):
- Low hydrogen annealing, also known as "baking," is a specific type of hydrogen annealing aimed at reducing or eliminating hydrogen in materials to prevent hydrogen embrittlement.
- Hydrogen embrittlement is a phenomenon where hydrogen atoms diffuse into the metal lattice, causing cracking and degrading mechanical properties such as plasticity, ductility, and fracture toughness.
- This process is particularly important for materials like steel, which are susceptible to hydrogen-induced cracking.
-
Impact on Mechanical Properties:
- Low hydrogen annealing can significantly alter the mechanical properties of materials. For example:
- In X80 pipeline steel, annealing at 200°C for 12 hours increases yield strength by approximately 10% but decreases elongation by about 20%.
- This is due to the formation of a Cottrell atmosphere, where carbon atoms diffuse into interstitial sites of dislocations, pinning them and reducing the density of movable dislocations.
- While effective for reducing internal hydrogen embrittlement, this process may not address hydrogen embrittlement caused by surface-absorbed hydrogen.
- Low hydrogen annealing can significantly alter the mechanical properties of materials. For example:
-
Applications and Alternatives:
- Hydrogen annealing is widely used in industries requiring high-quality surface finishes and stress relief, such as wire manufacturing and casting.
- Due to the high cost of pure hydrogen, nitrogen-hydrogen blends are often used as a cost-effective alternative, though they may not provide the same level of surface cleaning.
-
Process Parameters:
- Temperature: Typically ranges between 200-300°C, depending on the material and desired outcomes.
- Atmosphere: 100% hydrogen or nitrogen-hydrogen blends.
- Duration: Varies based on material thickness and specific requirements, such as 12 hours for low hydrogen annealing of X80 pipeline steel.
-
Advantages and Limitations:
- Advantages:
- Produces a clean, oxidation-free surface.
- Relieves internal stresses and reduces hydrogen embrittlement.
- Limitations:
- Risk of decarburization in steel.
- High cost of maintaining a pure hydrogen atmosphere.
- Limited effectiveness against surface-absorbed hydrogen embrittlement.
- Advantages:
By understanding these key points, equipment and consumable purchasers can make informed decisions about when and how to use hydrogen annealing, balancing its benefits against potential risks and costs.
Summary Table:
Aspect | Details |
---|---|
Purpose | Prevents oxidation, reduces surface oxides, relieves stress, addresses embrittlement. |
Temperature Range | 200-300°C |
Atmosphere | 100% hydrogen or nitrogen-hydrogen blends |
Key Benefits | Clean surface, stress relief, reduced hydrogen embrittlement. |
Risks | Decarburization of steel, high cost, limited effectiveness on surface-absorbed hydrogen. |
Applications | Wire manufacturing, casting, and industries requiring high-quality finishes. |
Discover how hydrogen annealing can optimize your material processing—contact our experts today!