Physical Vapor Deposition (PVD) is a sophisticated manufacturing process used to apply thin-film coatings to various substrates, enhancing their durability, functionality, and aesthetics. This vacuum-based technique involves the vaporization of a solid material, which is then deposited onto a substrate to form a thin, uniform layer. PVD is widely used in industries such as aerospace, automotive, and electronics, where it improves wear resistance, corrosion resistance, and other functional properties of components. The process involves multiple steps, including vaporization, migration, and deposition, and can utilize techniques like sputter deposition and ion plating. PVD is particularly valued for its ability to produce high-quality, durable coatings at relatively low temperatures, making it suitable for a wide range of applications.
Key Points Explained:
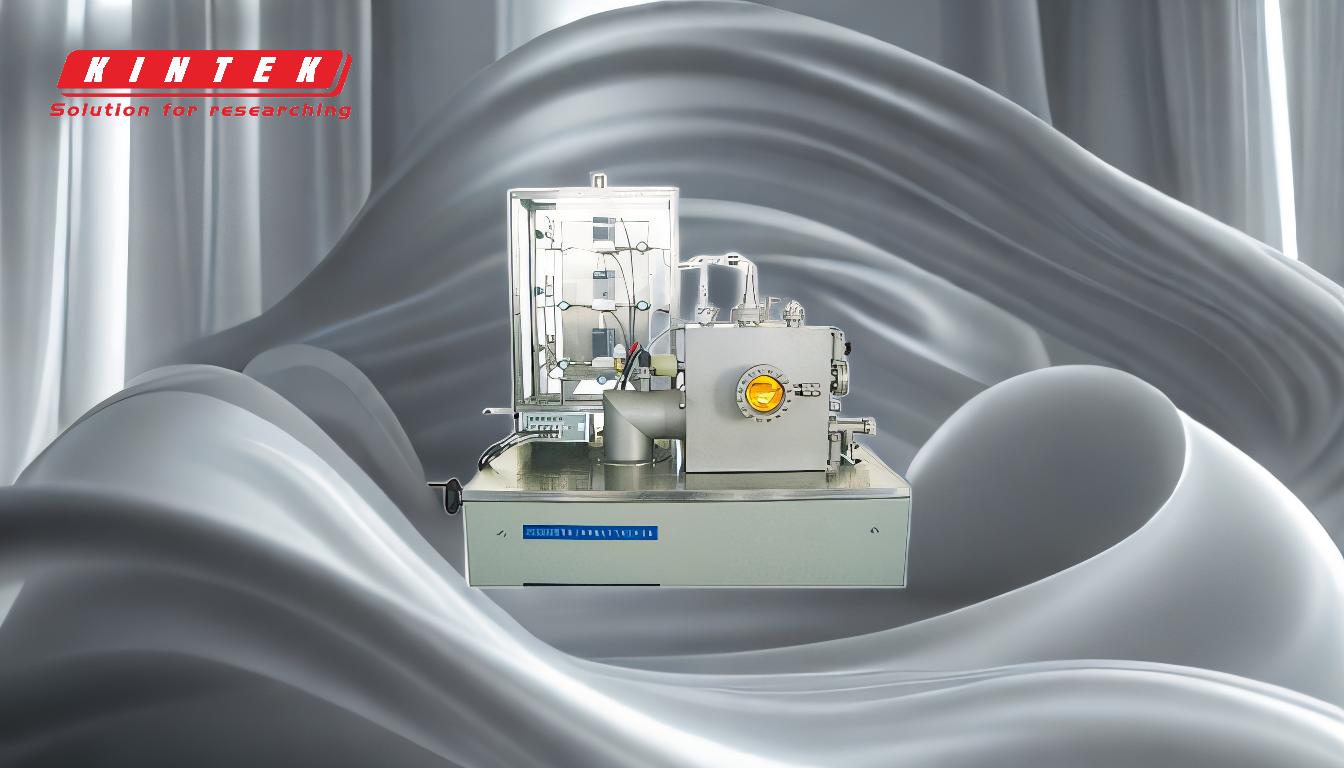
-
Definition of PVD:
- Physical Vapor Deposition (PVD) is a surface modification technique used in metalworking and other industries to apply thin-film coatings. These coatings enhance the durability, functionality, and appearance of the substrate.
-
Basic Steps in the PVD Process:
- Vaporization: The coating material is vaporized through methods such as evaporation, sputtering, or laser ablation. This step involves converting the solid material into a vapor state.
- Migration: The vaporized atoms or molecules migrate through a vacuum or low-pressure environment. During this phase, they may undergo reactions with other gases introduced into the chamber.
- Deposition: The atoms or molecules condense onto the substrate, forming a thin, uniform coating. This step typically occurs at relatively low temperatures, which helps preserve the integrity of the substrate.
-
Techniques Used in PVD:
- Sputter Deposition: A technique where atoms are ejected from a solid target material due to bombardment by high-energy ions. These ejected atoms then deposit onto the substrate.
- Ion Plating: A method that combines sputtering with a plasma environment to enhance the adhesion and density of the deposited film. This technique is particularly useful for achieving high-quality coatings with excellent mechanical properties.
-
Applications of PVD:
- Semiconductor Devices: PVD is used to deposit thin films in the production of semiconductor devices, such as thin-film solar panels and integrated circuits.
- Food Packaging: Aluminized PET film, created using PVD, is commonly used in food packaging and balloons due to its barrier properties and lightweight nature.
- Cutting Tools: Titanium nitride (TiN) coatings applied via PVD significantly improve the wear resistance and lifespan of cutting tools used in metalworking.
- Aerospace and Automotive: PVD coatings are applied to engine and chassis components to enhance their wear and corrosion resistance, which is critical for the longevity and performance of these parts.
-
Advantages of PVD:
- Durability: PVD coatings are known for their hardness and resistance to wear, making them ideal for high-stress applications.
- Corrosion Resistance: The coatings provide excellent protection against corrosion, which is essential for components exposed to harsh environments.
- Aesthetic Appeal: PVD can produce coatings with a variety of colors and finishes, enhancing the visual appeal of the coated items.
- Environmental Friendliness: PVD processes are generally more environmentally friendly compared to traditional coating methods, as they often involve fewer hazardous chemicals and produce less waste.
-
Process Conditions:
- Vacuum Environment: PVD is performed under high vacuum conditions to ensure the purity and quality of the deposited films. The vacuum environment minimizes contamination and allows for precise control over the deposition process.
- Low Temperatures: The process typically operates at relatively low temperatures, which is beneficial for substrates that may be sensitive to high heat.
-
Material Versatility:
- PVD can be used with a wide range of materials, including metals, alloys, and ceramics. This versatility allows for the creation of coatings with tailored properties to meet specific application requirements.
-
Industry-Specific Benefits:
- Electronics: In the electronics industry, PVD is crucial for the deposition of conductive and insulating layers in microelectronic devices.
- Medical Devices: PVD coatings are used in medical devices to improve biocompatibility and reduce wear, which is essential for implants and surgical instruments.
- Decorative Applications: PVD is also employed in decorative applications, such as coating watches, jewelry, and architectural elements, where both durability and aesthetics are important.
In summary, PVD is a highly versatile and effective manufacturing process that plays a critical role in enhancing the performance and longevity of various components across multiple industries. Its ability to produce durable, high-quality coatings at relatively low temperatures makes it a preferred choice for many applications.
Summary Table:
Key Aspect | Details |
---|---|
Definition | A vacuum-based technique for applying thin-film coatings to substrates. |
Process Steps | Vaporization, migration, and deposition. |
Techniques | Sputter deposition, ion plating. |
Applications | Semiconductor devices, food packaging, cutting tools, aerospace components. |
Advantages | Durability, corrosion resistance, aesthetic appeal, eco-friendliness. |
Process Conditions | High vacuum, low temperatures. |
Material Versatility | Metals, alloys, ceramics. |
Industry Benefits | Electronics, medical devices, decorative applications. |
Unlock the potential of PVD coatings for your industry—contact our experts today to learn more!