PVD sputtering is a specialized technique within the broader Physical Vapor Deposition (PVD) process, used to deposit thin films of material onto a substrate. This method involves bombarding a target material with high-energy ions, typically from a noble gas like argon, to eject atoms from the target. These ejected atoms then form a vapor that deposits onto the substrate, creating a thin, uniform film. PVD sputtering is widely used in industries such as semiconductors, optical devices, and coatings for glass and tools, offering benefits like improved wear resistance, hardness, and aesthetic appeal. The process is highly controlled, requiring specialized equipment to manage heat and ensure even deposition.
Key Points Explained:
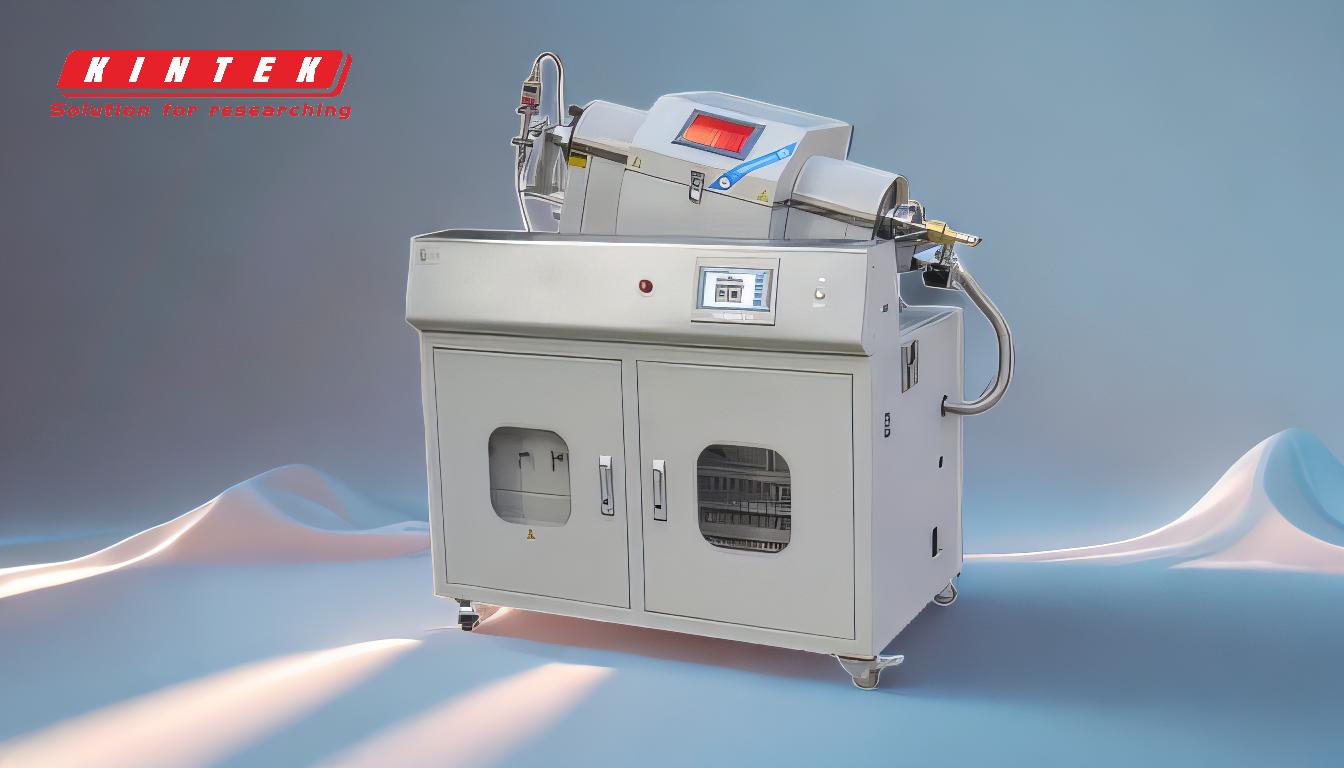
-
Definition of PVD Sputtering:
- PVD sputtering is a method within Physical Vapor Deposition where a target material is bombarded with high-energy ions, typically argon, to eject atoms. These atoms form a vapor that deposits onto a substrate, creating a thin film.
- This process is distinct from other PVD methods like electron-beam evaporation, as it relies on kinetic energy rather than heat to vaporize the target material.
-
How Sputtering Works:
- A noble gas, usually argon, is introduced into a vacuum chamber, and a plasma is ignited.
- The target material is electrically charged, causing argon ions to accelerate toward it.
- The high-energy collisions between argon ions and the target eject atoms from the target surface.
- These ejected atoms travel through the chamber and deposit onto the substrate, forming a thin film.
-
Applications of PVD Sputtering:
- Semiconductors: Used for depositing thin films in semiconductor circuits and thin-film transistors.
- Optical Devices: Applied in anti-reflective coatings for eyeglasses and architectural glass.
- Data Storage: Utilized in the production of CDs, DVDs, and disk drives.
- Industrial Tools: Enhances wear resistance and hardness in cutting tools and machinery components.
- Aesthetic Coatings: Used in jewelry and decorative glass to improve appearance and durability.
-
Advantages of PVD Sputtering:
- High-Quality Films: Produces uniform, high-purity films with excellent adhesion to the substrate.
- Versatility: Can deposit a wide range of materials, including metals, alloys, and ceramics.
- Controlled Deposition: Allows precise control over film thickness, ranging from nanometers to micrometers.
- No Chemical Reactions: Since a noble gas is used, the process is purely physical, avoiding unwanted chemical reactions.
-
Equipment and Process Requirements:
- Vacuum Chamber: Essential to maintain a controlled environment free from contaminants.
- Power Supply: Provides the electrical charge needed to create the plasma and accelerate ions.
- Cooling Systems: Manages the heat generated during the sputtering process to prevent damage to the equipment and ensure consistent results.
- Substrate Rotation: Ensures even coating by rotating the substrate during deposition, particularly important for complex shapes.
-
Comparison with Other PVD Methods:
- Unlike electron-beam PVD, which uses heat to vaporize the target material, sputtering relies on kinetic energy from ion bombardment.
- Sputtering is often preferred for materials with high melting points or those that are difficult to evaporate using thermal methods.
-
Industry-Specific Uses:
- Microelectronics: Critical for creating thin films in chip manufacturing and integrated circuits.
- Architectural Glass: Used for low-emissivity coatings that improve energy efficiency in buildings.
- Food Industry: Applied in packaging materials to enhance barrier properties and extend shelf life.
- Entertainment Electronics: Used in the production of hard drives and optical media.
In summary, PVD sputtering is a highly versatile and precise method for depositing thin films, offering numerous advantages in terms of quality, control, and material compatibility. Its applications span a wide range of industries, making it a cornerstone of modern manufacturing and technology.
Summary Table:
Aspect | Details |
---|---|
Definition | A PVD method using ion bombardment to deposit thin films on substrates. |
Process | Argon ions bombard a target, ejecting atoms that form a vapor and deposit. |
Applications | Semiconductors, optical devices, data storage, industrial tools, coatings. |
Advantages | High-quality films, versatility, controlled deposition, no chemical reactions. |
Equipment | Vacuum chamber, power supply, cooling systems, substrate rotation. |
Comparison | Relies on kinetic energy, not heat, making it ideal for high-melting materials. |
Discover how PVD sputtering can elevate your manufacturing process—contact our experts today!