Sintering is a critical process in ceramic manufacturing that transforms ceramic powder into a dense, strong, and functional material. By applying high temperatures, sintering facilitates particle bonding, reduces porosity, and enhances material properties such as strength, thermal conductivity, and electrical conductivity. This process results in a uniform microstructure, stable shape, and improved mechanical and functional characteristics. Sintering also enables the production of complex geometries and intricate shapes, making it indispensable for advanced ceramic applications. The process directly influences grain size, pore distribution, and grain boundary formation, which collectively determine the final properties of the ceramic material.
Key Points Explained:
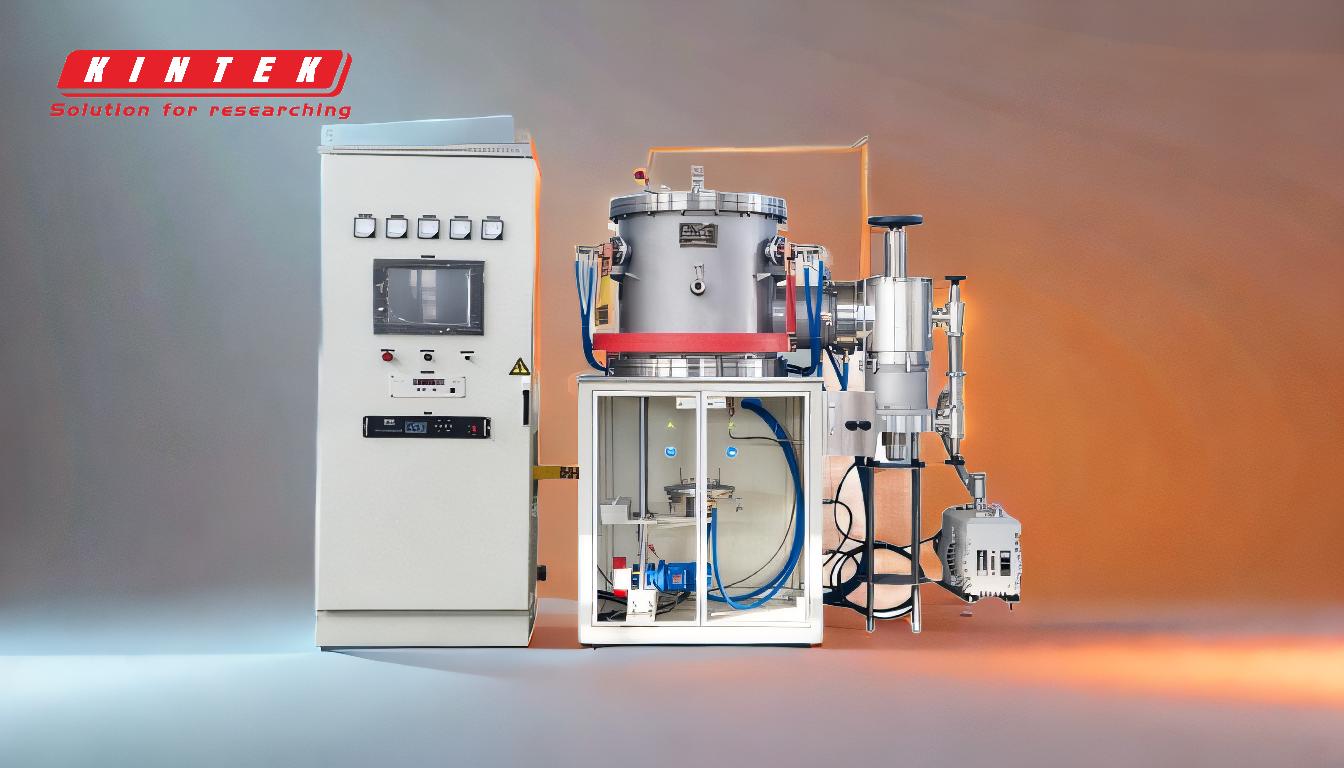
-
Transformation of Ceramic Powder into Dense Material:
- Sintering converts loose ceramic powder into a dense, polycrystalline ceramic material.
- Through diffusion and mass transfer, particles bond together, reducing porosity and increasing density.
- This densification results in a stable shape and uniform microstructure, essential for achieving desired mechanical and functional properties.
-
Mechanism of Sintering:
- During sintering, ceramic powder particles undergo material migration and grain boundary movement under high temperatures.
- Over time, the particles bond, grains grow, and voids decrease, leading to volume shrinkage and increased density.
- This process forms a hard, polycrystalline sintered body with specific microstructural characteristics.
-
Impact on Material Properties:
- Sintering enhances key properties such as strength, toughness, hardness, and thermal and electrical conductivity.
- It reduces porosity, which improves durability and resistance to wear and corrosion.
- The process also influences grain size, pore size, and grain boundary distribution, which directly affect the material's performance.
-
Importance in Advanced Ceramics:
- Sintering is crucial for producing advanced ceramics with precise geometries and intricate shapes.
- It enables the combination of multiple material properties, such as toughness and abrasion resistance, in a single component.
- The process supports cost-effective manufacturing of complex parts and facilitates rapid mass production while maintaining precision.
-
Optimization of Sintering:
- An optimized sintering process ensures the achievement of desired physical properties in the final product.
- Factors such as temperature, time, and atmosphere are carefully controlled to achieve specific microstructural and property outcomes.
- Proper optimization leads to consistent quality, repeatability, and performance in ceramic components.
-
Applications and Benefits:
- Sintering is used in various industries, including electronics, aerospace, and medical devices, to produce high-performance ceramic components.
- It allows for the creation of materials with high melting points without the need for melting, enabling the production of durable and heat-resistant products.
- The process supports the development of innovative materials with tailored properties for specific applications.
By understanding the sintering process and its effects on ceramics, manufacturers can produce materials with enhanced properties, enabling the creation of advanced and high-performance products.
Summary Table:
Key Aspect | Description |
---|---|
Transformation | Converts ceramic powder into dense, polycrystalline material. |
Mechanism | Particle bonding, grain growth, and porosity reduction under high temperatures. |
Material Properties | Enhances strength, toughness, conductivity, and durability. |
Advanced Applications | Enables precise geometries and complex shapes for high-performance ceramics. |
Optimization | Controlled temperature, time, and atmosphere for consistent quality. |
Benefits | Cost-effective, durable, and heat-resistant materials for various industries. |
Discover how sintering can elevate your ceramic manufacturing—contact our experts today!