The deposition rate in various processes, such as chemical vapor deposition (CVD) or physical vapor deposition (PVD), depends on several factors, including the material being deposited, the process parameters, and the equipment used. These factors influence how quickly and uniformly a thin film or coating is formed on a substrate. Key determinants include the type of precursor or target material, temperature, pressure, gas flow rates, and the energy source used in the process. Understanding these dependencies is crucial for optimizing deposition processes to achieve desired film properties, such as thickness, uniformity, and adhesion.
Key Points Explained:
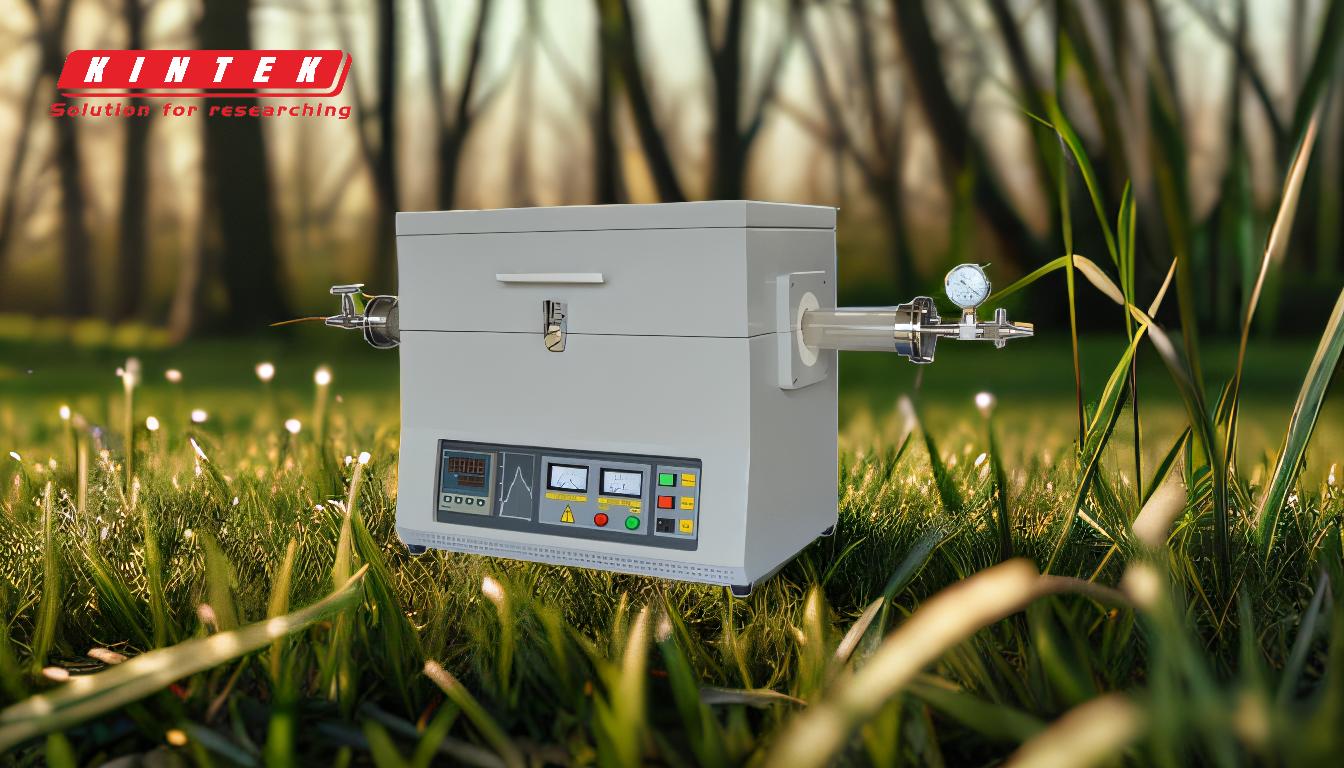
-
Material Properties:
- The type of precursor or target material significantly affects the deposition rate. For example, materials with higher vapor pressures or lower melting points tend to deposit faster. The chemical reactivity of the precursor also plays a role, as more reactive precursors can lead to higher deposition rates.
-
Process Temperature:
- Temperature is a critical factor in deposition processes. Higher temperatures generally increase the kinetic energy of the atoms or molecules, leading to faster deposition. However, excessively high temperatures can also cause unwanted reactions or degrade the substrate.
-
Pressure and Gas Flow Rates:
- The pressure inside the deposition chamber and the flow rates of reactive gases influence the deposition rate. Lower pressures can enhance the mean free path of particles, improving deposition uniformity, while higher gas flow rates can increase the availability of reactive species, speeding up the process.
-
Energy Source:
- The type of energy source used, such as plasma, laser, or thermal energy, affects the deposition rate. For instance, plasma-enhanced CVD (PECVD) can achieve higher deposition rates at lower temperatures compared to thermal CVD due to the increased reactivity of plasma-activated species.
-
Substrate Characteristics:
- The substrate's surface properties, such as roughness, cleanliness, and temperature, can influence the deposition rate. A smoother and cleaner surface often leads to better adhesion and more uniform deposition.
-
Equipment Design:
- The design of the deposition equipment, including the chamber geometry, target-to-substrate distance, and the efficiency of gas delivery systems, can impact the deposition rate. Optimized equipment design ensures better control over process parameters.
-
Process Control and Parameters:
- Precise control over process parameters, such as power input, gas composition, and deposition time, is essential for achieving consistent deposition rates. Advanced control systems can help maintain optimal conditions throughout the process.
By carefully considering these factors, manufacturers and researchers can optimize deposition processes to achieve the desired film properties and improve overall efficiency.
Summary Table:
Factor | Impact on Deposition Rate |
---|---|
Material Properties | Higher vapor pressure or reactivity increases deposition rate. |
Process Temperature | Higher temperatures generally speed up deposition but may risk substrate damage. |
Pressure & Gas Flow Rates | Lower pressure improves uniformity; higher gas flow rates increase reactive species availability. |
Energy Source | Plasma-enhanced methods (e.g., PECVD) achieve faster rates at lower temperatures. |
Substrate Characteristics | Smoother, cleaner surfaces enhance adhesion and uniformity. |
Equipment Design | Optimized chamber geometry and gas delivery systems improve control and efficiency. |
Process Control | Precise parameter control ensures consistent deposition rates and desired film properties. |
Optimize your deposition process today—contact our experts for tailored solutions!