Sintering is a critical process in materials science, driven primarily by the reduction of surface energy as particles bond at elevated temperatures. This process can occur below the melting point through solid-state sintering or involve the formation of a liquid phase. The driving force behind sintering is the minimization of surface energy, which is achieved by reducing the vapor-solid interfaces of the particles. Key factors influencing sintering include temperature, heating rate, pressure, particle size, and composition. These factors collectively determine the kinetics, densification, and final properties of the sintered material. Additionally, the sintering atmosphere, cooling rate, and process parameters such as layer thickness and machine speed play significant roles in optimizing the sintering process for desired material properties.
Key Points Explained:
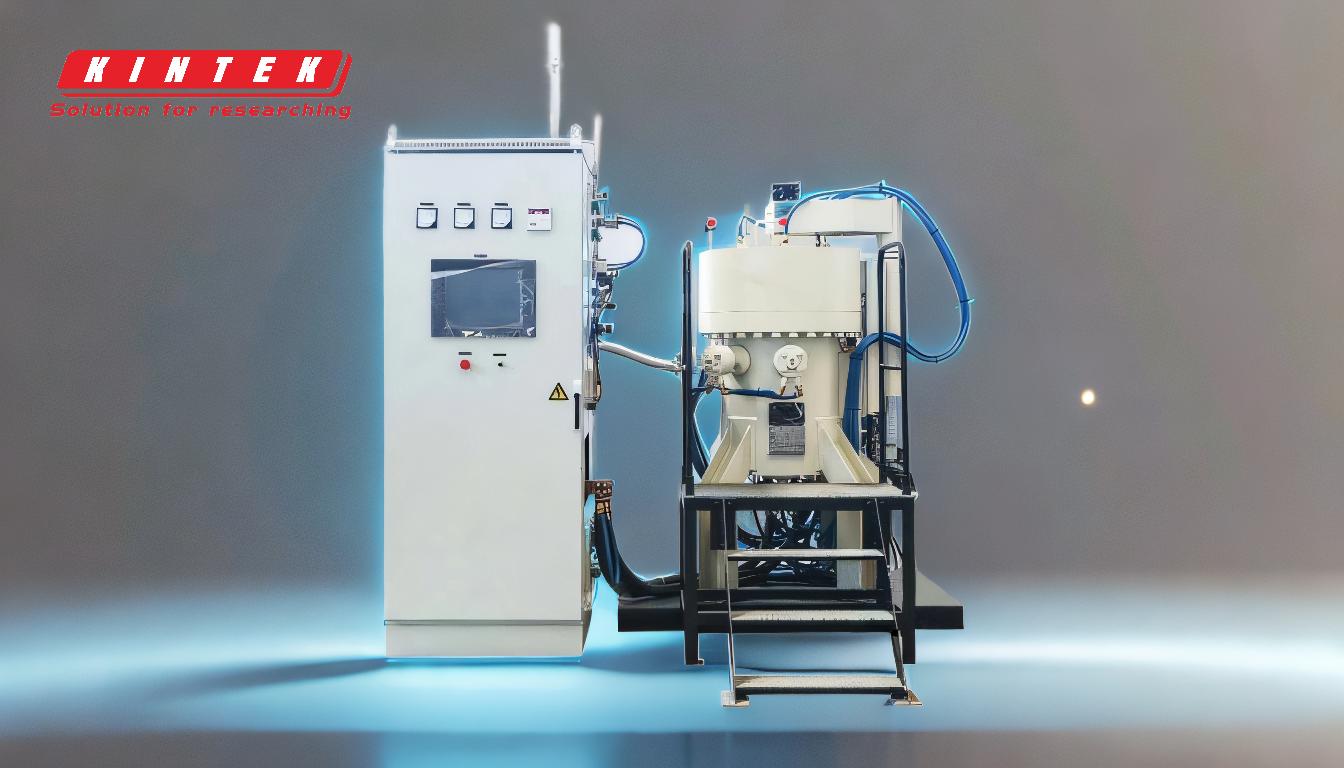
-
Driving Force of Sintering:
- The primary driving force behind sintering is the reduction of surface energy. As particles bond at high temperatures, the total surface area decreases, leading to a reduction in surface energy. This is achieved by minimizing the vapor-solid interfaces of the particles.
- Sintering can occur below the melting point (typically 0.7–0.8 of the melting temperature) through solid-state sintering, where atoms diffuse across particle boundaries to form bonds. Alternatively, sintering can involve the formation of a liquid phase, which enhances particle bonding.
-
Key Factors Influencing Sintering:
- Temperature: Temperature is a critical factor that determines the kinetics of sintering and the final material properties. Higher temperatures generally increase the rate of diffusion, leading to faster densification and stronger bonds between particles.
- Heating Rate: The rate at which the material is heated affects the densification process. A controlled heating rate ensures uniform densification and minimizes defects such as cracks or warping.
- Pressure: Applied pressure during sintering enhances particle rearrangement and helps eliminate porosity, leading to a more dense and uniform final product.
- Particle Size: Smaller particles have a higher surface area-to-volume ratio, which promotes faster diffusion and better densification. Fine powders are often preferred for sintering due to their enhanced sintering behavior.
- Composition: The chemical composition of the material affects its sintering behavior. Homogeneous compositions with well-distributed particles tend to sinter more uniformly and produce materials with better mechanical properties.
-
Sintering Atmosphere and Cooling Rate:
- The atmosphere in which sintering occurs (e.g., air, vacuum, or inert gases like argon/nitrogen) can significantly influence the process. For example, a vacuum or inert atmosphere prevents oxidation and allows for better control of the sintering environment.
- The cooling rate after sintering affects the microstructure and final properties of the material. Rapid cooling can lead to a finer grain structure, while slower cooling may result in larger grains and different mechanical properties.
-
Process Parameters:
- Layer Thickness and Machine Speed: In industrial sintering processes, the thickness of the material layer and the speed of the sintering machine are carefully controlled. Typical layer thicknesses range from 250-500mm, and machine speeds are maintained at 1.5-4m/min to ensure the material is sintered uniformly and reaches the desired endpoint.
- Air Volume and Vacuum: The air volume and vacuum conditions are critical for controlling the sintering environment. The air volume is typically around 3200m³ per ton of sintering ore, and the vacuum is determined by factors such as fan capacity, air resistance, and wind leakage loss.
-
Sintering Techniques:
- Different sintering techniques are employed depending on the specific requirements of the material and the desired properties. These techniques may involve the use of electrical currents, pressure, or various heat sources. The choice of technique is influenced by factors such as the material being sintered, the required density, and the final application of the product.
-
Thermally Activated Solid-State Diffusion:
- Sintering is fundamentally controlled by thermally activated solid-state diffusion mechanisms. These mechanisms can be quantified using sintering models and tools like Linseis push rod dilatometers, which measure the dimensional changes of materials during sintering.
-
Optimization of Sintering Process:
- The optimal sintering process is influenced by parameters such as sintering temperature, applied pressure, average grain size, and gaseous atmosphere. Finer powders and higher temperatures generally increase compaction, but the amount of liquid phase must be carefully controlled to avoid defects. The choice of process parameters depends on the expected product properties and the limiting factors of the sintering process.
In summary, sintering is a complex process driven by the reduction of surface energy and influenced by a multitude of factors including temperature, pressure, particle size, and sintering atmosphere. Understanding and controlling these factors is essential for optimizing the sintering process to achieve the desired material properties and performance.
Summary Table:
Aspect | Details |
---|---|
Driving Force | Reduction of surface energy through particle bonding at elevated temperatures. |
Key Factors | Temperature, heating rate, pressure, particle size, and composition. |
Sintering Atmosphere | Air, vacuum, or inert gases (e.g., argon/nitrogen). |
Process Parameters | Layer thickness (250-500mm), machine speed (1.5-4m/min), air volume (3200m³/ton). |
Optimization | Controlled temperature, pressure, grain size, and gaseous atmosphere. |
Optimize your sintering process for better material performance—contact our experts today!