Pressure plays a critical role in the sintering process, particularly in enhancing material density, reducing porosity, and improving mechanical properties. By applying pressure, especially in the later stages of sintering, plastic deformation is promoted, which helps in merging and eliminating pores. This results in materials that are closer to their theoretical density, with strengthened grain boundaries and controlled grain growth. The use of pressure, often combined with high temperatures in specialized equipment like a sintering furnace, ensures optimal densification and structural integrity of the final product.
Key Points Explained:
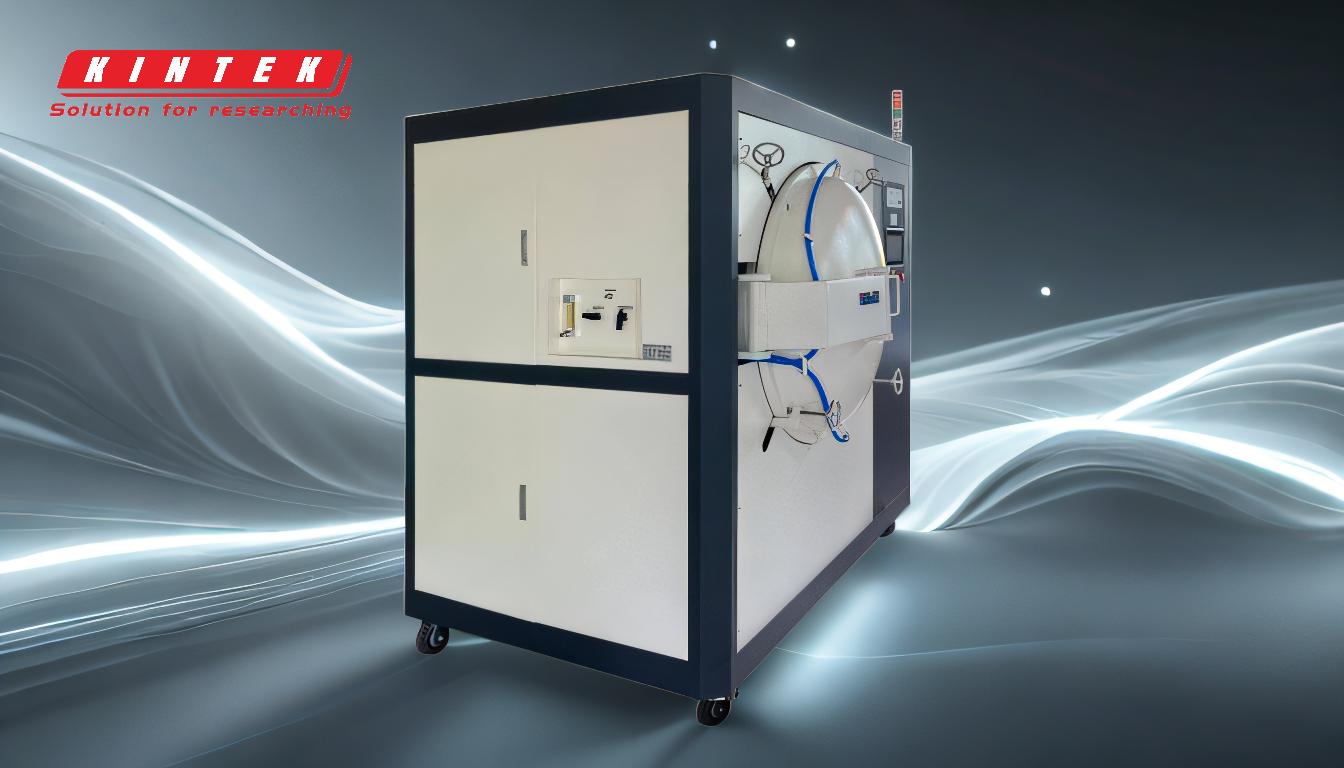
-
Enhancement of Plastic Deformation:
- Pressure, particularly oscillating pressure, facilitates plastic deformation during sintering. This deformation helps in the merging of smaller pores and their eventual elimination from the material.
- The process is crucial in achieving high-density materials, as it ensures that the residual pores are completely removed, bringing the material closer to its theoretical density.
-
Pore Elimination and Densification:
- The application of pressure aids in the discharge of pores, which is essential for achieving a dense and uniform microstructure.
- This densification process is vital for improving the mechanical properties of the sintered material, such as strength, hardness, and wear resistance.
-
Inhibition of Grain Growth:
- While high temperatures promote grain growth, the application of pressure can help control and inhibit excessive grain growth.
- Controlled grain growth is important for maintaining the desired mechanical properties and preventing the material from becoming too brittle.
-
Strengthening of Grain Boundaries:
- Pressure during sintering not only affects the grains but also strengthens the boundaries between them.
- Stronger grain boundaries contribute to the overall toughness and durability of the material, making it more resistant to cracking and deformation under stress.
-
Role of Sintering Furnaces:
- Sintering furnaces are essential in applying the necessary pressure and temperature conditions required for effective sintering.
- These furnaces, especially hot press sintering furnaces, combine high temperature and high pressure in a controlled environment to achieve optimal densification and material properties.
-
Combination of Pressure and Temperature:
- The synergy between pressure and temperature is critical in the sintering process. High temperatures promote particle bonding and diffusion, while pressure ensures the elimination of pores and densification.
- This combination is particularly effective in processes like hot press sintering, where ceramic powders are heated and fused under high pressure in a vacuum environment.
-
Atmosphere Control:
- The sintering atmosphere, regulated by various gases, plays a supporting role in the sintering process. It helps in controlling reactions such as deoxidization and decarburization, which can influence the final properties of the material.
- Proper atmosphere control ensures the stability and quality of the sintered product, especially in specialized applications like dental restorations.
In summary, pressure is a fundamental factor in sintering that significantly impacts the material's density, porosity, and mechanical properties. When combined with high temperatures and controlled atmospheres in a sintering furnace, it leads to the production of high-quality, dense, and durable materials.
Summary Table:
Effect of Pressure on Sintering | Key Benefits |
---|---|
Enhances Plastic Deformation | Merges and eliminates pores, achieving high-density materials. |
Promotes Pore Elimination | Improves densification and mechanical properties like strength and hardness. |
Inhibits Excessive Grain Growth | Maintains desired mechanical properties, preventing brittleness. |
Strengthens Grain Boundaries | Increases toughness and resistance to cracking. |
Synergy with Temperature | Ensures optimal densification and structural integrity. |
Controlled Atmosphere | Supports stability and quality of sintered products. |
Ready to optimize your sintering process? Contact our experts today for tailored solutions!