To produce biochar, specific equipment is required depending on the chosen production method, such as slow pyrolysis, fast pyrolysis, or gasification. These methods differ in terms of temperature, heating rates, biomass types, and vapor residence times. The equipment needed typically includes a reactor or kiln for thermal decomposition, a heating system to achieve the required temperatures, and systems for controlling airflow and managing by-products like syngas or bio-oil. Additional tools may include feedstock preparation equipment, cooling systems, and collection units for biochar and other outputs.
Key Points Explained:
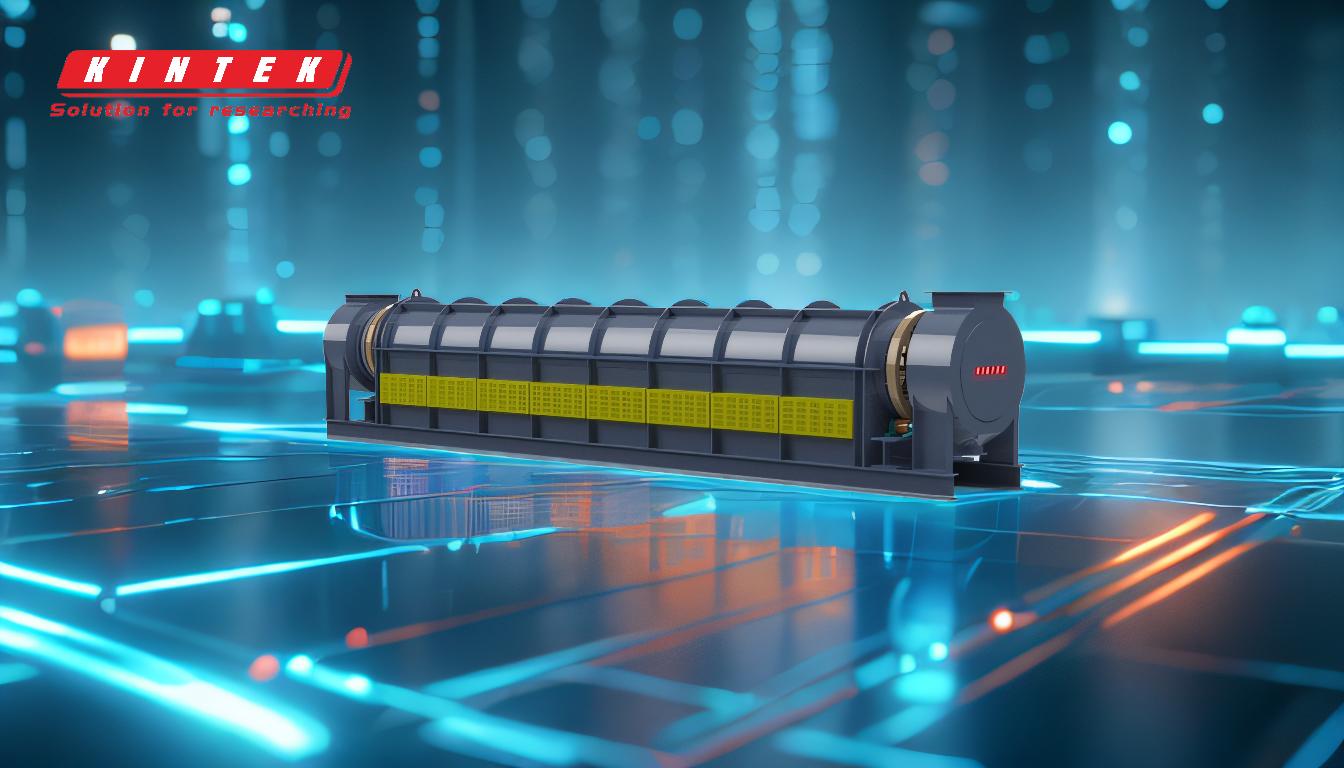
-
Reactor or Kiln:
- The core equipment for biochar production is a reactor or kiln, where the biomass undergoes thermal decomposition. This can be a simple retort kiln for small-scale production or a more sophisticated reactor for industrial-scale operations. The reactor must withstand high temperatures and provide controlled environments for pyrolysis or gasification.
-
Heating System:
- A heating system is essential to achieve the temperatures required for pyrolysis or gasification. This could involve electric heaters, gas burners, or even solar energy systems. The heating system must be capable of maintaining precise temperature ranges, typically between 300°C to 700°C, depending on the process.
-
Feedstock Preparation Equipment:
- Biomass feedstock needs to be prepared before it can be processed. This may involve chipping, shredding, or drying the biomass to ensure uniform particle size and moisture content. Equipment like chippers, shredders, and dryers are commonly used for this purpose.
-
Airflow Control Systems:
- Proper airflow is crucial for controlling the pyrolysis or gasification process. Equipment such as blowers, fans, and dampers are used to regulate the oxygen supply, which affects the quality and yield of biochar. Limited oxygen conditions are typically maintained to prevent complete combustion.
-
Cooling Systems:
- After the thermal decomposition process, the biochar needs to be cooled down before collection. Cooling systems, such as water-cooled condensers or air-cooled systems, are used to reduce the temperature of the biochar and prevent spontaneous combustion.
-
Collection Units:
- Biochar and other by-products like syngas or bio-oil need to be collected and separated. Cyclones, filters, and condensers are often used to capture these outputs. The biochar is then stored in containers or bags for further use or processing.
-
Monitoring and Control Systems:
- Advanced biochar production setups may include monitoring and control systems to ensure optimal process conditions. These systems can include temperature sensors, flow meters, and automated controls to adjust parameters in real-time.
By understanding these key components, one can assemble the necessary equipment to produce biochar efficiently, whether for small-scale or industrial applications. Each piece of equipment plays a vital role in ensuring the quality and consistency of the final biochar product.
Summary Table:
Equipment | Purpose |
---|---|
Reactor or Kiln | Core unit for thermal decomposition of biomass. |
Heating System | Achieves and maintains precise temperatures (300°C–700°C). |
Feedstock Preparation Tools | Prepares biomass (chipping, shredding, drying) for uniform processing. |
Airflow Control Systems | Regulates oxygen supply to optimize biochar quality and yield. |
Cooling Systems | Cools biochar post-production to prevent combustion. |
Collection Units | Captures biochar, syngas, and bio-oil for storage or further processing. |
Monitoring & Control Systems | Ensures optimal process conditions with real-time adjustments. |
Ready to start producing biochar? Contact our experts today for tailored solutions and equipment recommendations!