The sintering process involves transforming powdery materials into dense, solid bodies through the application of heat and pressure below the material's melting point. This process is widely used in industries such as ceramics, metals, and plastics manufacturing. The equipment used in sintering includes systems for ingredient preparation, mixing, ignition, and temperature control. Key components like the igniter play a critical role in burning the mixture, while other equipment ensures proper temperature, pressure, and structural integrity during the process. The sintering process is divided into stages to enhance bonding and reduce porosity, resulting in stronger and more durable materials.
Key Points Explained:
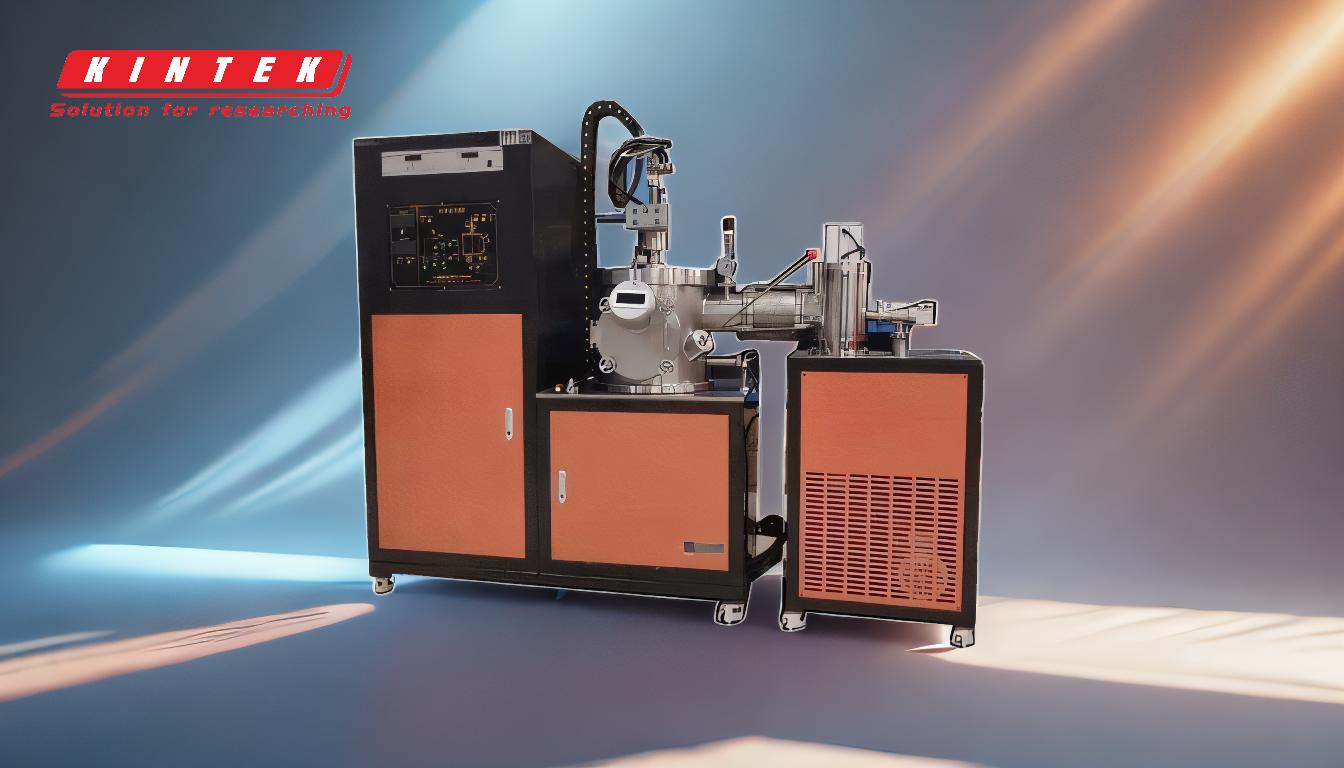
-
Definition and Purpose of Sintering
- Sintering is a manufacturing process that transforms powdery materials into dense, solid bodies by applying heat and pressure below the material's melting point.
- The process avoids liquefaction, allowing atoms to diffuse across particle boundaries and fuse together, reducing porosity and increasing structural integrity.
- It is commonly used in industries such as ceramics, metals, and plastics, as well as in powder metallurgy and pottery production.
-
Key Equipment Used in Sintering
- Igniter: A critical component that burns the mixture on the sintering machine, initiating the bonding process.
- Sintering Furnace: Provides controlled heat and pressure to facilitate the diffusion of atoms and fusion of particles.
- Ingredient Preparation System: Prepares raw materials, ensuring the correct composition and consistency of the powder mixture.
- Mixing System: Blends the ingredients uniformly to achieve a homogeneous mixture before sintering.
- Temperature and Pressure Control Systems: Regulate the sintering environment to maintain optimal conditions for bonding and densification.
-
Stages of the Sintering Process
- Preparation: Raw materials are prepared and mixed to ensure uniformity.
- Compaction: The mixture is pressed into a desired shape, creating a green body with sufficient structural integrity.
- Heating: The green body is heated in a furnace at temperatures below the material's melting point, allowing atoms to diffuse and bond.
- Cooling: The sintered product is cooled gradually to prevent cracking and ensure stability.
-
Parameters Controlled During Sintering
- Temperature: Must be carefully controlled to avoid melting while promoting atomic diffusion.
- Pressure: Applied to compact the material and reduce porosity.
- Negative Pressure: Used in some systems to enhance the sintering process by removing gases and improving bonding.
- Time: The duration of heating and cooling stages affects the final properties of the sintered product.
-
Applications of Sintering
- Ceramics: Used to produce pottery, tiles, and advanced ceramic components.
- Metals: Commonly applied in powder metallurgy to create metal parts with high strength and durability.
- Plastics: Sintered plastics are used in specialized applications requiring lightweight and robust materials.
-
Advantages of Sintering
- Produces materials with high strength, durability, and reduced porosity.
- Enables the creation of complex shapes and precise components.
- Reduces material waste compared to traditional manufacturing methods.
- Suitable for a wide range of materials, including ceramics, metals, and plastics.
-
Challenges in Sintering
- Requires precise control of temperature, pressure, and time to achieve desired properties.
- High initial investment in equipment and setup.
- Potential for defects such as cracking or warping if parameters are not optimized.
By understanding the equipment and processes involved in sintering, manufacturers can optimize their operations to produce high-quality materials for various industrial applications.
Summary Table:
Aspect | Details |
---|---|
Definition | Transforms powdery materials into dense, solid bodies using heat and pressure. |
Key Equipment | Igniter, sintering furnace, ingredient prep, mixing, temperature control. |
Stages | Preparation, compaction, heating, cooling. |
Applications | Ceramics, metals, plastics, powder metallurgy. |
Advantages | High strength, reduced porosity, complex shapes, material efficiency. |
Challenges | Precise control, high investment, risk of defects. |
Ready to optimize your sintering process? Contact our experts today for tailored solutions!