When hot metal is compressed, several physical and metallurgical changes occur due to the combination of heat and pressure. These changes include alterations in the metal's microstructure, such as grain refinement, and changes in its mechanical properties, like increased strength and hardness. The process can also lead to the elimination of internal defects and porosity, resulting in a more homogeneous and dense material. The specific outcomes depend on factors such as the type of metal, the temperature, the rate of compression, and the applied pressure. Understanding these changes is crucial for applications in metalworking, manufacturing, and materials science.
Key Points Explained:
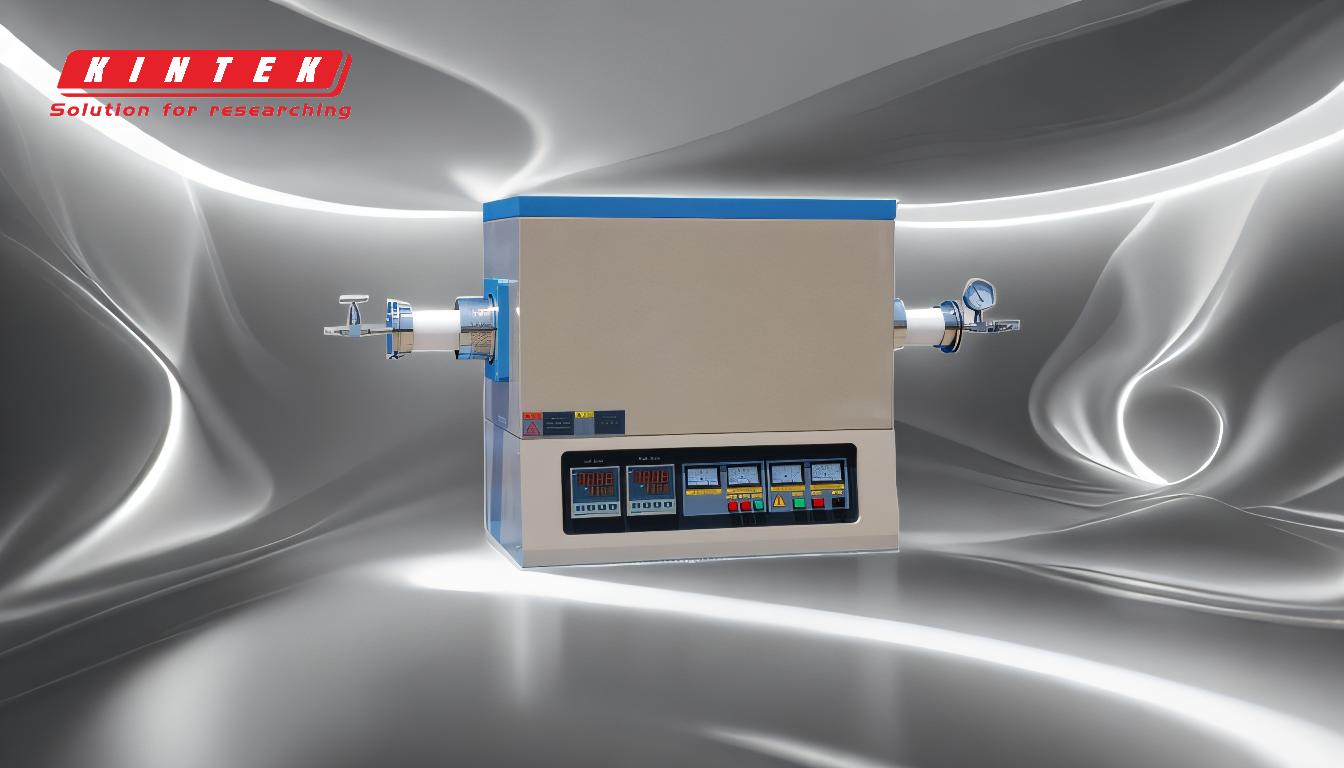
-
Microstructural Changes:
- Grain Refinement: When hot metal is compressed, the grains within the metal structure are deformed and may break down into smaller grains. This process, known as grain refinement, improves the metal's mechanical properties, such as strength and toughness.
- Recrystallization: At high temperatures, the metal may undergo recrystallization, where new, strain-free grains form, replacing the deformed grains. This process can further enhance the metal's properties by reducing internal stresses and improving ductility.
-
Mechanical Properties:
- Increased Strength: Compression at high temperatures can lead to work hardening, where the metal becomes stronger due to the dislocation of atoms within the crystal structure. This is particularly beneficial in applications requiring high strength and durability.
- Improved Hardness: The process of compressing hot metal can also increase its hardness, making it more resistant to wear and deformation.
-
Elimination of Defects:
- Porosity Reduction: Compression helps to close up internal voids and pores within the metal, leading to a denser and more uniform material. This is especially important in casting processes where porosity can weaken the metal.
- Stress Relief: The application of pressure at high temperatures can help to relieve internal stresses that may have been introduced during previous manufacturing processes, such as welding or casting.
-
Thermal Effects:
- Temperature Control: The temperature at which the metal is compressed plays a critical role in determining the outcomes. If the temperature is too low, the metal may not deform properly, leading to cracks or fractures. If the temperature is too high, the metal may become too soft, reducing its strength.
- Cooling Rate: The rate at which the metal cools after compression can also affect its final properties. Rapid cooling may lead to the formation of undesirable phases, while slow cooling can allow for the development of a more stable microstructure.
-
Applications in Industry:
- Forging: In forging processes, hot metal is compressed to shape it into desired forms. The combination of heat and pressure allows for the creation of complex shapes with improved mechanical properties.
- Hot Rolling: In hot rolling, metal is passed through rollers at high temperatures to reduce its thickness and improve its surface finish. The compression during rolling enhances the metal's strength and uniformity.
- Extrusion: In extrusion processes, hot metal is forced through a die to create long, continuous shapes. The compression involved in extrusion helps to refine the metal's microstructure and improve its mechanical properties.
Understanding the effects of compressing hot metal is essential for optimizing manufacturing processes and ensuring the production of high-quality metal products. By controlling factors such as temperature, pressure, and cooling rate, manufacturers can tailor the properties of the metal to meet specific application requirements.
Summary Table:
Aspect | Effects of Compressing Hot Metal |
---|---|
Microstructure | Grain refinement and recrystallization improve strength and ductility. |
Mechanical Properties | Increased strength and hardness due to work hardening. |
Defect Elimination | Porosity reduction and stress relief create a denser, more uniform material. |
Thermal Effects | Temperature control and cooling rate influence final properties. |
Industrial Applications | Forging, hot rolling, and extrusion benefit from enhanced metal properties. |
Want to optimize your metalworking processes? Contact our experts today for tailored solutions!