Heat treatment is a critical process for large castings, especially when specific mechanical or physical properties are required for their intended application. The process involves heating the casting to a specified temperature, holding it at that temperature for a predetermined time, and then cooling it using prescribed methods. The goal is to enhance properties such as hardness, strength, and wear resistance. While not all castings require heat treatment, it is essential for applications demanding superior performance characteristics. The specific heat treatment process depends on the material, the desired properties, and the application requirements.
Key Points Explained:
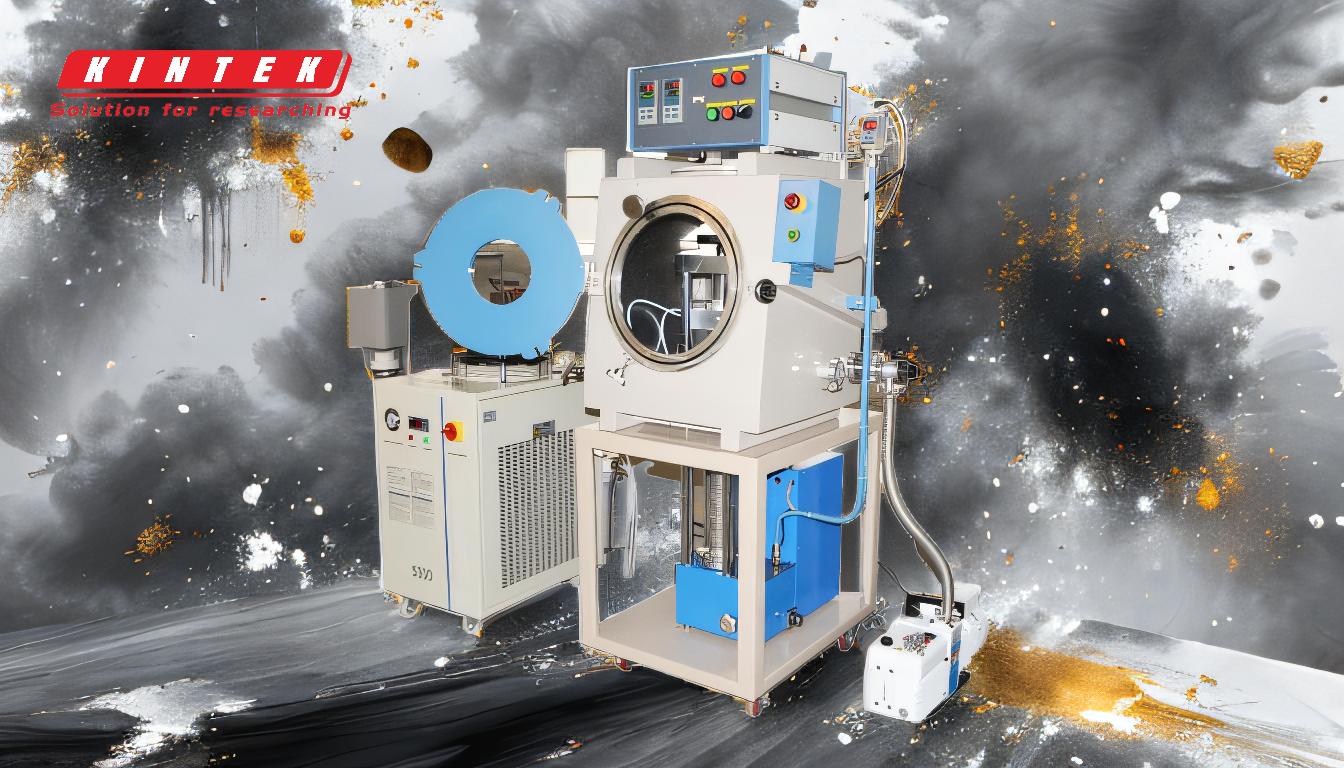
-
Purpose of Heat Treatment for Large Castings
- Heat treatment is used to improve the mechanical and physical properties of large castings, such as hardness, strength, ductility, and resistance to wear and corrosion.
- It is particularly important for castings used in demanding applications, such as heavy machinery, aerospace, or automotive components, where performance under stress is critical.
- Heat treatment can also relieve internal stresses caused during the casting process, reducing the risk of cracking or deformation.
-
Basic Steps of Heat Treatment
- Heating: The casting is heated to a specific temperature, which can range up to 2,400°F (1,315°C), depending on the material and desired outcome.
- Holding: The casting is held at the target temperature for a set period, which can vary from a few seconds to over 60 hours. This duration ensures uniform heat distribution and allows for microstructural changes.
- Cooling: The casting is cooled according to a controlled method, such as air cooling, oil quenching, or water quenching. The cooling rate significantly impacts the final properties of the material.
-
Types of Heat Treatment Processes for Large Castings
- Annealing: This process involves heating the casting to a high temperature and then slowly cooling it. It softens the material, improves ductility, and reduces internal stresses.
- Normalizing: Similar to annealing, but the cooling process is faster. It refines the grain structure and improves mechanical properties.
- Quenching: The casting is rapidly cooled to achieve high hardness and strength. However, this can introduce internal stresses, which may require tempering.
- Tempering: After quenching, the casting is reheated to a lower temperature to reduce brittleness and improve toughness.
- Stress Relieving: This process involves heating the casting to a moderate temperature and then slowly cooling it to relieve residual stresses without significantly altering the microstructure.
-
Factors Influencing Heat Treatment
- Material Composition: Different materials (e.g., steel, cast iron, aluminum) require specific heat treatment processes to achieve the desired properties.
- Casting Size and Geometry: Large castings may require specialized equipment and longer heating/cooling times to ensure uniform treatment.
- Application Requirements: The intended use of the casting determines the necessary properties, such as hardness, strength, or wear resistance.
- Cooling Rate: The method and rate of cooling (e.g., air, oil, water) directly affect the final properties of the material.
-
Challenges in Heat Treating Large Castings
- Uniform Heating: Ensuring even heat distribution throughout a large casting can be challenging, requiring precise control of furnace conditions.
- Distortion and Cracking: Rapid cooling or uneven heating can lead to warping or cracking, especially in complex geometries.
- Energy and Time Requirements: Heat treating large castings is energy-intensive and time-consuming, often requiring specialized equipment and expertise.
-
When Heat Treatment is Not Required
- Some castings can be used "as cast" if their material properties already meet the application requirements.
- Heat treatment may not be necessary for non-critical components or those made from materials that inherently possess the desired properties.
-
Importance of Post-Treatment Inspection
- After heat treatment, large castings should be inspected for dimensional accuracy, surface quality, and mechanical properties.
- Non-destructive testing methods, such as ultrasonic or magnetic particle inspection, can detect internal defects or inconsistencies.
By carefully selecting and applying the appropriate heat treatment process, manufacturers can ensure that large castings meet the stringent requirements of their intended applications, enhancing performance, durability, and reliability.
Summary Table:
Aspect | Details |
---|---|
Purpose | Improves hardness, strength, ductility, and wear/corrosion resistance. |
Basic Steps | Heating, holding at temperature, controlled cooling. |
Types of Processes | Annealing, normalizing, quenching, tempering, stress relieving. |
Key Factors | Material, size/geometry, application needs, cooling rate. |
Challenges | Uniform heating, distortion/cracking, energy/time requirements. |
Post-Treatment | Inspection for accuracy, surface quality, and mechanical properties. |
Optimize your large castings with expert heat treatment solutions—contact us today!