Heat treatment processes are essential for modifying the properties of materials, such as softening them or achieving desired mechanical characteristics like hardness, ductility, and toughness. The most commonly used heat treatment processes for softening materials and obtaining other properties include annealing, tempering, and normalizing. Annealing is particularly effective for softening metals by reducing hardness and increasing ductility, while tempering improves toughness and reduces brittleness. Other processes like case hardening, carburizing, and quenching are used to enhance surface hardness and wear resistance. Each process involves specific temperature controls, cooling rates, and atmospheres to achieve the desired material properties.
Key Points Explained:
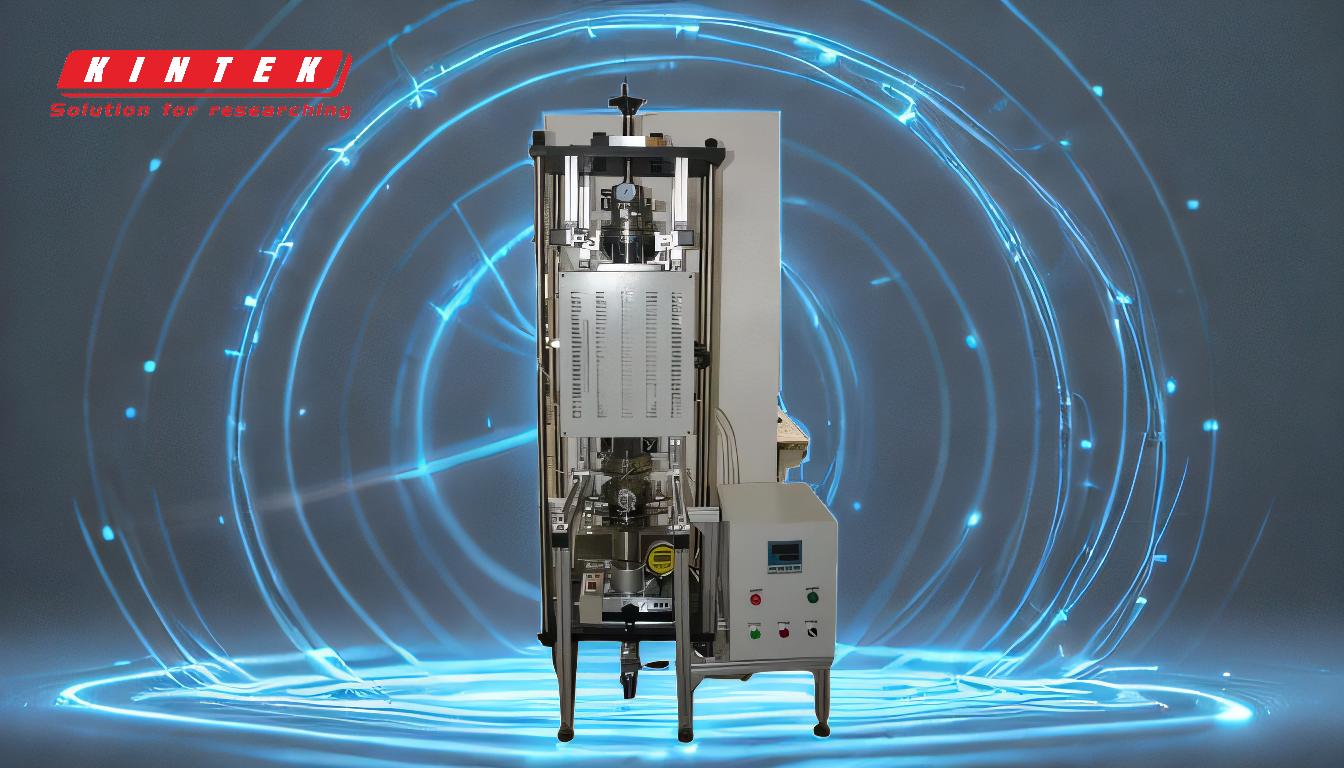
-
Annealing:
- Purpose: Annealing is primarily used to soften materials, reduce internal stresses, and improve ductility.
- Process: The material is heated to a specific temperature (above its recrystallization temperature but below its melting point) and then slowly cooled in a furnace or air.
- Applications: Commonly used for metals like steel, copper, and aluminum to make them more workable for subsequent manufacturing processes.
- Benefits: Improves machinability, reduces hardness, and enhances grain structure uniformity.
-
Tempering:
- Purpose: Tempering is used to reduce brittleness and increase toughness in hardened materials.
- Process: After quenching, the material is reheated to a temperature below its critical point and then cooled at a controlled rate.
- Applications: Often applied to steel after quenching to balance hardness and toughness.
- Benefits: Enhances ductility and impact resistance while maintaining adequate hardness.
-
Normalizing:
- Purpose: Normalizing refines the grain structure and improves mechanical properties like strength and toughness.
- Process: The material is heated to a temperature above its critical range and then cooled in air.
- Applications: Used for steel to achieve a more uniform microstructure and better machinability.
- Benefits: Provides a balance between hardness and ductility, making the material more suitable for machining and forming.
-
Case Hardening:
- Purpose: Case hardening increases surface hardness while maintaining a tough core.
- Process: Techniques like carburizing or nitriding introduce carbon or nitrogen into the surface layer of the material, followed by quenching.
- Applications: Commonly used for gears, shafts, and other components requiring wear resistance.
- Benefits: Enhances surface durability without compromising the core's toughness.
-
Carburizing:
- Purpose: Carburizing increases surface hardness by adding carbon to the outer layer of the material.
- Process: The material is heated in a carbon-rich environment (e.g., endothermic gas) and then quenched.
- Applications: Ideal for low-carbon steels to improve wear resistance.
- Benefits: Creates a hard, wear-resistant surface while maintaining a ductile core.
-
Quenching:
- Purpose: Quenching rapidly cools the material to achieve high hardness and strength.
- Process: The material is heated to a high temperature and then immersed in a quenching medium (e.g., water, oil, or air).
- Applications: Used for steels and other alloys to achieve martensitic transformation.
- Benefits: Provides high hardness but may require tempering to reduce brittleness.
-
Precipitation Hardening:
- Purpose: Precipitation hardening increases strength by forming fine precipitates within the material.
- Process: The material is heated to dissolve alloying elements, then cooled and aged to allow precipitation.
- Applications: Commonly used for aluminum, nickel, and stainless steel alloys.
- Benefits: Enhances strength and hardness without significant loss of ductility.
-
Bright Annealing:
- Purpose: Bright annealing minimizes oxidation and maintains a clean, bright surface.
- Process: The material is heated in a protective atmosphere (e.g., hydrogen, nitrogen, or argon) and then cooled.
- Applications: Used for stainless steel and other alloys requiring a polished finish.
- Benefits: Prevents surface oxidation and preserves the material's appearance.
-
Stress Relieving:
- Purpose: Stress relieving reduces residual stresses caused by machining, welding, or forming.
- Process: The material is heated to a temperature below its critical range and then slowly cooled.
- Applications: Used for welded components and cold-worked metals.
- Benefits: Improves dimensional stability and reduces the risk of cracking.
By understanding these heat treatment processes, manufacturers can select the appropriate method to achieve the desired material properties for specific applications. Each process offers unique benefits, making them indispensable in industries ranging from automotive to aerospace.
Summary Table:
Process | Purpose | Applications | Benefits |
---|---|---|---|
Annealing | Soften materials, reduce internal stresses, improve ductility | Steel, copper, aluminum | Improves machinability, reduces hardness, enhances grain structure uniformity |
Tempering | Reduce brittleness, increase toughness | Steel after quenching | Enhances ductility and impact resistance |
Normalizing | Refine grain structure, improve strength and toughness | Steel | Balances hardness and ductility, improves machinability |
Case Hardening | Increase surface hardness while maintaining a tough core | Gears, shafts, wear-resistant components | Enhances surface durability without compromising core toughness |
Carburizing | Increase surface hardness by adding carbon | Low-carbon steels | Creates a hard, wear-resistant surface with a ductile core |
Quenching | Achieve high hardness and strength | Steels and alloys | Provides high hardness but may require tempering |
Precipitation Hardening | Increase strength by forming fine precipitates | Aluminum, nickel, stainless steel alloys | Enhances strength and hardness without significant loss of ductility |
Bright Annealing | Minimize oxidation, maintain a clean, bright surface | Stainless steel, polished alloys | Prevents surface oxidation, preserves appearance |
Stress Relieving | Reduce residual stresses from machining, welding, or forming | Welded components, cold-worked metals | Improves dimensional stability, reduces cracking risk |
Need help selecting the right heat treatment process for your materials? Contact our experts today for tailored solutions!