A batch type furnace for heat treatment is a specialized piece of equipment designed to heat materials in a controlled environment to achieve specific metallurgical properties. Unlike continuous furnaces, batch furnaces process materials in discrete batches, making them ideal for applications requiring precise control over temperature, atmosphere, and cooling rates. These furnaces are widely used in industries such as aerospace, automotive, and manufacturing for processes like annealing, hardening, tempering, and sintering. The design and features of a batch furnace vary depending on the material being treated and the desired outcome, but they typically include advanced heating elements, temperature controllers, and cooling systems to ensure consistent and high-quality results.
Key Points Explained:
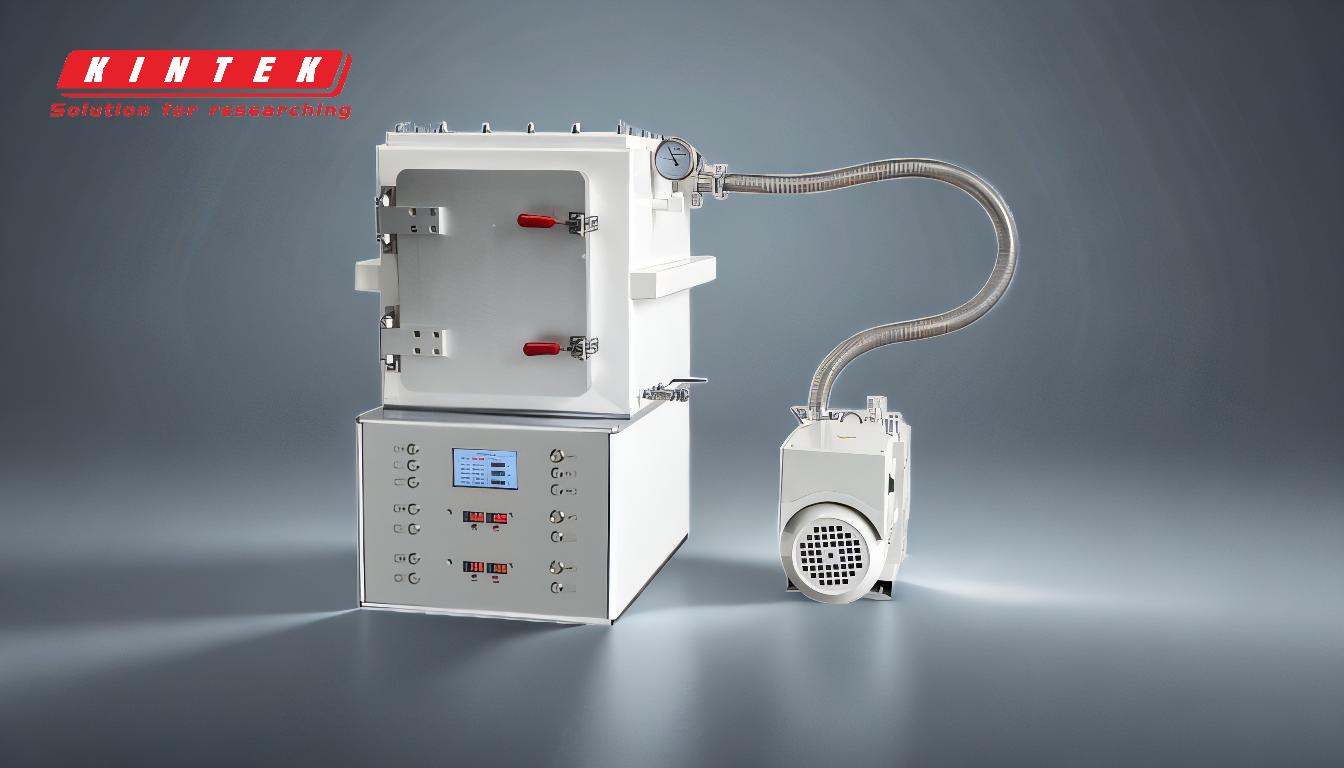
-
Definition and Purpose of a Batch Type Furnace:
- A batch type furnace is designed to heat treat materials in discrete batches rather than continuously. This allows for precise control over the heating and cooling processes, which is critical for achieving specific material properties.
- It is commonly used for processes such as annealing, hardening, tempering, and sintering, where consistent and controlled conditions are essential.
-
Key Features of Batch Type Furnaces:
- Temperature Control: Advanced controllers ensure accurate temperature adjustment, which is crucial for achieving the desired material properties.
- Heating Elements: High-quality heating elements provide even heat distribution, ensuring uniform treatment of the materials.
- Cooling Systems: Efficient cooling systems are integrated to manage the cooling rates, which can significantly impact the final properties of the treated materials.
- Atmosphere Control: Many batch furnaces allow for controlled atmospheres, such as vacuum or inert gas, to prevent oxidation or other undesirable reactions during heat treatment.
-
Applications in Heat Treatment:
- Annealing: Used to soften materials, improve machinability, and relieve internal stresses.
- Hardening: Increases the hardness and strength of materials through rapid cooling.
- Tempering: Reduces brittleness and improves toughness after hardening.
- Sintering: A process used to bond powdered materials into a solid mass, often used in the production of ceramics and metals. For more details on sintering, see sintering furnace.
-
Design Considerations:
- Material Compatibility: The design of the furnace must be compatible with the materials being treated, including considerations for temperature range and atmosphere.
- Structural Integrity: High structural design and manufacturing accuracy are required, especially for furnaces operating at high temperatures and pressures.
- Cooling Efficiency: Effective cooling systems are essential to manage the thermal stress on the furnace components and ensure consistent performance.
-
Advantages of Batch Type Furnaces:
- Flexibility: Batch furnaces can be easily adapted to different materials and processes, making them versatile tools in heat treatment.
- Precision: The ability to control every aspect of the heat treatment process ensures high-quality results.
- Efficiency: Batch processing allows for optimal use of energy and resources, as each batch can be tailored to specific requirements.
-
Comparison with Continuous Furnaces:
- Batch vs. Continuous: While continuous furnaces are suitable for high-volume production, batch furnaces offer greater flexibility and precision, making them ideal for specialized or low-volume applications.
- Process Control: Batch furnaces provide better control over the entire heat treatment cycle, from heating to cooling, which is crucial for achieving specific material properties.
In summary, a batch type furnace for heat treatment is a versatile and precise tool used in various industrial applications to achieve specific material properties. Its design and features are tailored to provide optimal control over the heat treatment process, ensuring high-quality and consistent results. For more information on sintering processes, refer to sintering furnace.
Summary Table:
Feature | Description |
---|---|
Temperature Control | Advanced controllers ensure accurate temperature adjustment for desired results. |
Heating Elements | High-quality elements provide uniform heat distribution for consistent treatment. |
Cooling Systems | Efficient cooling manages rates, impacting final material properties. |
Atmosphere Control | Controlled environments (e.g., vacuum or inert gas) prevent oxidation. |
Applications | Annealing, hardening, tempering, and sintering for various industries. |
Advantages | Flexibility, precision, and efficiency in heat treatment processes. |
Ready to enhance your heat treatment process? Contact us today to learn more about batch type furnaces!