A burnout furnace in dentistry is primarily used for the removal of wax patterns and organic materials from dental molds before the casting process. This step is crucial in creating precise dental restorations such as crowns, bridges, and frameworks. The furnace ensures that all organic materials are completely eliminated, leaving behind a clean mold ready for metal or ceramic casting. Additionally, burnout furnaces are essential in the heat treatment of 3D-printed metal restorations, ensuring the final product meets the required strength and durability standards. The process is closely related to sintering, where a sintering furnace is used to fuse ceramic or metal particles into a solid structure, ensuring the restoration's density and stability.
Key Points Explained:
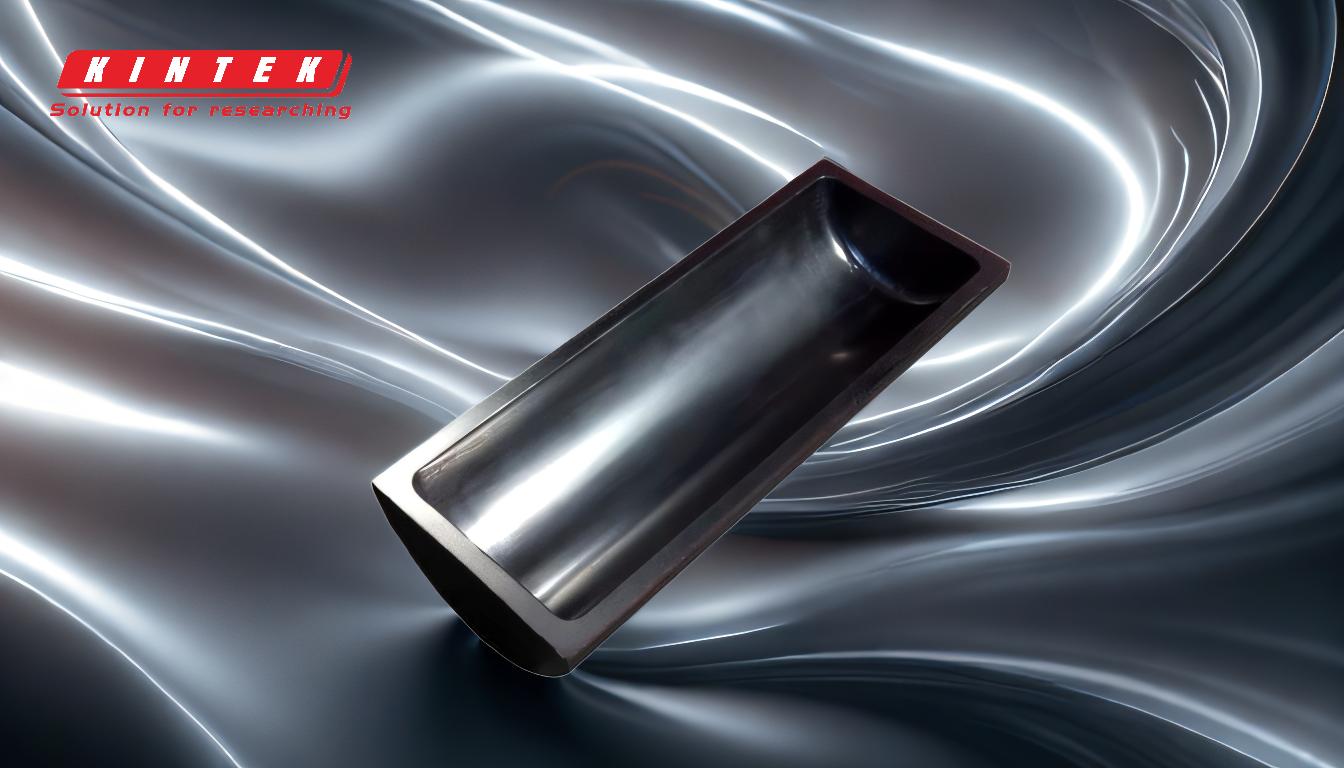
-
Purpose of a Burnout Furnace in Dentistry:
- A burnout furnace is specifically designed to remove wax and other organic materials from dental molds. This step is critical in the lost-wax casting technique, which is widely used in dental laboratories to create precise restorations.
- It ensures that the mold is free of any residues that could compromise the final restoration's accuracy and quality.
-
Role in Dental Restoration Processes:
- The burnout furnace is used in conjunction with other dental equipment, such as a sintering furnace, to produce high-quality dental restorations. After the burnout process, the mold is ready for casting, and the sintering furnace is used to fuse the material into a solid structure.
- This combination of processes ensures that the final restoration is durable, aesthetically pleasing, and meets the required functional standards.
-
Heat Treatment for 3D-Printed Restorations:
- Burnout furnaces are also used in the heat treatment of 3D-printed metal restorations. This step is essential to achieve the desired mechanical properties, such as strength and durability, in the final product.
- The furnace ensures that the restoration undergoes the necessary thermal cycles to eliminate any internal stresses and improve its overall performance.
-
Atmosphere Control and Process Stability:
- Modern burnout furnaces are equipped with advanced features such as atmosphere control, which ensures the stability and quality of the dental restorations. This is particularly important in preventing oxidation and other defects during the burnout process.
- The furnace's ability to maintain consistent temperature and atmosphere conditions is crucial for achieving predictable and high-quality results.
-
Integration with Sintering Processes:
- The burnout furnace works in tandem with a sintering furnace to complete the dental restoration process. After the burnout phase, the sintering furnace is used to fuse the ceramic or metal particles, ensuring the restoration's density and stability.
- This integration is essential for producing restorations that are both functional and aesthetically pleasing, meeting the high standards required in modern dentistry.
In summary, the burnout furnace plays a vital role in the dental restoration process by ensuring the complete removal of organic materials and preparing the mold for casting. Its integration with sintering processes and advanced features like atmosphere control make it an indispensable tool in modern dental laboratories.
Summary Table:
Key Functions | Details |
---|---|
Wax and Organic Material Removal | Eliminates wax and organic residues from dental molds for accurate casting. |
Heat Treatment for 3D-Printed Restorations | Ensures strength and durability in 3D-printed metal restorations. |
Atmosphere Control | Prevents oxidation and defects, ensuring high-quality results. |
Integration with Sintering | Works with sintering furnaces to fuse materials for stable restorations. |
Discover how a burnout furnace can elevate your dental lab's precision—contact us today!