A burnout kiln is a specialized type of kiln used primarily in the ceramics and metalworking industries to remove organic materials, such as binders or waxes, from molds or products before the final firing or sintering process. It operates at high temperatures to ensure complete combustion or decomposition of these materials, leaving behind a clean, residue-free structure. This process is critical for achieving high-quality finished products, as any remaining organic material can lead to defects during the final firing stage.
Key Points Explained:
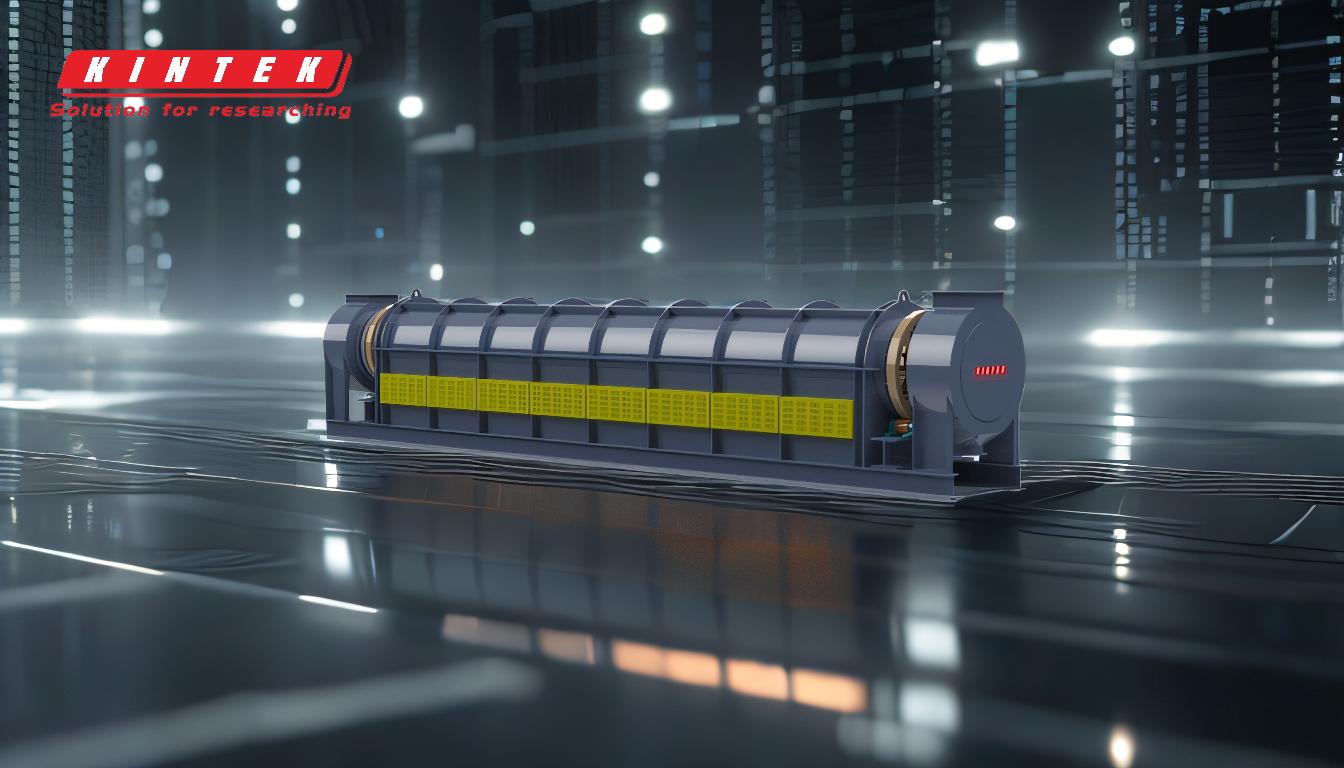
-
Purpose of a Burnout Kiln:
- A burnout kiln is designed to remove organic materials, such as waxes, binders, or other residues, from molds or ceramic/metal products. This process ensures that the final product is free from contaminants that could cause defects during the sintering or firing process.
- The burnout process is essential in industries like ceramics, jewelry making, and metal casting, where organic materials are used in the initial stages of production.
-
Temperature Range:
- Burnout kilns typically operate at high temperatures, often exceeding 1000°C (1832°F), to ensure complete combustion or decomposition of organic materials. The exact temperature depends on the type of material being removed and the requirements of the final product.
- For example, in ceramic production, burnout kilns may reach temperatures of up to 1288°C (2350°F), similar to sintering kilns, to ensure thorough removal of binders.
-
Design and Features:
- Burnout kilns are constructed from refractory materials that can withstand high temperatures without melting or degrading. This ensures durability and consistent performance over multiple cycles.
- Many burnout kilns feature advanced control systems, such as touchscreen interfaces, allowing users to program and monitor the burnout process with precision. Some models even offer remote monitoring via smartphones or computers.
- Customization options, such as air cooling mechanisms and 360° heater placement, ensure even heat distribution and stable temperature control, which are critical for achieving uniform burnout results.
-
Applications:
- Ceramics: Used to remove binders from ceramic molds before the final firing process.
- Metal Casting: Employed in lost-wax casting to eliminate wax patterns from investment molds.
- Jewelry Making: Ensures that wax models are completely burned out before casting precious metals.
-
Advantages of Modern Burnout Kilns:
- Efficiency: Modern burnout kilns are designed for energy efficiency, reducing operational costs and environmental impact.
- Precision: Advanced control systems allow for precise temperature management, ensuring consistent results.
- Versatility: Customizable features, such as adjustable heat patterns and contamination suppression mechanisms, make burnout kilns suitable for a wide range of applications.
-
Comparison with Other Kilns:
- Unlike sintering kilns, which focus on fusing particles to create a solid structure, burnout kilns are specifically designed for the removal of organic materials.
- Rotary kilns, which are used for material processing, differ in design and function, as they involve a rotating mechanism to ensure even heat distribution and are often used in industrial processes like cement production.
In summary, a burnout kiln is an essential tool in industries that require the removal of organic materials before the final production stage. Its high-temperature capabilities, advanced control systems, and customizable features make it a versatile and efficient solution for achieving high-quality finished products.
Summary Table:
Key Aspect | Details |
---|---|
Purpose | Removes organic materials like waxes and binders from molds/products. |
Temperature Range | Operates at 1000°C (1832°F) or higher, up to 1288°C (2350°F) for ceramics. |
Design & Features | Refractory materials, touchscreen controls, remote monitoring, air cooling. |
Applications | Ceramics, metal casting, jewelry making. |
Advantages | Energy-efficient, precise temperature control, versatile customization. |
Comparison with Kilns | Focuses on organic material removal, unlike sintering or rotary kilns. |
Discover how a burnout kiln can elevate your production quality—contact us today!