A calciner kiln is a specialized type of rotary kiln used primarily for the calcination process, which involves heating materials to high temperatures to induce chemical dissociation or remove bound moisture. It is widely used in industries such as cement production, metallurgy, and chemical processing. The calciner kiln operates by exposing materials to controlled high temperatures, ensuring the desired chemical reactions occur efficiently. Its design includes key components like the kiln shell, refractory lining, support tyres, and drive gear, which work together to facilitate material movement, heat transfer, and combustion. Customization options allow the kiln to meet specific industrial requirements, though this often increases costs.
Key Points Explained:
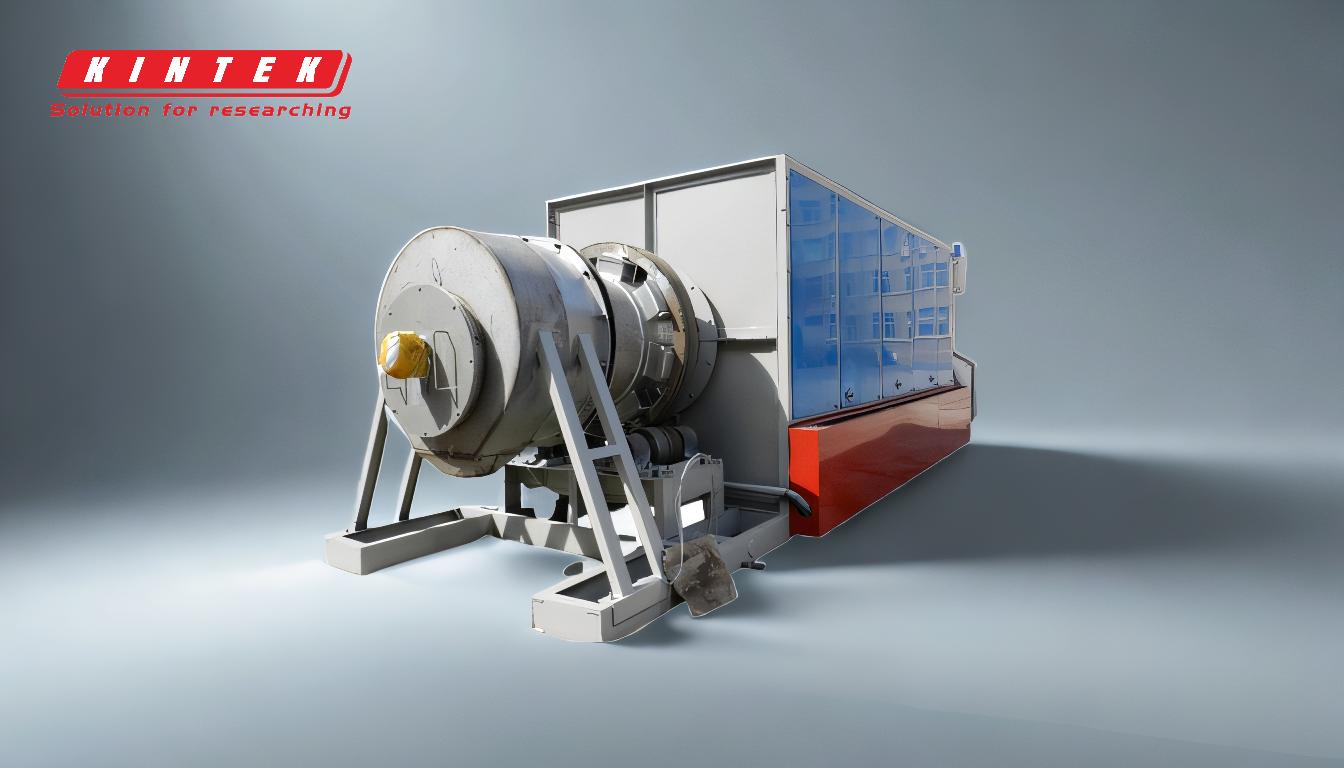
-
Definition and Purpose of a Calciner Kiln:
- A calciner kiln is a rotary kiln specifically designed for calcination, a thermal process that heats materials to high temperatures to achieve chemical dissociation or remove moisture.
- Common applications include the dissociation of calcium carbonate (CaCO₃) into calcium oxide (CaO) and carbon dioxide (CO₂) in cement production, as well as the removal of bound moisture from materials like borax.
-
Key Components of a Calciner Kiln:
- Kiln Shell: The outer structure that houses the internal components and withstands high temperatures.
- Refractory Lining: A heat-resistant lining inside the kiln shell that protects it from extreme temperatures and chemical reactions.
- Support Tyres (Riding Rings) and Rollers: These components support the kiln's weight and allow it to rotate smoothly.
- Drive Gear: Powers the rotation of the kiln, ensuring consistent material movement.
- Internal Heat Exchangers: Facilitate efficient heat transfer to the materials being processed.
-
Working Principle:
- The calciner kiln operates through a combination of gas flow, fuel combustion, heat transfer, and material movement.
- Fuel is burned to generate heat, which is transferred to the material inside the kiln.
- As the kiln rotates, the material moves through different temperature zones, undergoing physical and chemical changes to form the desired product.
-
Customization and Cost Considerations:
- Calciner kilns can be customized to meet specific industrial needs, such as processing unique materials or achieving particular temperature profiles.
- Customization often involves modifying components like the kiln shell, refractory lining, or heat exchangers, which can increase costs.
-
Applications in Industry:
- Cement Production: Calciner kilns are essential for producing clinker, a key ingredient in cement.
- Metallurgy: Used for roasting ores and removing impurities.
- Chemical Processing: Employed in the production of inorganic materials and the removal of moisture from chemical compounds.
-
Advantages of Using a Calciner Kiln:
- Efficient Heat Transfer: The design ensures optimal heat distribution, reducing energy consumption.
- Versatility: Can handle a wide range of materials and processes.
- Scalability: Suitable for both small-scale laboratory use and large-scale industrial production.
-
Comparison with Other Kiln Types:
- Unlike standard rotary kilns, calciner kilns are specifically optimized for high-temperature chemical reactions.
- They often include additional features like advanced heat exchangers or specialized refractory linings to enhance performance.
By understanding the design, components, and operational principles of a calciner kiln, industries can effectively utilize this equipment to achieve precise thermal processing and optimize production outcomes.
Summary Table:
Aspect | Details |
---|---|
Definition | A rotary kiln optimized for calcination, heating materials to induce chemical changes or remove moisture. |
Key Components | Kiln shell, refractory lining, support tyres, drive gear, internal heat exchangers. |
Working Principle | Combines gas flow, fuel combustion, heat transfer, and material movement for precise thermal processing. |
Applications | Cement production, metallurgy, chemical processing. |
Advantages | Efficient heat transfer, versatility, scalability. |
Customization | Tailored designs for specific industrial needs, though costs may increase. |
Discover how a calciner kiln can optimize your industrial processes—contact our experts today!