A ceramic furnace is a specialized heating device designed to achieve and maintain extremely high temperatures, typically used for processes such as firing, melting, or sintering ceramic materials. These furnaces are constructed with components that can withstand intense heat, ensuring precise temperature control and uniform heat distribution. Key components include a firing or heating chamber, heating elements, insulation, and an electronic control system. Ceramic furnaces are widely used in industries such as ceramics manufacturing, metallurgy, and laboratory research, where high-temperature processing is essential. They come in various designs, including muffle furnaces, tube furnaces, and crucible furnaces, each tailored to specific applications.
Key Points Explained:
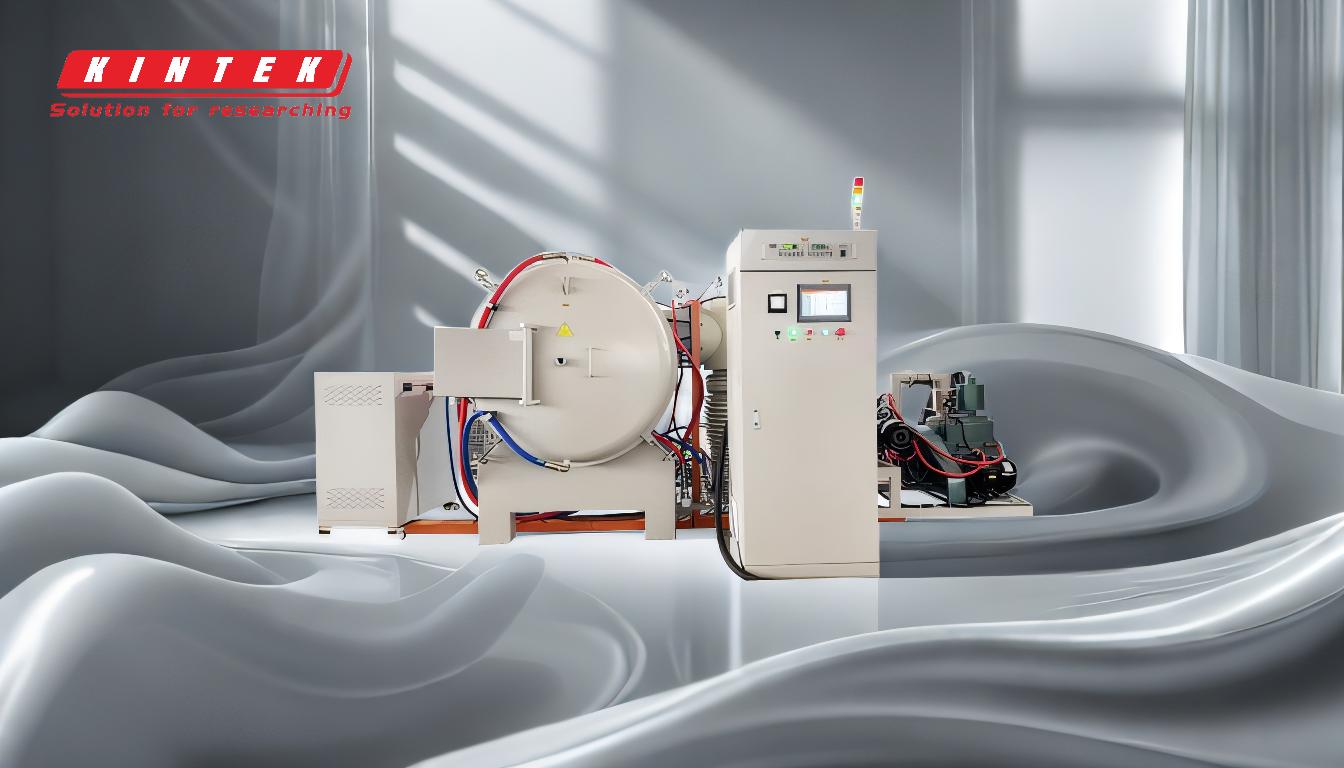
-
Definition and Purpose of a Ceramic Furnace:
- A ceramic furnace is a high-temperature heating device used for processes like firing ceramics, melting metals, or sintering materials.
- It is designed to achieve and maintain temperatures ranging from 1200°C to over 1500°C, depending on the application.
- These furnaces are essential in industries such as ceramics, metallurgy, and laboratory research, where precise and uniform heating is critical.
-
Core Components of a Ceramic Furnace:
-
Firing/Heating Chamber:
- The chamber is the central component where materials are placed for heating.
- It is typically made of high-temperature-resistant materials like ceramics (e.g., silica, alumina) to withstand extreme heat.
- In some designs, the chamber is cylindrical (tube furnace) or rectangular (muffle furnace).
-
Heating Elements:
- Heating elements, often made of refractory materials like silicon carbide or molybdenum disilicide, generate heat.
- These elements are embedded in the furnace walls or surrounding the chamber to ensure even heat distribution.
-
Insulation:
- Insulation materials, such as ceramic fiber or refractory bricks, are used to retain heat and improve energy efficiency.
- They also protect the external enclosure from excessive heat.
-
Electronic Control System:
- A microprocessor-based PID (Proportional-Integral-Derivative) controller regulates temperature with high precision.
- The system includes sensors (e.g., thermocouples) for real-time temperature monitoring and feedback.
- Features like timers, safety switches, and LED displays enhance usability and safety.
-
Firing/Heating Chamber:
-
Types of Ceramic Furnaces:
-
Muffle Furnace:
- Features an internal chamber insulated from the external environment, preventing contamination.
- Commonly used for applications requiring clean heating, such as ceramic firing or ash testing.
-
Tube Furnace:
- Consists of a cylindrical heating chamber surrounded by heating coils embedded in a ceramic matrix.
- Ideal for processes requiring uniform heating, such as material synthesis or heat treatment.
-
Crucible Furnace:
- Includes a crucible (made of graphite, clay, or silicon carbide) placed inside a heating chamber.
- Used for melting metals or other materials at high temperatures.
-
Porcelain Furnace:
- Specifically designed for dental or industrial porcelain firing.
- Equipped with a vacuum pump to prevent opacity and ensure high-quality results.
-
Muffle Furnace:
-
Applications of Ceramic Furnaces:
-
Ceramics Manufacturing:
- Used for firing pottery, tiles, and other ceramic products to achieve desired hardness and durability.
-
Metallurgy:
- Employed for melting metals, heat treatment, and sintering powdered metals.
-
Laboratory Research:
- Utilized in material science for experiments requiring controlled high-temperature environments.
-
Dental Industry:
- Porcelain furnaces are used to create dental prosthetics like crowns and bridges.
-
Ceramics Manufacturing:
-
Key Features and Advantages:
-
High-Temperature Capability:
- Can reach temperatures up to 1530°C or higher, suitable for a wide range of materials.
-
Precision Control:
- Advanced PID controllers ensure accurate temperature regulation and uniformity.
-
Durability:
- Constructed with refractory materials that withstand extreme heat and thermal cycling.
-
Safety Features:
- Includes safety switches, gas release holes, and insulation to prevent accidents and ensure operator safety.
-
Versatility:
- Available in various designs to meet specific application requirements.
-
High-Temperature Capability:
In summary, a ceramic furnace is a highly specialized and versatile tool designed for high-temperature processing. Its robust construction, precise temperature control, and adaptability make it indispensable in industries ranging from ceramics and metallurgy to laboratory research and dental applications.
Summary Table:
Aspect | Details |
---|---|
Definition | High-temperature device for firing, melting, or sintering materials. |
Temperature Range | 1200°C to 1530°C or higher. |
Core Components | Firing chamber, heating elements, insulation, electronic control system. |
Types | Muffle, tube, crucible, and porcelain furnaces. |
Applications | Ceramics manufacturing, metallurgy, lab research, dental prosthetics. |
Key Features | High-temperature capability, precision control, durability, safety, versatility. |
Discover how a ceramic furnace can elevate your high-temperature processes—contact us today for expert guidance!