Thermoforming is a cost-effective alternative to injection moulding, particularly for producing relatively simple plastic parts such as packaging containers, vehicle door panels, and dashboards, especially in low-to-mid volume production runs. Unlike injection moulding, which requires complex and expensive multi-part moulds, thermoforming uses a simpler single-sided press mold, significantly reducing tooling costs. This method is ideal for applications where the complexity of the part is low, and the production volumes do not justify the high initial investment of injection moulding. Thermoforming offers a practical solution for manufacturers looking to balance cost-efficiency with quality and functionality in plastic part production.
Key Points Explained:
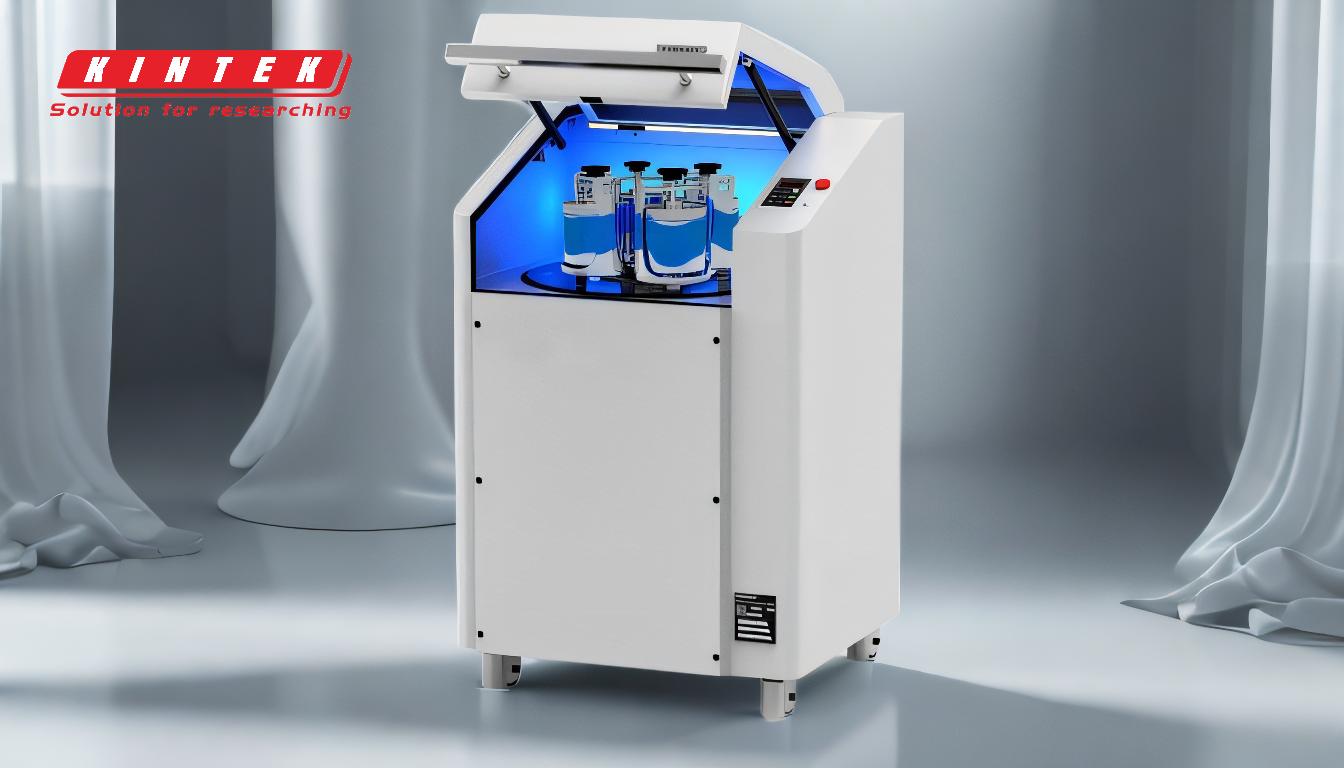
-
Thermoforming as a Cost-Effective Alternative:
- Thermoforming is highlighted as a cheaper alternative to injection moulding, particularly suitable for simpler plastic parts.
- It is especially advantageous for low-to-mid volume production runs where the high costs of injection moulding tools are not justified.
-
Applications Suitable for Thermoforming:
- Common applications include packaging containers, vehicle door panels, and dashboards.
- These parts typically have simpler geometries, making them ideal candidates for thermoforming processes.
-
Advantages of Using Single-Sided Moulds:
- Thermoforming requires only a single-sided mould, which is simpler and less expensive to produce compared to the multi-part moulds used in injection moulding.
- This reduction in tooling costs is a significant factor in the overall cost-effectiveness of thermoforming.
-
Considerations for Choosing Thermoforming:
- The decision to use thermoforming should consider the complexity of the part and the production volume.
- For parts with intricate designs or high production volumes, injection moulding might still be the preferred method despite higher costs.
-
Impact on Production and Manufacturing:
- By opting for thermoforming, manufacturers can achieve considerable savings on tooling and setup costs.
- This method allows for flexibility in production, enabling quicker changes and adaptations in the manufacturing process, which is beneficial for custom or variable production runs.
Summary Table:
Aspect | Thermoforming | Injection Moulding |
---|---|---|
Tooling Costs | Lower (single-sided mould) | Higher (multi-part mould) |
Production Volume | Ideal for low-to-mid volume runs | Suitable for high-volume production |
Part Complexity | Best for simpler geometries (e.g., packaging, vehicle panels) | Better for intricate designs |
Flexibility | Easier to adapt for custom or variable production runs | Less flexible due to higher setup costs |
Applications | Packaging containers, vehicle door panels, dashboards | Complex parts requiring high precision |
Want to explore how thermoforming can save your manufacturing costs? Contact us today for expert advice!