Furnace brazing is a high-precision industrial process used to join metallic materials by heating them to a temperature where a filler metal melts and flows into the joint through capillary action. This method is particularly effective for creating strong, seamless joints in complex assemblies, making it ideal for industries like aerospace, particle physics, and metallurgical research. A vacuum brazing furnace is a specialized type of furnace used in this process, offering advantages such as high temperature uniformity, oxidation prevention, and precise cycle programming. It operates under vacuum conditions, which eliminates the need for flux, reduces contamination, and ensures high-quality brazed joints with minimal deformation and excellent mechanical properties.
Key Points Explained:
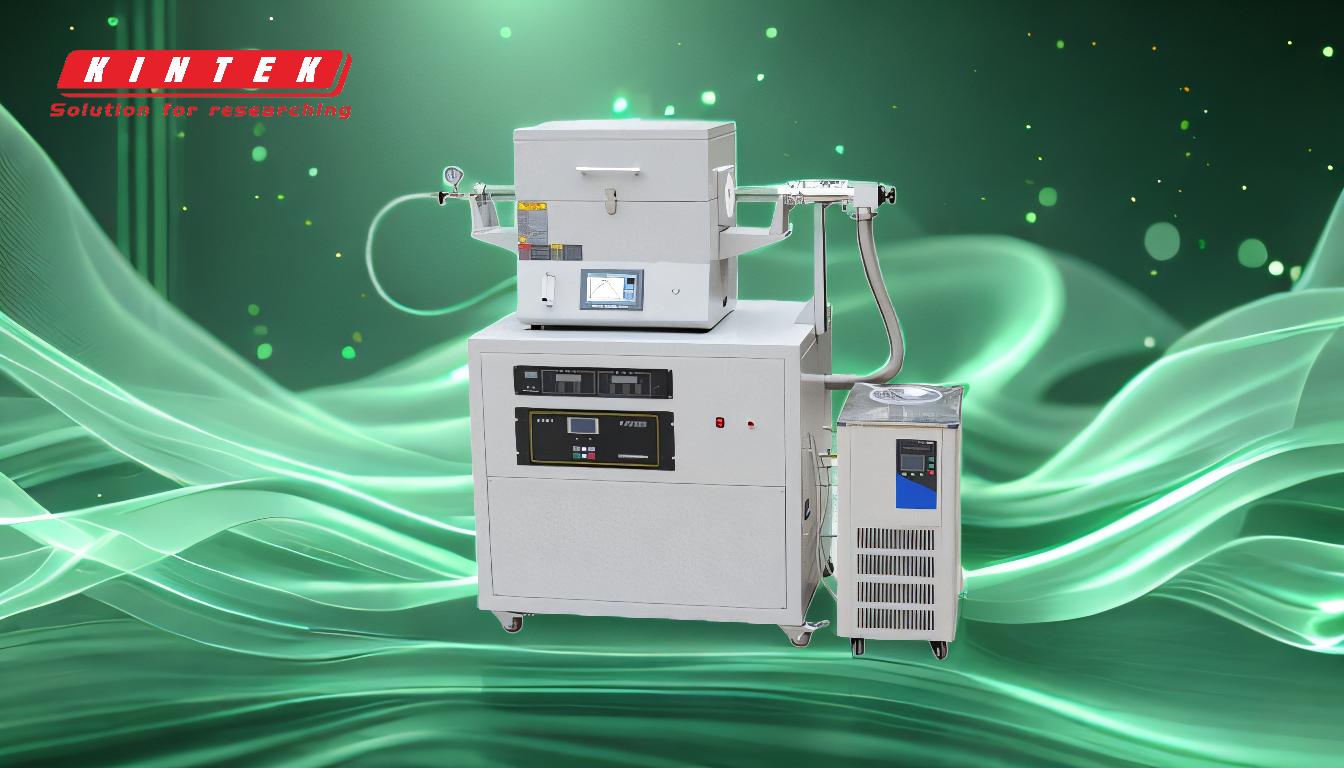
-
Definition of Furnace Brazing:
- Furnace brazing is a process where metallic materials are joined using a molten filler metal that flows into the joint through capillary action. The entire assembly is heated to the melting point of the filler metal, which then solidifies upon cooling to form a strong bond.
- This method is highly efficient for creating multiple joints simultaneously, making it suitable for high-volume industrial applications.
-
Role of a Vacuum Brazing Furnace:
- A vacuum brazing furnace is designed to operate under reduced pressure, preventing oxidation and decarburization of the workpiece surface. This results in joints with fewer defects, such as pinholes or segregation, and ensures high mechanical strength.
- The furnace features a vacuum system (with components like mechanical pumps and diffusion pumps) and a heating system, which work together to maintain precise temperature control and vacuum levels during the brazing process.
-
Key Features of Vacuum Brazing Furnaces:
- High Temperature Uniformity: Ensures consistent heating cycles, even for large or multiple workpieces.
- Oxide Layer Removal: Operates at temperatures higher than oxide formation, allowing oxidized pieces to lose their oxide layer before brazing.
- Precision Programming: Recognizes workpieces via barcode-linked cycle programs, ensuring tailored heating cycles for each piece.
- No Flux Required: Eliminates the need for flux, reducing contamination and simplifying the process.
-
Advantages of Furnace Brazing:
- Strong Joints: Creates seamless, high-strength joints with excellent mechanical properties.
- Versatility: Suitable for a wide range of materials and complex assemblies.
- Efficiency: Allows for the simultaneous brazing of thousands of joints, reducing production time.
- Pollution-Free: Operates without flux, making it environmentally friendly and cost-effective.
-
Applications of Furnace Brazing:
- Aerospace: Used for joining critical components that require high precision and strength.
- Particle Physics: Ideal for creating specialized equipment with stringent quality requirements.
- Metallurgical Research: Enables the study of material properties and joint integrity under controlled conditions.
-
Process Steps in Vacuum Brazing:
- Workpiece Preparation: Assemble the parts to be brazed and place them in the vacuum chamber.
- Vacuum Creation: Start the mechanical vacuum pump and connect the diffusion pump to achieve the required vacuum level.
- Heating: Heat the workpiece to the brazing temperature while maintaining the vacuum to prevent oxidation.
- Cooling: Allow the workpiece to cool to a safe temperature before removal to avoid oxidation.
-
Benefits of Vacuum Brazing Over Traditional Methods:
- No Flux Corrosion: Eliminates the risk of flux-related corrosion, improving the longevity of the joint.
- Enhanced Surface Quality: Produces smooth, dense brazing seams that are ideal for subsequent treatments.
- Cost-Effective: Simple brazing fixtures and shorter production cycles reduce overall costs.
In summary, furnace brazing, particularly when performed in a vacuum brazing furnace, is a highly efficient and precise method for joining metallic materials. Its ability to produce strong, contamination-free joints with minimal deformation makes it indispensable in industries requiring high-performance components.
Summary Table:
Aspect | Details |
---|---|
Definition | Joins metallic materials using a molten filler metal via capillary action. |
Key Features | High temperature uniformity, oxide layer removal, no flux required. |
Advantages | Strong joints, versatility, efficiency, pollution-free. |
Applications | Aerospace, particle physics, metallurgical research. |
Process Steps | Workpiece preparation, vacuum creation, heating, cooling. |
Benefits Over Traditional Methods | No flux corrosion, enhanced surface quality, cost-effective. |
Ready to enhance your metal joining process? Contact us today to learn more about vacuum brazing furnaces!