A furnace retort is a specialized type of furnace designed for processes that require controlled atmospheres or vacuum conditions. It is commonly used in industries such as metallurgy, materials science, and manufacturing for heat treatment, sintering, brazing, and other thermal processes. The retort furnace can be constructed in either horizontal or vertical configurations, depending on the application. It typically features a sealed chamber (the retort) that isolates the material being processed from the external environment, allowing precise control over temperature and atmosphere. Heating is achieved through electrical resistance heaters or gas burners, and advanced designs may include water-cooled structures, vacuum systems, and sophisticated control mechanisms to ensure optimal performance.
Key Points Explained:
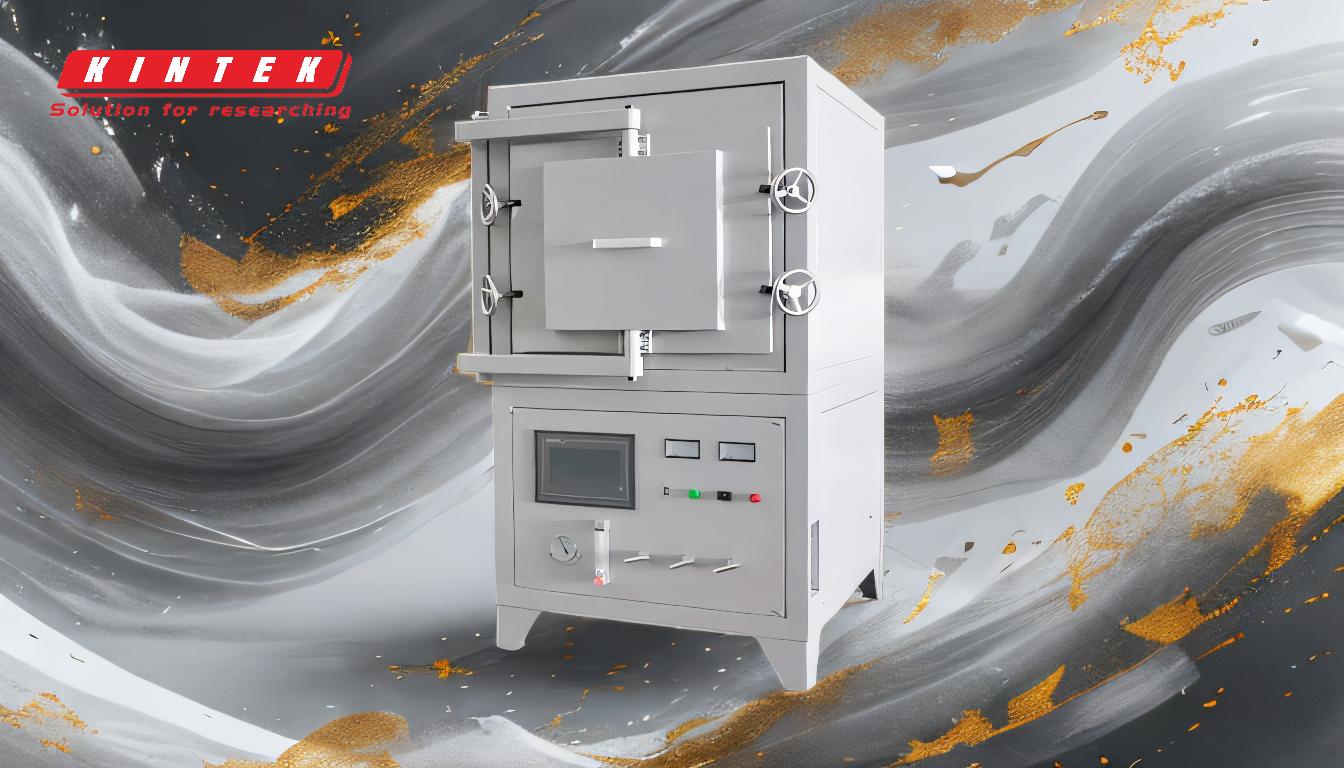
-
Definition and Purpose of a Furnace Retort:
- A furnace retort is a sealed chamber within a furnace that isolates the material being processed from the external environment. This design allows for precise control over the atmosphere (e.g., inert gases, vacuum) and temperature, making it ideal for processes like heat treatment, sintering, and brazing.
-
Horizontal and Vertical Configurations:
- Retort furnaces can be built in either horizontal or vertical orientations. The choice depends on the specific application and the type of materials being processed. Horizontal designs are often used for continuous processing, while vertical designs are preferred for batch processing or when space is limited.
-
Heating Mechanisms:
- The heating in a retort furnace is typically achieved through electrical resistance heaters or gas burners. These heating systems provide uniform and controlled temperatures, ensuring consistent results in the thermal processing of materials.
-
Sealed Chamber (Retort):
- The retort itself is a key component, designed to maintain a controlled atmosphere or vacuum. This is crucial for processes that require protection from oxidation or contamination. The chamber is often made of materials like stainless steel to withstand high temperatures and corrosive environments.
-
Advanced Features:
- Modern retort furnaces may include advanced features such as double-layer water-cooled structures, vacuum systems, and sophisticated control systems. For example, the furnace cover might have a water-cooled sandwich structure with polished stainless steel inner walls and anti-rust-treated outer walls. These features enhance durability, safety, and performance.
-
Applications:
- Retort furnaces are widely used in industries that require precise thermal processing under controlled conditions. Common applications include the heat treatment of metals, sintering of ceramics, and brazing of components. The ability to maintain a controlled atmosphere or vacuum makes them indispensable for high-quality manufacturing processes.
-
Maintenance and Repairability:
- Components of a retort furnace, such as the heating elements, vacuum systems, and cooling systems, are designed for easy maintenance. Degrading parts like hot zones, cooling jackets, and vacuum pumps can often be cleaned, repaired, or replaced, ensuring long-term reliability and cost-effectiveness.
By combining these features, a furnace retort provides a versatile and efficient solution for a wide range of thermal processing applications, ensuring high-quality results and operational flexibility.
Summary Table:
Key Aspect | Details |
---|---|
Definition | Sealed chamber for controlled atmosphere or vacuum thermal processing. |
Configurations | Horizontal (continuous processing) or vertical (batch processing). |
Heating Mechanisms | Electrical resistance heaters or gas burners for uniform temperature control. |
Sealed Chamber | Made of stainless steel to withstand high temperatures and corrosion. |
Advanced Features | Water-cooled structures, vacuum systems, and sophisticated controls. |
Applications | Heat treatment, sintering, brazing in metallurgy and materials science. |
Maintenance | Easy-to-repair components like heating elements and vacuum systems. |
Need a furnace retort for your thermal processing needs? Contact us today to find the perfect solution!