A high-temperature furnace is a specialized heating device designed to operate at extremely high temperatures, typically ranging from 1000°C to 3000°C, depending on the application. It is widely used in industries such as ceramics, metallurgy, electronics, glass, and chemical processing, as well as in research institutions and universities. These furnaces are essential for processes like sintering, annealing, heat treatment, material testing, and high-temperature experiments. They are engineered to provide precise temperature control, uniform heating, and often operate under controlled atmospheres or vacuum conditions to meet the specific requirements of advanced materials and industrial processes.
Key Points Explained:
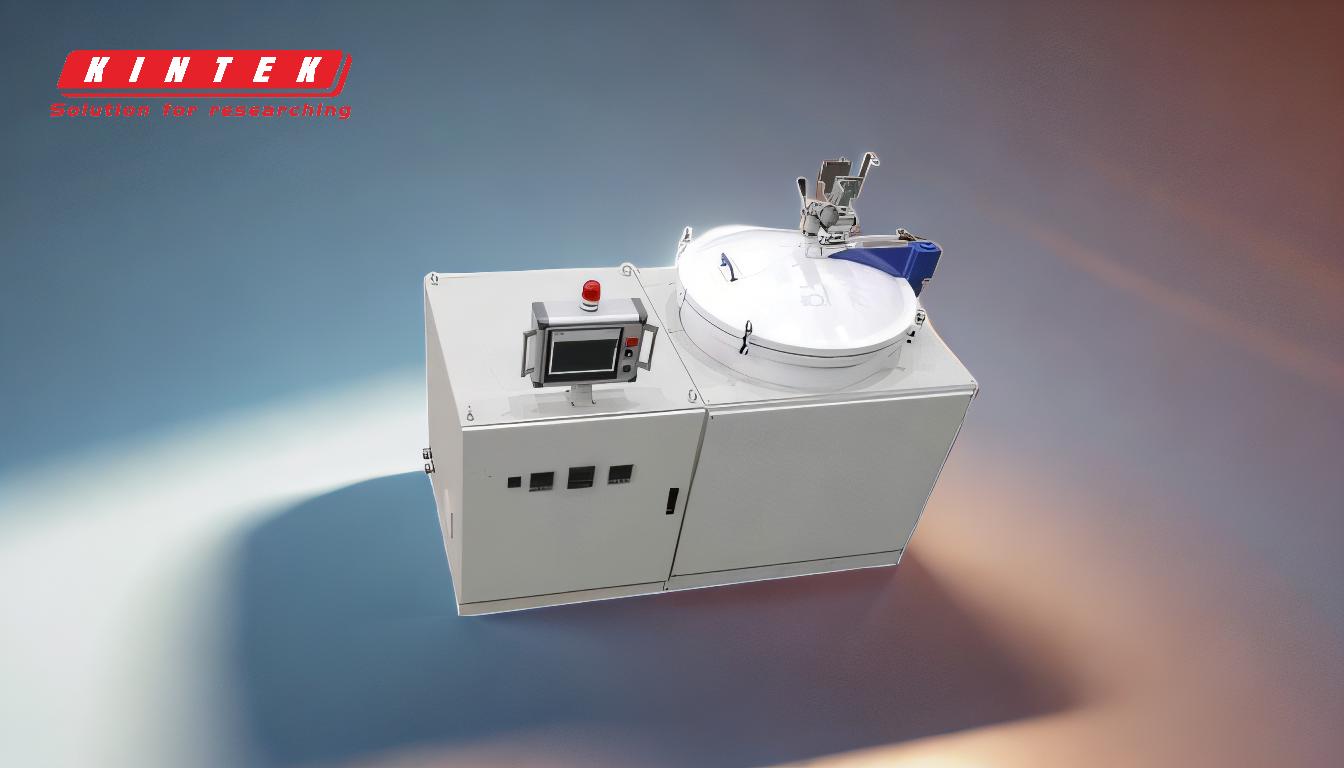
-
Definition and Purpose of a High-Temperature Furnace
- A high temperature furnace is a device capable of reaching and maintaining extremely high temperatures, often exceeding 1000°C.
- Its primary purpose is to facilitate processes such as sintering, annealing, hardening, and heat treatment of materials like metals, ceramics, and composites.
- It is also used for elemental analysis, material testing, and high-temperature experiments in research and industrial settings.
-
Applications Across Industries
- Ceramics and Glass: Used for sintering ceramic powders, firing glass, and processing advanced ceramic materials.
- Metallurgy: Essential for heat treatment processes like annealing, hardening, and tempering of metals and alloys.
- Electronics: Utilized in the production of semiconductors and electronic components requiring precise thermal processing.
- Chemical Industry: Applied in high-temperature reactions, catalyst testing, and material synthesis.
- Research and Development: Used in universities and scientific research institutes for material testing and high-temperature experiments.
-
Types of High-Temperature Furnaces
- Tube Furnaces: Ideal for processes like calcination, sintering, and annealing. They are versatile and can operate under controlled atmospheres or vacuum.
- Induction Furnaces: Use electromagnetic fields to heat conductive materials directly, making them suitable for melting metals and creating alloys.
- Hot Press Sintering Furnaces: Combine high temperature and pressure in a vacuum environment to densify materials like ceramics and composites.
-
Key Components and Functionality
- Heating Elements: Made from materials like silicon carbide, molybdenum disilicide, or graphite, capable of withstanding extreme temperatures.
- Insulation: High-quality refractory materials are used to minimize heat loss and ensure energy efficiency.
- Temperature Control Systems: Advanced controllers and thermocouples ensure precise temperature regulation and uniformity.
- Atmosphere Control: Some furnaces can operate under inert gases, reducing atmospheres, or vacuum to prevent oxidation or contamination.
-
Operational Processes
- Loading: Materials or samples are placed inside the furnace chamber.
- Heating: The furnace is heated to the desired temperature at a controlled rate.
- Processing: The material undergoes the required thermal treatment, such as sintering, annealing, or melting.
- Cooling: The furnace is cooled gradually to prevent thermal shock and ensure material integrity.
-
Advantages of High-Temperature Furnaces
- Precision: Offers accurate temperature control and uniform heating for consistent results.
- Versatility: Suitable for a wide range of materials and processes.
- Efficiency: Advanced insulation and heating elements reduce energy consumption.
- Customization: Can be tailored to meet specific industrial or research requirements.
-
Considerations for Purchasers
- Temperature Range: Ensure the furnace can reach the required temperatures for your applications.
- Atmosphere Control: Determine if you need vacuum, inert gas, or reducing atmosphere capabilities.
- Heating Rate and Uniformity: Look for furnaces with fast heating rates and excellent temperature uniformity.
- Durability and Maintenance: Choose furnaces with robust construction and easy maintenance features.
- Safety Features: Ensure the furnace has safety mechanisms like over-temperature protection and emergency shut-off.
By understanding these key points, purchasers and users can make informed decisions when selecting a high-temperature furnace that meets their specific needs and applications.
Summary Table:
Aspect | Details |
---|---|
Temperature Range | 1000°C to 3000°C |
Applications | Ceramics, metallurgy, electronics, chemical processing, research |
Key Processes | Sintering, annealing, heat treatment, material testing |
Types | Tube furnaces, induction furnaces, hot press sintering furnaces |
Key Components | Heating elements, insulation, temperature control, atmosphere control |
Advantages | Precision, versatility, efficiency, customization |
Considerations | Temperature range, atmosphere control, heating rate, durability, safety |
Ready to find the perfect high-temperature furnace for your needs? Contact us today to get expert advice and solutions!