A high-temperature hydrogen annealing furnace is a specialized heating equipment designed to perform annealing, sintering, brazing, and other thermal processes in a high-purity hydrogen or hydrogen-nitrogen atmosphere. It is widely used in industries such as ceramics, metallurgy, semiconductors, and glass sealing due to its ability to reduce oxidation, ensure uniform heating, and achieve precise temperature control. The furnace operates at temperatures up to 1600℃, with features like rapid heating and cooling, automatic temperature control, and the ability to store multiple heating programs. Its applications include ceramic sintering, powder metallurgy, semiconductor alloy processing, and annealing of glass and metal parts.
Key Points Explained:
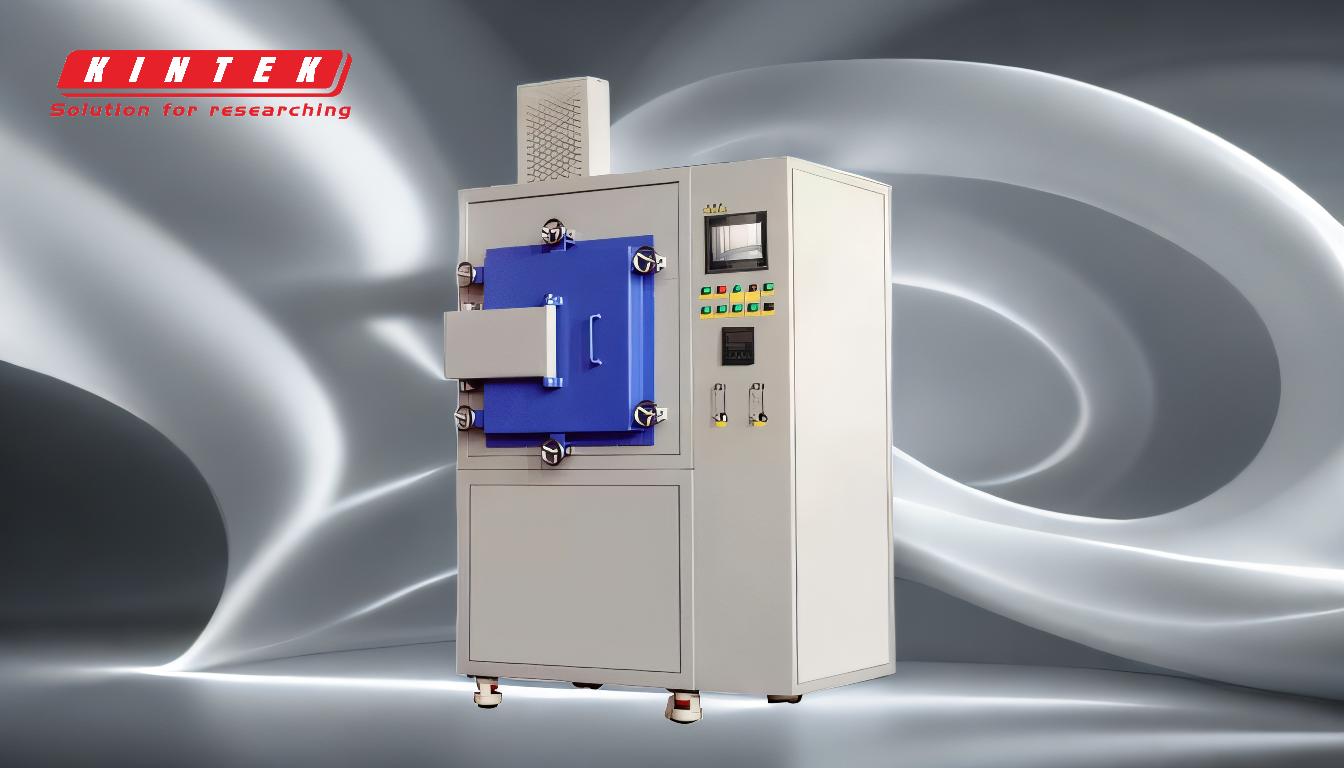
-
Definition and Purpose:
- A high-temperature hydrogen annealing furnace is a heating device that uses hydrogen or a hydrogen-nitrogen mixture (with hydrogen content >5%) as a protective atmosphere.
- It is designed to prevent oxidation and contamination during high-temperature processes like annealing, sintering, brazing, and purification.
-
Key Features:
- High-Purity Hydrogen Environment: Ensures a clean, oxidation-free atmosphere for sensitive materials.
- Temperature Capabilities: Operates at temperatures up to 1600℃, suitable for demanding industrial processes.
- Uniform Heating: Heating elements on all sides of the chamber ensure consistent temperature distribution.
- Rapid Heating and Cooling: Enhances process efficiency and reduces cycle times.
- Automatic and Manual Control: Offers flexibility in operation with precise temperature control (±1℃) and uniformity (±3℃ to ±10℃).
- Programmable Heating Profiles: Stores multiple heating programs to accommodate various process requirements.
-
Applications:
- Ceramic Sintering: Used to densify ceramic materials without oxidation.
- Metallization and Brazing: Joins metals and ceramics in a controlled atmosphere.
- Glass Sealing: Anneals and purifies glass parts for sealing with metals.
- Powder Metallurgy: Sinters metal powders into solid components.
- Semiconductor Alloy Processing: Processes semiconductor materials in a contamination-free environment.
-
Advantages:
- Oxidation Prevention: The hydrogen atmosphere reduces oxidation, improving the quality of treated materials.
- Versatility: Suitable for a wide range of materials and processes.
- Precision: High accuracy in temperature control ensures consistent results.
- Efficiency: Rapid heating and cooling reduce processing time and energy consumption.
-
Design Considerations:
- Horizontal or Vertical Configuration: Depending on the application, furnaces may be designed horizontally or vertically.
- Vacuum Compatibility: Some models, like horizontal vacuum annealing furnaces, can operate under vacuum conditions to further enhance oxidation resistance.
- Cooling Mechanisms: Features like movable furnace bodies or cooling systems improve cooling rates while maintaining a controlled atmosphere.
-
Industrial Relevance:
- Essential for industries requiring high-temperature processing in a controlled, oxidation-free environment.
- Enables the production of high-quality components in ceramics, metallurgy, semiconductors, and glass-to-metal sealing.
By combining these features and capabilities, a high-temperature hydrogen annealing furnace provides a reliable and efficient solution for advanced material processing and industrial applications.
Summary Table:
Key Features | Applications | Advantages |
---|---|---|
High-purity hydrogen environment | Ceramic sintering | Oxidation prevention |
Temperature up to 1600℃ | Metallization and brazing | Versatility for various materials |
Uniform heating | Glass sealing | Precise temperature control (±1℃) |
Rapid heating and cooling | Powder metallurgy | Efficient processing |
Programmable heating profiles | Semiconductor alloy processing | Consistent results |
Looking for a high-temperature hydrogen annealing furnace? Contact us today to find the perfect solution for your needs!