Press molds are versatile tools used in various industries and crafts, primarily for shaping materials into specific forms. In pottery, press molding involves forcing clay into a mold to create uniform, replicable shapes, similar to metal casting. Beyond pottery, press molds are utilized in industries such as pharmaceuticals, ceramics, polymers, and composites, where they help shape materials under controlled pressure. These molds ensure consistency, precision, and efficiency in production processes, making them indispensable for creating standardized products.
Key Points Explained:
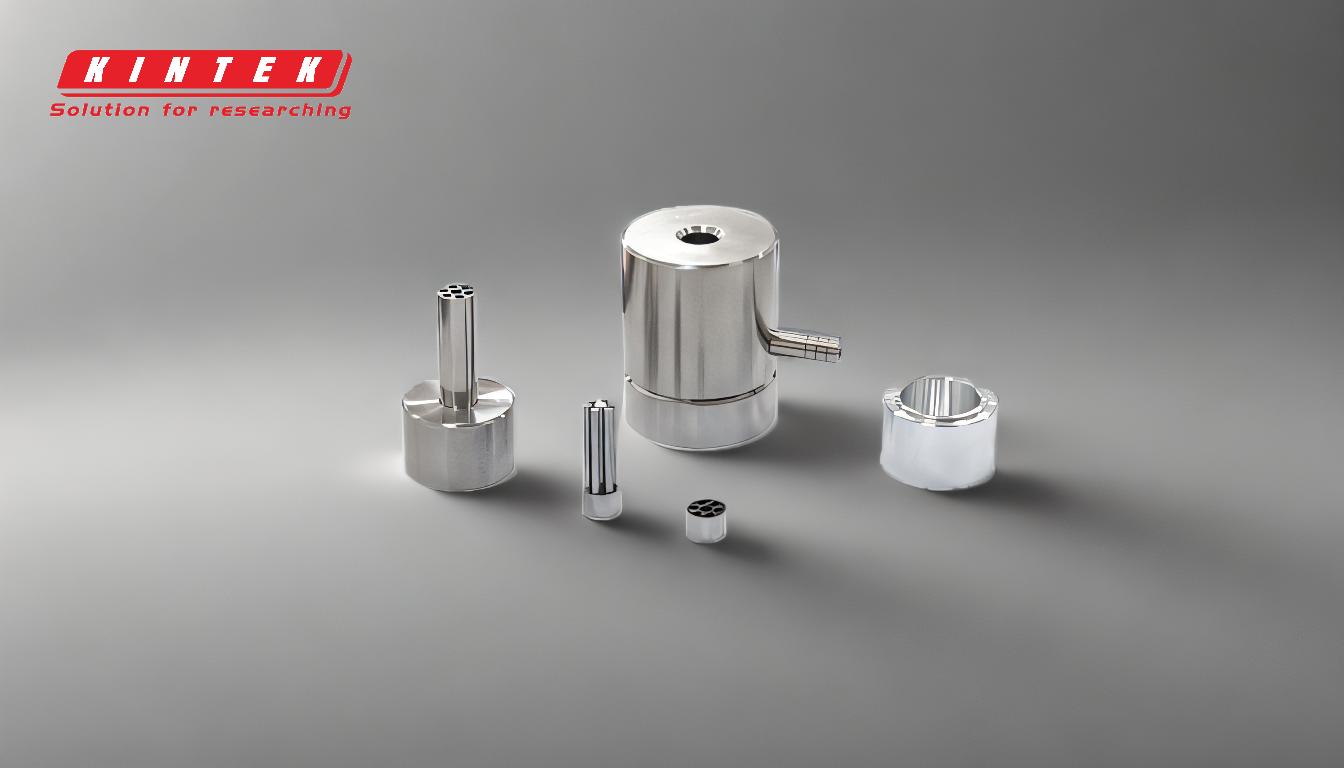
-
Definition and Basic Function of Press Molds
- A press mold is a tool used to shape materials by applying pressure, forcing them into a predefined form.
- The mold's interior design determines the final shape of the product, ensuring uniformity and consistency across multiple pieces.
-
Applications in Pottery
- In pottery, press molding involves pressing clay into a mold to replicate intricate or consistent shapes.
- This method is particularly useful for creating identical pieces, such as tiles, plates, or decorative items, without requiring extensive handcrafting.
- Once the clay is pressed and the mold is removed, the piece retains the mold's interior shape, ready for drying and firing.
-
Industrial Applications
- Polymers and Composites: Press molds are used to shape materials like plastics and fiber-reinforced composites into components for automotive, aerospace, and consumer goods.
- Ceramics: Beyond pottery, industrial ceramics are often shaped using press molds for applications in electronics, construction, and machinery.
- Pharmaceuticals: Press molds play a role in tablet manufacturing, where powdered ingredients are compressed into precise shapes and sizes for medication.
-
Advantages of Press Molding
- Consistency: Press molds ensure that each product is identical, which is crucial for mass production and quality control.
- Efficiency: The process is faster and less labor-intensive compared to hand-shaping methods.
- Precision: Molds can be designed to produce highly detailed and complex shapes that would be difficult to achieve manually.
-
Types of Press Molds
- Single-Piece Molds: Simple molds used for basic shapes, often in pottery or small-scale production.
- Multi-Piece Molds: Complex molds with multiple parts, allowing for intricate designs and undercuts.
- Hydraulic or Mechanical Press Molds: Used in industrial settings, these molds apply significant pressure to shape harder materials like metals or dense composites.
-
Considerations for Purchasing Press Molds
- Material Compatibility: Ensure the mold material (e.g., plaster, silicone, or metal) is suitable for the substance being shaped.
- Durability: Industrial applications require molds made from robust materials to withstand repeated use and high pressure.
- Design Complexity: Choose molds that match the desired level of detail and intricacy for the final product.
- Cost: Balance the initial investment with the expected production volume and mold lifespan.
-
Maintenance and Care
- Regularly clean molds to prevent material buildup, which can affect product quality.
- Inspect molds for wear and tear, especially in high-pressure industrial applications, to avoid defects in the final product.
- Store molds properly to prevent damage or deformation when not in use.
By understanding the versatility and functionality of press molds, purchasers can make informed decisions about their use in various applications, ensuring efficiency, consistency, and high-quality results.
Summary Table:
Aspect | Details |
---|---|
Definition | Tools used to shape materials by applying pressure into predefined forms. |
Applications | Pottery, pharmaceuticals, ceramics, polymers, and composites. |
Advantages | Consistency, efficiency, and precision in mass production. |
Types | Single-piece, multi-piece, hydraulic/mechanical press molds. |
Considerations | Material compatibility, durability, design complexity, and cost. |
Maintenance | Regular cleaning, inspection for wear, and proper storage. |
Ready to enhance your production process with press molds? Contact us today for expert guidance!