A sintered element is a solid structure created through the sintering process, which involves bonding small particles of materials like metal, ceramic, or plastic under high heat and pressure without melting them completely. This process allows for precise control over the material's porosity, density, and strength, making it ideal for applications in industries such as automotive, biomedical, and manufacturing. Sintering is a versatile and efficient method for producing durable and complex components with tailored properties.
Key Points Explained:
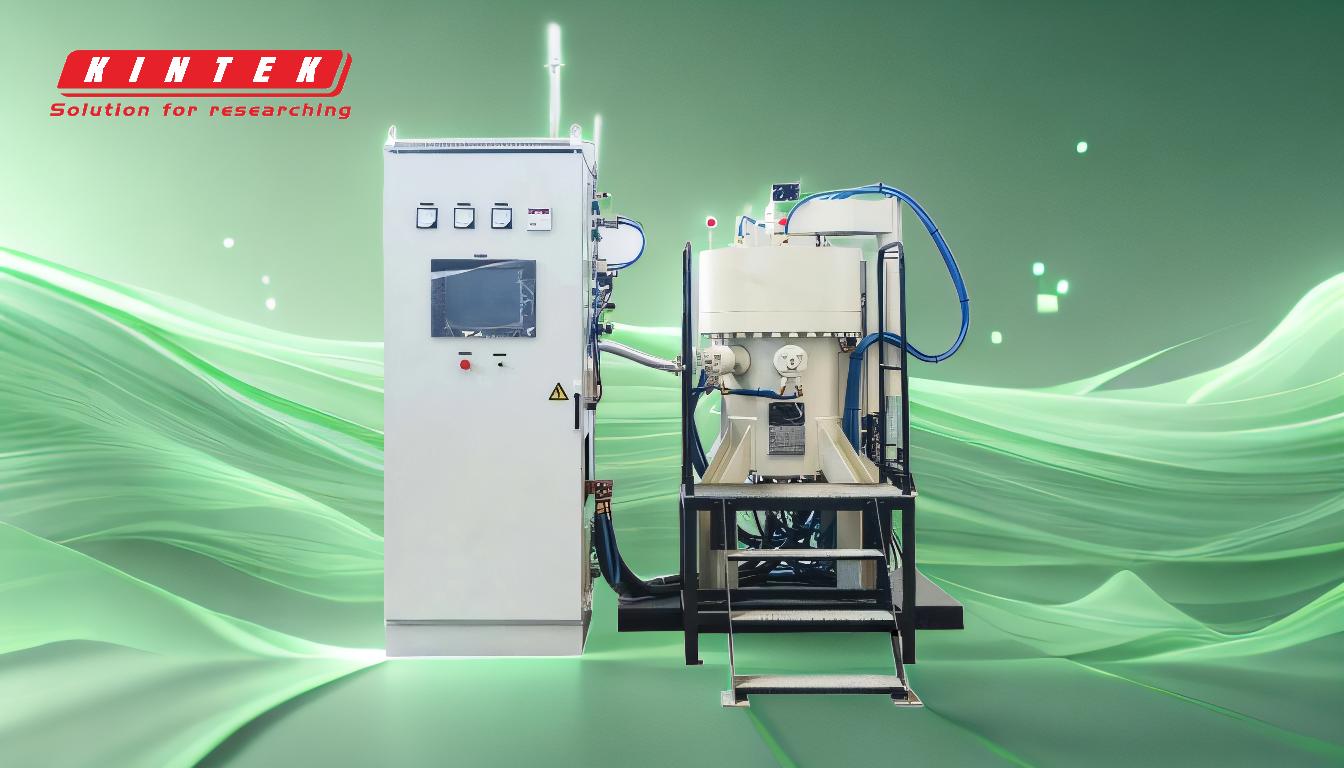
-
Definition of Sintering:
- Sintering is a manufacturing process that bonds small particles of materials (e.g., metal, ceramic, plastic) into a solid mass using heat and pressure below the material's melting point.
- It avoids liquefaction, instead relying on atomic diffusion across particle boundaries to fuse the material into a cohesive structure.
-
How Sintering Works:
- Heat and pressure are applied to powdered materials, causing the particles to bond at their surfaces.
- The process reduces porosity and compacts the material into a denser, stronger form.
- It is particularly useful for materials with high melting points, such as tungsten and molybdenum.
-
Benefits of Sintering:
- Precision Control: Allows for precise control over pore size and distribution, enabling customization of material properties like permeability and strength.
- Versatility: Can be used with a wide range of materials, including metals, ceramics, and plastics.
- Durability: Produces components that are harder, stronger, and more durable than those made through traditional methods.
- Complex Shapes: Enables the creation of intricate and complex shapes that are difficult to achieve with other manufacturing processes.
-
Applications of Sintered Elements:
- Automotive Industry: Used for components like gears, bearings, and filters due to their strength and wear resistance.
- Biomedical Field: Sintered stainless-steel components are used in medical devices and implants because of their biocompatibility and durability.
- Mechanical Engineering: Employed in the production of tools, machinery parts, and structural components.
- Fashion and Jewelry: Sintered metals are used to create intricate designs and lightweight yet durable accessories.
-
Sintering Technologies:
- Powder Pressing: Compacts metal powders into a desired shape before sintering.
- Metal Injection Molding (MIM): Combines powdered metal with a binder to create complex shapes, which are then sintered.
- Binder Jetting Additive Manufacturing: Uses a 3D printing approach to layer powdered material and a binder, followed by sintering to fuse the layers.
- Metal FDM (Fused Deposition Modeling): A 3D printing technique that extrudes metal-filled filaments, which are then sintered to create solid parts.
-
Natural vs. Industrial Sintering:
- Natural Sintering: Occurs in mineral deposits over geological time scales due to heat and pressure.
- Industrial Sintering: A controlled process used in manufacturing to produce materials with specific properties for various applications.
-
Material Properties After Sintering:
- Reduced porosity and increased density.
- Enhanced mechanical properties, such as hardness, strength, and wear resistance.
- Improved thermal and electrical conductivity in some cases.
-
Common Materials Used in Sintering:
- Metals: Stainless steel, tungsten, molybdenum, and other alloys.
- Ceramics: Used in pottery, electronics, and high-temperature applications.
- Plastics: For lightweight and durable components.
By understanding the sintering process and its applications, purchasers of equipment and consumables can make informed decisions about the materials and technologies best suited for their needs. Sintered elements offer a unique combination of strength, precision, and versatility, making them invaluable across a wide range of industries.
Summary Table:
Aspect | Details |
---|---|
Definition | Bonding particles of metal, ceramic, or plastic under heat and pressure. |
Key Benefits | Precision control, versatility, durability, and ability to create complex shapes. |
Applications | Automotive (gears, bearings), biomedical (implants), and mechanical engineering. |
Common Materials | Metals (stainless steel, tungsten), ceramics, and plastics. |
Sintering Technologies | Powder pressing, metal injection molding, binder jetting, and metal FDM. |
Unlock the potential of sintered elements for your industry—contact us today!