A three-zone furnace is a specialized heating device designed to provide precise temperature control across three distinct zones within the furnace chamber. This configuration allows for uniform heating, temperature gradients, or specific thermal profiles tailored to the needs of various industrial processes, such as material testing, heat treatment, or semiconductor manufacturing. Each zone is independently controlled, enabling users to achieve optimal thermal conditions for complex applications. This type of furnace is particularly useful in scenarios where consistent heat distribution or controlled temperature variations are critical to the process.
Key Points Explained:
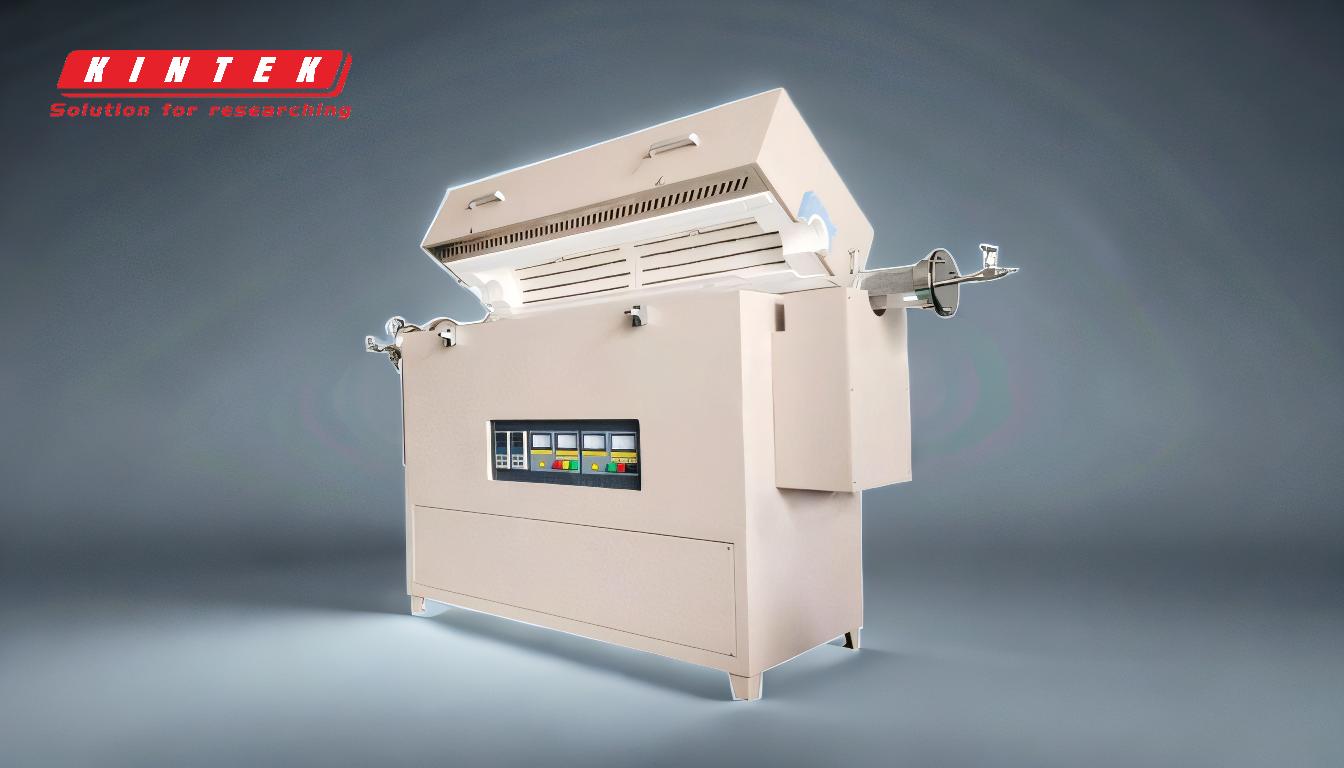
-
Definition and Structure of a Three-Zone Furnace
- A three-zone furnace is a type of industrial furnace divided into three separate heating zones, each with its own temperature control system.
- The furnace typically consists of a single chamber, but the heating elements and sensors are arranged to create distinct zones.
- This design allows for precise control over the thermal environment, making it suitable for applications requiring uniform heating or specific temperature gradients.
-
Independent Temperature Control
- Each zone in a three-zone furnace is equipped with its own set of heating elements and temperature sensors.
- This independence enables users to set different temperatures for each zone, creating a customized thermal profile.
- For example, one zone can be set to a high temperature for annealing, while another zone maintains a lower temperature for cooling or stress relief.
-
Applications of Three-Zone Furnaces
- Material Testing: Used to simulate real-world thermal conditions for testing the durability and performance of materials.
- Heat Treatment: Ideal for processes like annealing, tempering, and hardening, where precise temperature control is essential.
- Semiconductor Manufacturing: Ensures uniform heating during the production of semiconductor components, which are sensitive to temperature variations.
- Research and Development: Provides flexibility for experiments requiring controlled thermal environments.
-
Advantages of Three-Zone Furnaces
- Uniform Heating: The ability to control each zone independently ensures even heat distribution, reducing the risk of hot or cold spots.
- Flexibility: Users can create custom temperature profiles to meet the specific requirements of their processes.
- Energy Efficiency: By optimizing the temperature in each zone, energy consumption can be minimized, leading to cost savings.
- Improved Process Control: Enhanced precision in temperature management results in better-quality outputs and reduced material waste.
-
Considerations for Purchasing a Three-Zone Furnace
- Temperature Range: Ensure the furnace can achieve the required temperatures for your specific application.
- Zone Configuration: Verify that the furnace's zone layout aligns with your process needs.
- Control System: Look for advanced control features, such as programmable settings and real-time monitoring.
- Size and Capacity: Choose a furnace with a chamber size and load capacity suitable for your operations.
- Energy Efficiency: Consider models with energy-saving features to reduce operational costs.
In summary, a three-zone furnace is a versatile and highly controllable heating device that offers significant advantages for industries requiring precise thermal management. Its ability to independently regulate temperatures across multiple zones makes it an invaluable tool for achieving consistent and high-quality results in various applications.
Summary Table:
Feature | Description |
---|---|
Definition | A furnace with three independently controlled heating zones for precise thermal management. |
Applications | Material testing, heat treatment, semiconductor manufacturing, R&D. |
Advantages | Uniform heating, flexibility, energy efficiency, improved process control. |
Key Considerations | Temperature range, zone configuration, control system, size, energy efficiency. |
Looking for a three-zone furnace tailored to your needs? Contact our experts today to find the perfect solution!