A vacuum heat treatment furnace is a specialized piece of equipment designed to heat materials, typically metals, in a controlled, oxygen-free environment to achieve specific mechanical and physical properties. It operates by creating a vacuum within a sealed chamber, removing oxygen and nitrogen to prevent oxidation and contamination. The furnace uses electric heating elements to achieve high temperatures, often up to 2400°F, and employs advanced cooling systems like gas quenching or oil quenching to rapidly lower the temperature of the treated materials. This process is widely used in industries requiring high precision and quality, such as aerospace, automotive, and tool manufacturing, to enhance material properties like hardness, strength, and durability.
Key Points Explained:
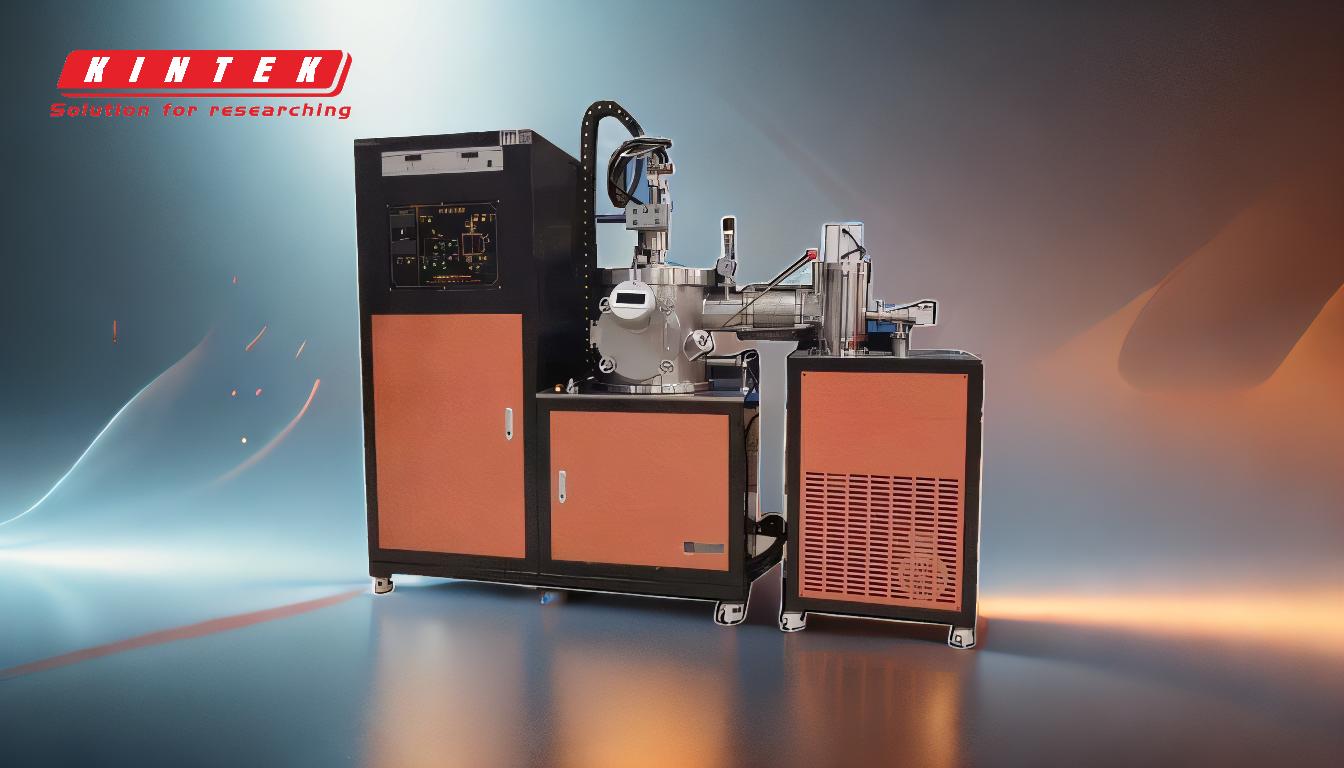
-
Definition and Purpose of a Vacuum Heat Treatment Furnace
- A vacuum heat treatment furnace is a sealed chamber where materials, particularly metals, are heated in a vacuum environment to prevent oxidation and contamination.
- Its primary purpose is to impart specific mechanical properties to materials, such as increased hardness, strength, and durability, through controlled heating and cooling processes.
-
Working Principle
- The furnace operates by creating a low-pressure environment, effectively removing air and replacing it with inert gases like argon.
- Electric heating elements generate heat, which is transferred to the materials being treated. The absence of oxygen prevents oxidation and decarburization, ensuring a clean and high-quality finish.
- The furnace can achieve temperatures up to 2400°F, with precise control over heating and cooling rates to meet specific material requirements.
-
Key Components
- Sealed Chamber: The core of the furnace, where the heat treatment process occurs. It is designed to maintain a vacuum and withstand high temperatures.
- Vacuum System: Removes air and gases from the chamber, creating a low-pressure environment.
- Heating Elements: Typically made of graphite or metal-ceramic, these elements provide the necessary heat for the process.
- Cooling System: Includes water-cooled tubes, heat-evacuating fans, and quenching stations (using oil or gas) to rapidly cool the materials after heating.
- Control Systems: Computer-controlled systems ensure precise temperature regulation, uniformity, and repeatability of the heat treatment process.
-
Advantages of Vacuum Heat Treatment
- Prevention of Oxidation and Contamination: The vacuum environment eliminates oxygen, preventing oxidation and ensuring a clean surface finish.
- Minimal Distortion: The controlled heating and cooling processes reduce the risk of warping or deformation, resulting in parts with precise dimensions.
- High-Quality Finished Products: The process removes impurities, leading to fewer defects such as pinholes and segregation, and producing materials with superior mechanical properties.
- Energy Efficiency: The furnace's design, with small heat storage and rapid temperature changes, results in significant energy savings compared to traditional refractory furnaces.
-
Applications
- Aerospace: Used to treat components that require high strength and resistance to extreme conditions.
- Automotive: Enhances the durability and performance of engine parts, gears, and other critical components.
- Tool Manufacturing: Improves the hardness and wear resistance of cutting tools, molds, and dies.
- Medical Devices: Ensures the biocompatibility and strength of surgical instruments and implants.
-
Customization and Flexibility
- Vacuum furnaces come in various sizes and configurations, allowing for customization based on specific industry needs.
- Features such as rapid cooling systems, gas quenching, and advanced temperature monitoring can be integrated to optimize the heat treatment process for different materials and desired outcomes.
-
Safety and Ease of Use
- The furnace is designed with user safety in mind, featuring automatic power-off functions when the furnace door is opened.
- It is simple to operate, with stable control systems that are easy to adjust, making it suitable for both experienced operators and those new to vacuum heat treatment.
-
Process Control and Repeatability
- The heat treatment process is computer-controlled, ensuring consistent and repeatable results.
- Parameters such as temperature, heating rate, cooling rate, and soak time can be precisely controlled, allowing for the customization of the process to meet the specific requirements of different materials and parts.
In summary, a vacuum heat treatment furnace is a highly advanced and versatile piece of equipment that plays a critical role in enhancing the properties of materials through precise and controlled heat treatment processes. Its ability to operate in a vacuum environment, combined with advanced heating and cooling systems, makes it an essential tool in industries where material performance and quality are paramount.
Summary Table:
Key Feature | Details |
---|---|
Purpose | Heat materials in a vacuum to prevent oxidation and enhance properties. |
Temperature Range | Up to 2400°F with precise control. |
Key Components | Sealed chamber, vacuum system, heating elements, cooling system, controls. |
Advantages | No oxidation, minimal distortion, high-quality finish, energy efficiency. |
Applications | Aerospace, automotive, tool manufacturing, medical devices. |
Customization | Available in various sizes with advanced features like gas quenching. |
Unlock the potential of vacuum heat treatment for your materials—contact us today to learn more!