Air melting is a process used in metallurgy and materials science to melt metals or alloys in the presence of air, typically in an open-air environment or using equipment that allows exposure to atmospheric conditions. This method is commonly employed in foundries and manufacturing facilities to produce castings, ingots, or other metal products. Unlike vacuum melting or controlled atmosphere melting, air melting does not involve isolating the molten metal from the surrounding air, which can lead to oxidation and the formation of impurities. Despite these challenges, air melting is widely used due to its simplicity, cost-effectiveness, and suitability for producing large quantities of metal.
Key Points Explained:
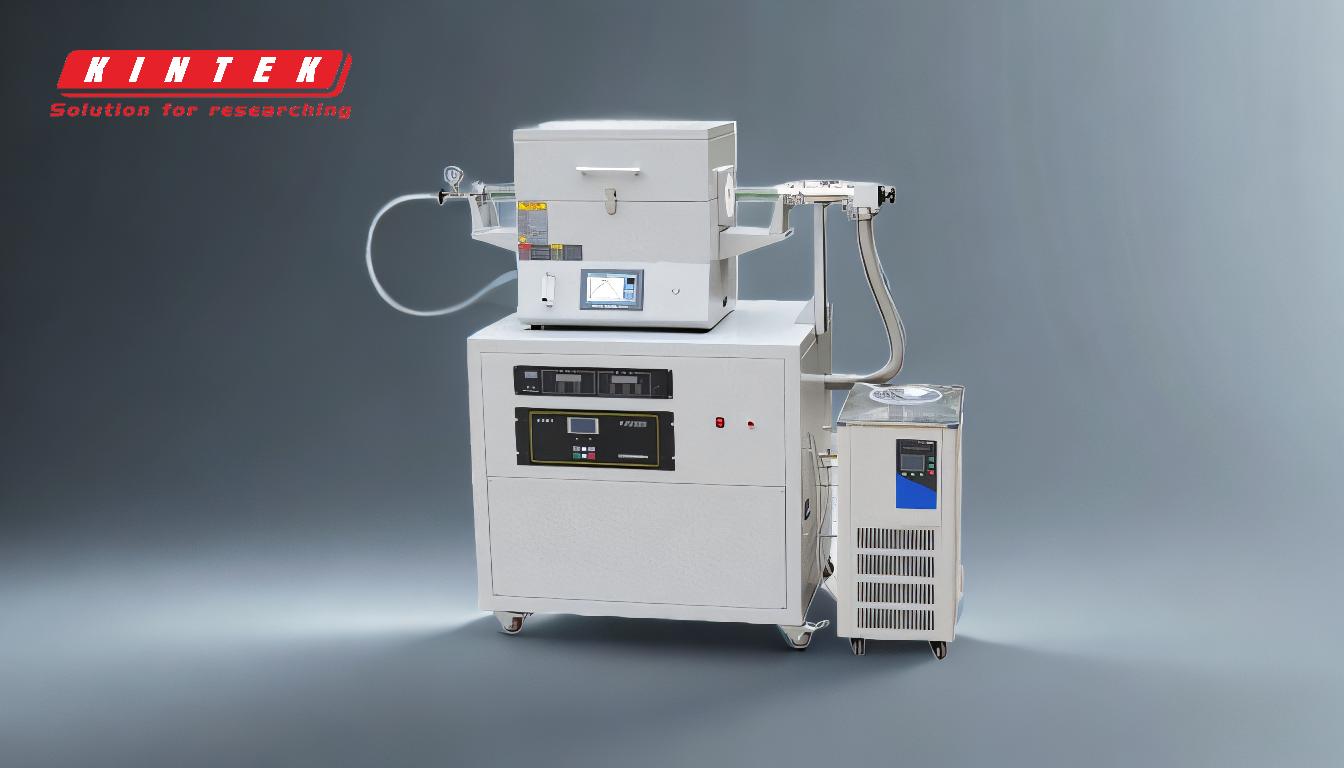
-
Definition of Air Melting:
- Air melting refers to the process of heating metals or alloys to their melting point in an open-air environment or in equipment that allows exposure to atmospheric oxygen. This method is distinct from vacuum melting or inert gas melting, where the molten metal is protected from oxidation and contamination.
-
Applications of Air Melting:
- Air melting is commonly used in industries such as foundries, steel production, and metal casting. It is suitable for producing a wide range of metal products, including:
- Castings for automotive and aerospace components.
- Ingots for further processing.
- Structural steel and other construction materials.
- Air melting is commonly used in industries such as foundries, steel production, and metal casting. It is suitable for producing a wide range of metal products, including:
-
Advantages of Air Melting:
- Cost-Effectiveness: Air melting is generally more affordable than vacuum or controlled atmosphere melting because it does not require expensive equipment or gases.
- Simplicity: The process is straightforward and does not involve complex setups, making it accessible for many manufacturers.
- Scalability: Air melting can handle large volumes of metal, making it ideal for mass production.
-
Challenges of Air Melting:
- Oxidation: Exposure to air can lead to the formation of oxides on the surface of the molten metal, which can affect the quality and properties of the final product.
- Impurities: Airborne contaminants, such as dust and moisture, can introduce impurities into the molten metal.
- Limited Material Suitability: Some metals and alloys, particularly those prone to oxidation or requiring high purity, are not suitable for air melting.
-
Equipment Used in Air Melting:
- Air melting is typically performed using furnaces such as:
- Induction furnaces.
- Arc furnaces.
- Crucible furnaces.
- These furnaces are designed to withstand high temperatures and provide the necessary heat to melt the metal.
- Air melting is typically performed using furnaces such as:
-
Comparison with Other Melting Methods:
- Vacuum Melting: This method involves melting metal in a vacuum to prevent oxidation and contamination. It is used for high-purity applications but is more expensive and complex.
- Inert Gas Melting: In this process, an inert gas (e.g., argon or nitrogen) is used to create a protective atmosphere around the molten metal. It reduces oxidation but adds to the cost.
- Air melting is less controlled but more economical for many industrial applications.
-
Impact on Metal Properties:
- The exposure to air during melting can affect the mechanical and chemical properties of the metal. For example:
- Oxidation can lead to the formation of scale or slag, which may need to be removed.
- Impurities can reduce the strength and durability of the final product.
- Proper post-melting treatments, such as degassing or refining, are often required to improve metal quality.
- The exposure to air during melting can affect the mechanical and chemical properties of the metal. For example:
-
Environmental Considerations:
- Air melting can produce emissions, such as particulate matter and gases, which may require filtration or other pollution control measures to comply with environmental regulations.
By understanding these key points, manufacturers and purchasers can make informed decisions about whether air melting is the right process for their specific needs, balancing cost, quality, and production requirements.
Summary Table:
Aspect | Details |
---|---|
Definition | Melting metals/alloys in open air or equipment exposed to atmospheric oxygen. |
Applications | Foundries, steel production, metal casting (e.g., automotive, aerospace). |
Advantages | Cost-effective, simple, scalable for mass production. |
Challenges | Oxidation, impurities, limited suitability for oxidation-prone metals. |
Equipment | Induction, arc, and crucible furnaces. |
Comparison | Less controlled than vacuum or inert gas melting but more economical. |
Impact on Metal | Oxidation and impurities may affect mechanical/chemical properties. |
Environmental Impact | Emissions may require pollution control measures. |
Need help choosing the right melting process for your needs? Contact our experts today!