A continuous furnace is an industrial furnace designed for high-volume production, where materials or workpieces are transported through the heating chamber at a constant speed or in a step-by-step manner. These furnaces are ideal for processes like heat treatment, drying, curing, and reheating semi-finished products. They operate using conveyor belts, rollers, or other mechanisms to ensure a continuous flow of materials, making them highly efficient for mass production. Examples of continuous furnaces include push rod furnaces, rotary hearth furnaces, and continuous controllable atmosphere carburizing production lines, which are used for processes such as bright quenching, tempering, carburizing, and carbonitriding.
Key Points Explained:
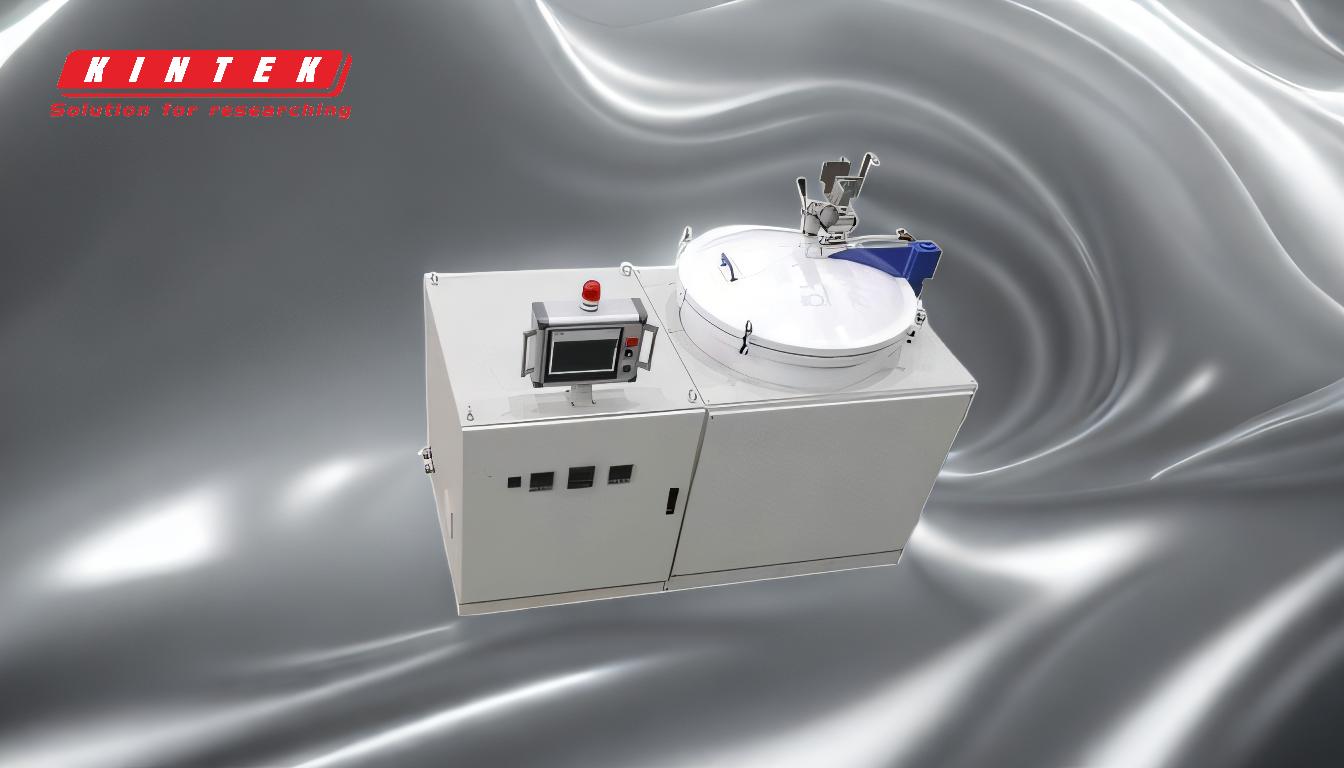
-
Definition of a Continuous Furnace:
- A continuous furnace is an industrial furnace that uses a conveyor or belt system to transport materials or workpieces through the heating chamber.
- It is designed for rapid thermal processing, making it suitable for high-volume production.
- The furnace ensures a continuous and uninterrupted flow of materials, which is ideal for processes like heat treatment, drying, and curing.
-
How Continuous Furnaces Operate:
- Materials or workpieces are transported through the furnace at a constant speed or in a step-by-step manner.
- The furnace is designed to heat the materials simultaneously as they move through the heating chamber.
- This continuous flow allows for consistent and uniform heat treatment, ensuring high-quality results.
-
Types of Continuous Furnaces:
- Push Rod Furnaces: These furnaces use a push rod mechanism to move workpieces through the heating chamber. They are commonly used for processes like bright quenching and tempering.
- Rotary Hearth Furnaces: In these furnaces, the workpieces are placed on a rotating hearth, which moves them through the heating chamber. This type is suitable for processes like carburizing and carbonitriding.
- Continuous Controllable Atmosphere Carburizing Production Lines: These furnaces are designed for mass production and can perform complex heat treatment processes in a controlled atmosphere.
-
Applications of Continuous Furnaces:
- Heat Treatment: Continuous furnaces are widely used for heat treatment processes such as quenching, tempering, carburizing, and carbonitriding. These processes are essential for improving the mechanical properties of metals.
- Drying and Curing: These furnaces are also used for drying and curing products, especially in industries that require rapid thermal processing.
- Reheating Semi-Finished Products: Continuous furnaces are used to reheat semi-finished products before they undergo further processing, such as hot forming.
-
Advantages of Continuous Furnaces:
- High Efficiency: Continuous furnaces are designed for high-volume production, making them highly efficient for large-scale manufacturing.
- Consistent Quality: The continuous flow of materials ensures uniform heat treatment, resulting in consistent product quality.
- Versatility: These furnaces can be used for a wide range of processes, including heat treatment, drying, and curing.
- Controlled Atmosphere: Some continuous furnaces, like the continuous controllable atmosphere carburizing production lines, allow for precise control of the furnace atmosphere, which is crucial for certain heat treatment processes.
-
Considerations for Purchasing a Continuous Furnace:
- Production Volume: Continuous furnaces are ideal for high-volume production. If your production volume is low, a batch furnace might be more suitable.
- Process Requirements: Consider the specific heat treatment processes you need. Different types of continuous furnaces are designed for different processes.
- Furnace Atmosphere: If your process requires a controlled atmosphere, look for furnaces that offer this feature.
- Maintenance and Operation: Continuous furnaces require regular maintenance to ensure smooth operation. Consider the ease of maintenance and the availability of spare parts when making your purchase.
In summary, continuous furnaces are essential for industries that require high-volume production and consistent heat treatment processes. They offer numerous advantages, including high efficiency, consistent quality, and versatility, making them a valuable investment for many manufacturing operations.
Summary Table:
Aspect | Details |
---|---|
Definition | Industrial furnace for high-volume production with continuous material flow |
Operation | Uses conveyor belts, rollers, or mechanisms for constant material movement |
Types | Push rod furnaces, rotary hearth furnaces, controlled atmosphere lines |
Applications | Heat treatment, drying, curing, reheating semi-finished products |
Advantages | High efficiency, consistent quality, versatility, controlled atmosphere |
Considerations | Production volume, process requirements, furnace atmosphere, maintenance |
Ready to optimize your production process? Contact us today to find the perfect continuous furnace for your needs!