Physical vapor deposition (PVD) is a vacuum-based process used to deposit thin films of materials onto substrates. It involves purely physical methods, such as evaporation or sputtering, to transfer material from a solid target to a substrate. Examples of PVD techniques include thermal evaporation, sputtering, cathodic arc deposition, and pulsed laser deposition. These techniques are widely used in industries like microelectronics, optics, and solar-cell production due to their ability to create high-purity, uniform thin films.
Key Points Explained:
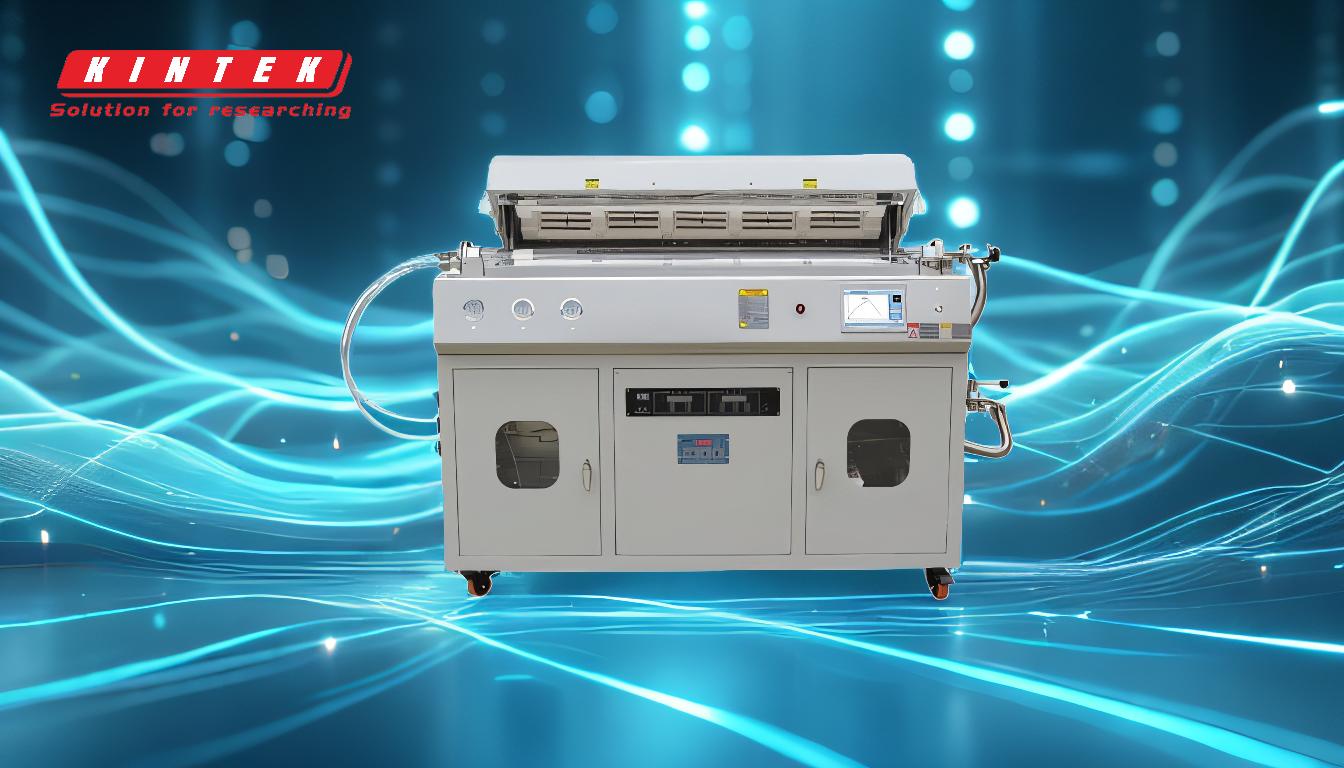
-
Definition of Physical Vapor Deposition (PVD):
- PVD is a process that occurs in a vacuum environment, where a solid target material is transformed into a vapor state and then deposited onto a substrate to form a thin film. This process relies on physical methods rather than chemical reactions, making it suitable for creating high-purity coatings.
-
Examples of PVD Techniques:
- Thermal Evaporation: A technique where the target material is heated until it evaporates and then condenses onto the substrate. This method is commonly used for depositing metals and simple compounds.
- Sputtering: Involves bombarding the target material with high-energy ions, causing atoms to be ejected and deposited onto the substrate. Sputtering is widely used in microelectronics and optics due to its ability to produce uniform and high-quality films.
- Cathodic Arc Deposition: Uses an electric arc to vaporize material from a cathode target. This technique is known for its high deposition rates and is often used for hard coatings and wear-resistant layers.
- Pulsed Laser Deposition (PLD): A method where a high-power laser pulse is used to ablate material from a target, creating a vapor that deposits onto the substrate. PLD is particularly useful for depositing complex materials like oxides and superconductors.
-
Applications of PVD:
- Microelectronics: PVD is used to deposit thin films of metals and dielectrics in semiconductor devices.
- Optics: PVD techniques are employed to create anti-reflective coatings, mirrors, and optical filters.
- Solar-Cell Production: PVD is used to deposit thin layers of materials like silicon and cadmium telluride in photovoltaic cells.
- Material Research: PVD is utilized to study the properties of thin films and develop new materials with specific characteristics.
-
Advantages of PVD:
- High Purity: PVD processes occur in a vacuum, minimizing contamination and resulting in high-purity films.
- Uniformity: PVD techniques can produce highly uniform thin films with precise thickness control.
- Versatility: PVD can deposit a wide range of materials, including metals, ceramics, and polymers, onto various substrates.
- Environmental Friendliness: PVD is a clean process that generates minimal waste compared to chemical vapor deposition (CVD).
-
Comparison with Chemical Vapor Deposition (CVD):
- Unlike PVD, CVD involves chemical reactions to deposit materials onto a substrate. While CVD can produce thicker films and is better suited for certain applications, PVD is preferred for creating high-purity, thin films with precise control over composition and structure.
By understanding these key points, equipment and consumable purchasers can make informed decisions about the most suitable PVD techniques and materials for their specific applications.
Summary Table:
PVD Technique | Description | Applications |
---|---|---|
Thermal Evaporation | Heats target material until it evaporates and condenses onto a substrate. | Metal and compound deposition. |
Sputtering | Bombards target with ions to eject atoms for deposition. | Microelectronics, optics. |
Cathodic Arc Deposition | Uses an electric arc to vaporize material from a cathode target. | Hard coatings, wear-resistant layers. |
Pulsed Laser Deposition | Ablates target material with a laser pulse for vapor deposition. | Complex materials like oxides, superconductors. |
Need help choosing the right PVD technique for your application? Contact our experts today!