Cold isostatic pressing (CIP) is a manufacturing process used to compact powdered materials into a solid form by applying uniform pressure from all directions. This method is particularly useful for materials that are difficult to press using conventional methods, such as hard metals. CIP is advantageous for producing parts with complex shapes or large sizes, where the high cost of pressing dies cannot be justified. The process involves placing the powder in an elastomeric mold, submerging it in a fluid, and applying high pressure to achieve uniform density and strength. This technology enhances product performance, quality, and economic benefits, making it a preferred choice in various industries.
Key Points Explained:
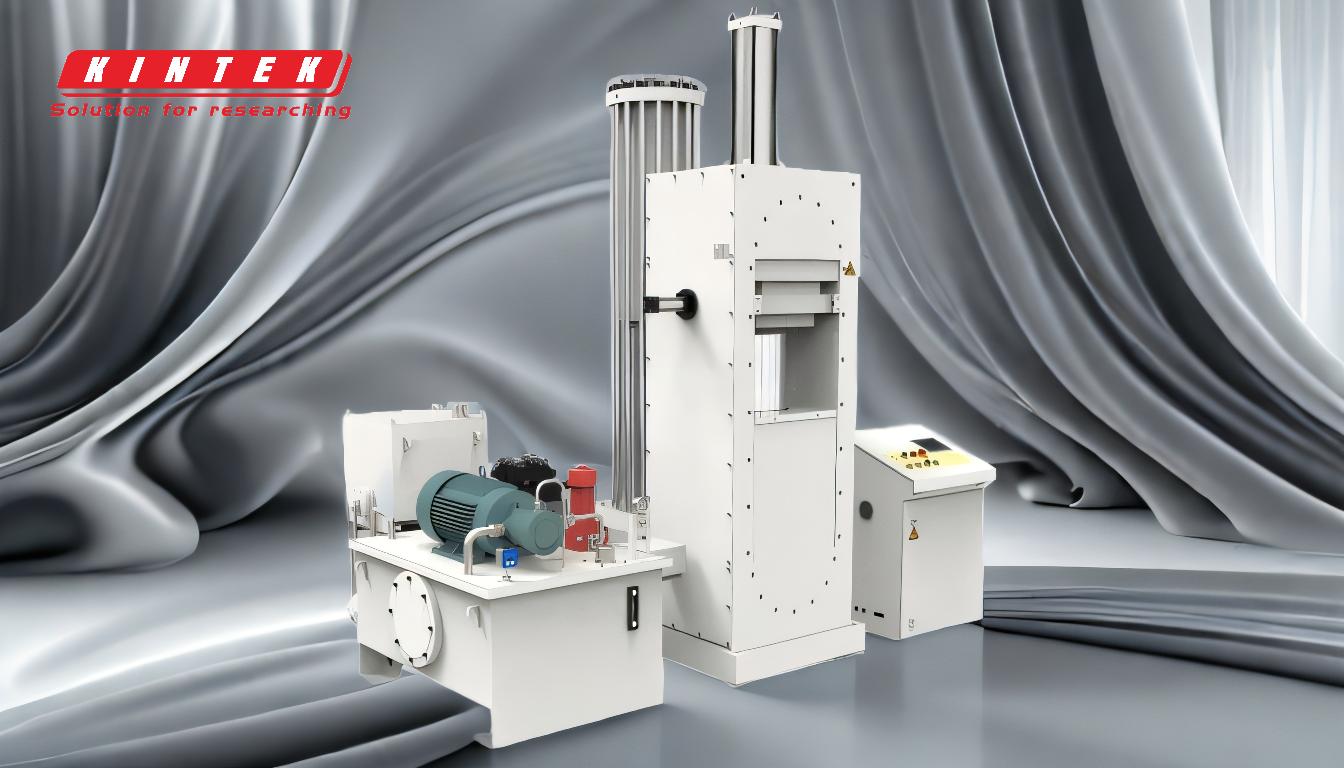
-
Process of Cold Isostatic Pressing:
- Cold isostatic pressing involves compacting powder in an elastomeric container submerged in a fluid at pressures ranging from 20 to 400 MPa.
- The powder is encased in an elastomer mold, which is then placed into a pressure chamber filled with a room-temperature liquid, usually water with a corrosion inhibitor.
- Pressure is applied uniformly from all sides to condense the metal powder, resulting in a solid green body with uniform density.
-
Applications of Cold Isostatic Pressing:
- CIP is used for powders that are difficult to press, such as hard metals, and allows the production of simple-shaped small or large powder compacts with uniform green density.
- It is also used for blending or preparing powders for subsequent processing, such as sintering.
- CIP is advantageous for producing parts where the high initial cost of pressing dies cannot be justified or when very large or complex compacts are needed.
-
Advantages of Cold Isostatic Pressing:
- Uniform Density and Strength: CIP ensures that the compacted powder has uniform density and strength throughout the part.
- Versatility: It can be used for a wide range of materials and complex shapes.
- Corrosion Resistance: The process can enhance the corrosion resistance of the final product.
- Improved Mechanical Properties: CIP improves the mechanical properties of the compacted material.
- Use in Powder Metallurgy: It is widely used in powder metallurgy for the production of refractory metals and other materials.
- Preparation for Sintering: CIP prepares powders for subsequent sintering processes, ensuring better final product quality.
-
Comparison with Hot Isostatic Pressing (HIP):
- The main types of isostatic pressing are Hot Isostatic Pressing (HIP) and Cold Isostatic Pressing (CIP).
- While HIP involves applying heat along with pressure to achieve densification, CIP operates at room temperature, making it suitable for materials that cannot withstand high temperatures.
-
Economic and Quality Benefits:
- Cold isostatic pressing technology can improve product performance, enhance product quality, and increase economic benefits.
- It offers many advantages over other molding processes, leading to its expanding application fields and increasing technological maturity.
In summary, cold isostatic pressing is a versatile and efficient method for compacting powdered materials, offering numerous advantages in terms of product quality, performance, and economic benefits. Its ability to produce parts with uniform density and complex shapes makes it an essential process in various industries, particularly in powder metallurgy and the production of refractory metals.
Summary Table:
Aspect | Details |
---|---|
Process | Compacts powder in an elastomeric mold submerged in fluid at 20-400 MPa. |
Applications | Used for hard metals, complex shapes, and large compacts. |
Advantages | Uniform density, corrosion resistance, improved mechanical properties. |
Comparison with HIP | Operates at room temperature, unlike HIP which uses heat. |
Economic Benefits | Enhances product performance, quality, and cost-efficiency. |
Interested in how cold isostatic pressing can benefit your manufacturing process? Contact us today to learn more!