An inert atmosphere for annealing refers to a controlled environment where reactive gases like oxygen are replaced with non-reactive (inert) gases such as nitrogen or argon. This environment prevents oxidation, decarburization, and contamination of the metal surface during the annealing process, ensuring high-quality results. Inert atmospheres are particularly crucial for annealing stainless steels and non-ferrous metals, as they protect the material from chemical reactions that could compromise its properties. The use of high-purity inert gases (e.g., 99.99% purity) and precise control systems in furnaces further enhances the effectiveness of the annealing process.
Key Points Explained:
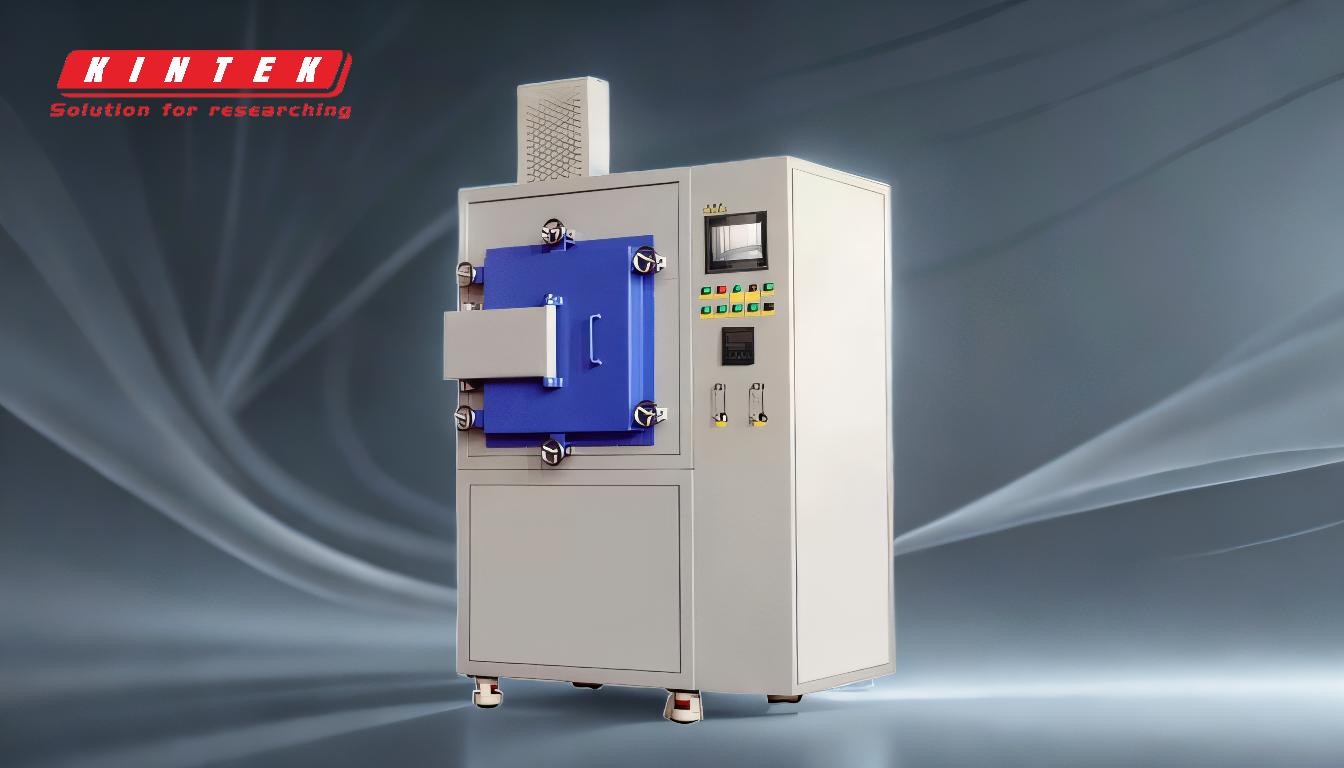
-
Definition of an Inert Atmosphere:
- An inert atmosphere is a controlled environment where reactive gases (e.g., oxygen) are replaced with non-reactive gases like nitrogen or argon.
- This environment is designed to prevent unwanted chemical reactions, such as oxidation or decarburization, during heat treatment processes like annealing.
-
Purpose of Using an Inert Atmosphere in Annealing:
- Preventing Oxidation: Oxidation occurs when metals react with oxygen, leading to scale formation on the surface. An inert atmosphere eliminates oxygen, preventing this reaction.
- Avoiding Decarburization: Decarburization is the loss of carbon from the surface of steel, which can weaken the material. Inert gases prevent this by creating a non-reactive environment.
- Reducing Contamination: Inert atmospheres minimize the risk of contamination from impurities, ensuring the metal retains its desired properties.
- Enhancing Reproducibility: By maintaining a consistent environment, inert atmospheres ensure reliable and repeatable annealing results.
-
Types of Inert Gases Used:
- Nitrogen: The most commonly used inert gas due to its cost-effectiveness and non-reactive nature with steel. It is widely available and provides excellent protection against oxidation.
- Argon: Another popular choice, especially for applications requiring higher purity or when nitrogen might react with certain materials. Argon is denser than nitrogen, providing better protection in some cases.
- Hydrogen: Occasionally used in combination with argon for specific applications, such as annealing stainless steels, to enhance surface cleanliness and reduce oxide formation.
-
Applications of Inert Atmospheres in Annealing:
- Stainless Steels: Inert atmospheres are essential for annealing stainless steels to prevent chromium oxide formation, which can degrade corrosion resistance.
- Non-Ferrous Metals: Metals like copper, aluminum, and titanium benefit from inert atmospheres to avoid oxidation and maintain surface quality.
- Specialized Heat Treatments: Inert atmospheres are used in processes like bonding, curing, and heat-treating to ensure precise control over material properties.
-
Equipment and Control Systems:
- Inert Gas Atmosphere Furnaces: These furnaces are designed with precision microprocessor-based temperature controls and energy-efficient insulation to maintain consistent conditions.
- High-Purity Gases: Inert gases with a purity of more than 99.99% are used to ensure minimal contamination and optimal performance.
- Pressure Control: The pressure of the inert gas is typically maintained within a specific range (e.g., 0.05 to 0.07 MPa) to achieve the desired protective environment.
-
Benefits of Using an Inert Atmosphere:
- Improved Surface Quality: Prevents scale formation and maintains a clean, oxide-free surface.
- Enhanced Material Properties: Retains carbon content and other critical elements, ensuring the material's strength and durability.
- Safety: Reduces the risk of fire and explosions by eliminating reactive gases.
- Cost Savings: Energy-efficient furnaces and precise control systems optimize resource usage, reducing operational costs.
-
Challenges and Considerations:
- Cost of Inert Gases: High-purity gases like argon can be expensive, impacting the overall cost of the annealing process.
- Equipment Maintenance: Inert gas atmosphere furnaces require regular maintenance to ensure consistent performance and prevent leaks.
- Material Compatibility: Not all materials require inert atmospheres, so it's essential to evaluate the specific needs of the material being annealed.
By understanding these key points, equipment and consumable purchasers can make informed decisions about implementing inert atmospheres in their annealing processes, ensuring high-quality results and cost-effective operations.
Summary Table:
Aspect | Details |
---|---|
Definition | Controlled environment with non-reactive gases (e.g., nitrogen, argon). |
Purpose | Prevents oxidation, decarburization, contamination, and ensures reproducibility. |
Inert Gases Used | Nitrogen (cost-effective), Argon (high-purity), Hydrogen (specialized). |
Applications | Stainless steels, non-ferrous metals, specialized heat treatments. |
Equipment | Inert gas furnaces with precision controls and high-purity gases. |
Benefits | Improved surface quality, enhanced material properties, safety, cost savings. |
Challenges | Cost of inert gases, equipment maintenance, material compatibility. |
Need help setting up an inert atmosphere for annealing? Contact our experts today for tailored solutions!