Atomic Layer Deposition (ALD) of metals is a highly precise thin-film deposition technique that enables the creation of uniform, conformal, and pinhole-free metal layers at the atomic scale. It is a specialized form of Chemical Vapor Deposition (CVD) that relies on sequential, self-limiting chemical reactions between gas-phase precursors and the substrate surface. ALD alternates between two or more precursor gases, separated by purge steps, to ensure controlled layer-by-layer growth. This method is particularly advantageous for depositing metals on complex geometries, high-aspect-ratio structures, and nanoscale devices, offering exceptional thickness control, uniformity, and conformality. ALD is widely used in industries such as semiconductors, medical devices, and advanced coatings due to its ability to produce high-quality, ultra-thin metal films with atomic precision.
Key Points Explained:
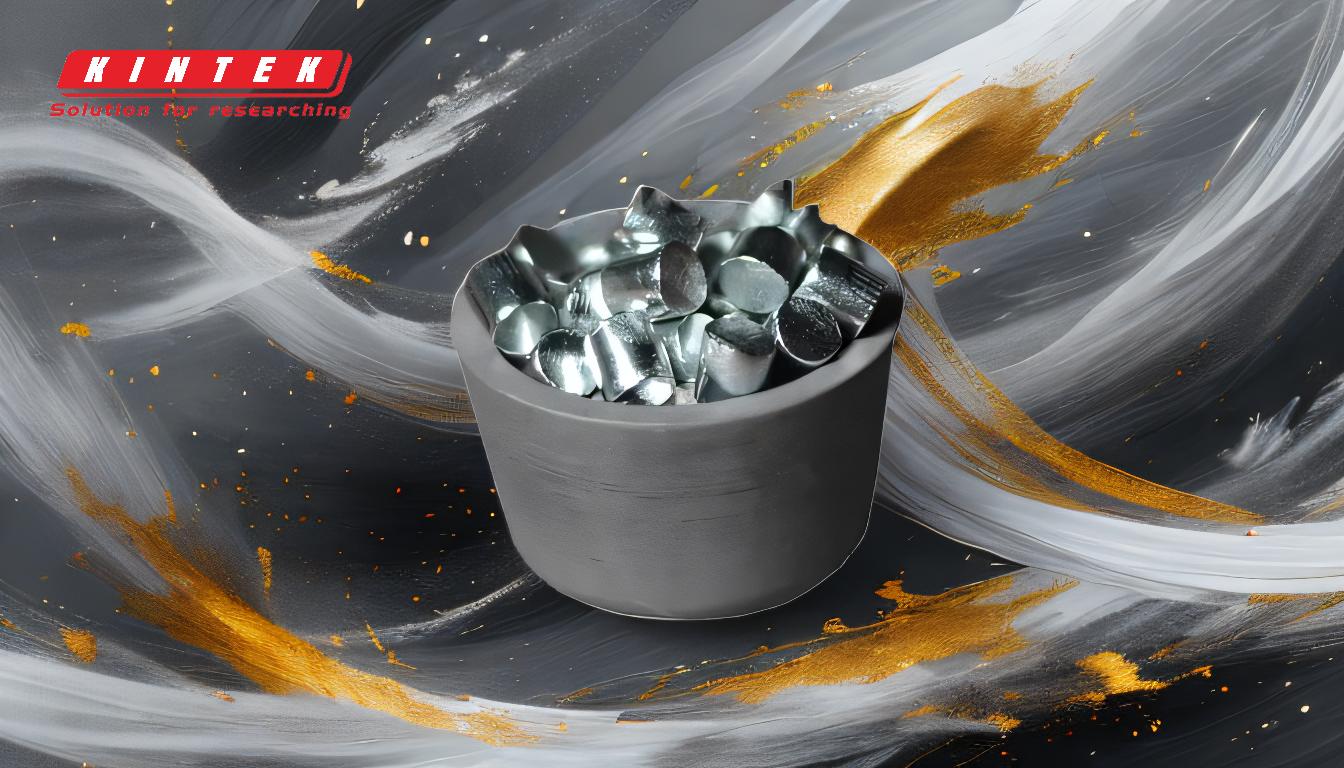
-
Definition and Process of ALD for Metals:
- ALD is a surface-controlled, sequential deposition technique that builds thin films one atomic layer at a time.
- It involves alternating exposures of a substrate to two or more gas-phase precursors, separated by purge steps to remove excess reactants and by-products.
- The process is self-limiting, meaning each reaction cycle deposits a single atomic layer, ensuring precise thickness control.
-
Key Characteristics of ALD for Metals:
- Conformality: ALD provides excellent step coverage, even on high-aspect-ratio structures (up to 2000:1), making it ideal for complex geometries.
- Uniformity: Films are highly uniform across the substrate, with thickness variations controlled at the atomic level.
- Pinhole-Free Layers: The self-limiting nature of ALD reactions ensures dense, defect-free films.
- Thickness Control: ALD can deposit ultra-thin layers (less than 10 nm) with atomic precision, enabling nanoscale applications.
-
Applications of ALD for Metals:
- Semiconductors: ALD is used to deposit metal layers for transistors, interconnects, and memory devices, where precision and uniformity are critical.
- Medical Devices: ALD coatings are applied to implants and instruments with complex shapes, providing biocompatibility and corrosion resistance.
- Advanced Coatings: ALD is used for protective and functional coatings in optics, energy storage, and catalysis, where conformality and thickness control are essential.
-
Advantages Over Traditional Deposition Techniques:
- Versatility: Unlike physical vapor deposition (PVD) or traditional CVD, ALD does not require line-of-sight or constant exposure, making it suitable for intricate structures.
- Repeatability: The self-limiting nature of ALD ensures consistent film properties across multiple deposition cycles.
- Scalability: ALD can be scaled for industrial applications, including batch processing and roll-to-roll manufacturing.
-
Challenges and Considerations:
- Precursor Selection: Choosing appropriate metal precursors is critical, as they must be volatile, reactive, and thermally stable.
- Deposition Rate: ALD is a slower process compared to other techniques, which may limit its use in high-throughput applications.
- Cost: The specialized equipment and high-purity precursors can make ALD more expensive than traditional methods.
-
Future Trends in ALD for Metals:
- New Materials: Research is ongoing to develop ALD processes for emerging materials, such as 2D metals and alloys.
- Hybrid Techniques: Combining ALD with other deposition methods (e.g., plasma-enhanced ALD) to improve deposition rates and material properties.
- Sustainability: Developing eco-friendly precursors and reducing energy consumption in ALD processes.
In summary, ALD of metals is a cutting-edge technology that offers unparalleled control over film thickness, uniformity, and conformality. Its ability to deposit high-quality metal layers on complex structures makes it indispensable in modern industries, from microelectronics to medical devices. While challenges such as cost and deposition rate remain, ongoing advancements are expanding its applications and efficiency.
Summary Table:
Aspect | Details |
---|---|
Process | Sequential, self-limiting reactions with gas-phase precursors. |
Key Characteristics | Conformality, uniformity, pinhole-free layers, and atomic-level thickness control. |
Applications | Semiconductors, medical devices, advanced coatings. |
Advantages | Versatility, repeatability, scalability for complex geometries. |
Challenges | Precursor selection, slower deposition rate, higher cost. |
Future Trends | New materials, hybrid techniques, sustainability improvements. |
Unlock the potential of ALD for your industry—contact our experts today to learn more!