Brazing is a versatile joining process primarily used to create strong, leak-proof, and durable bonds between metal components. It is widely employed across various industries, including automotive, aerospace, electronics, HVAC, and medical devices, due to its ability to join dissimilar metals, work with complex geometries, and handle thin or thick cross-sections. Brazing is particularly suited for applications requiring precision, such as heat exchangers, hydraulic fittings, and structural components, as well as assemblies with restricted access or multiple joints. Its adaptability makes it a preferred method for manufacturing components in high-performance and high-reliability environments.
Key Points Explained:
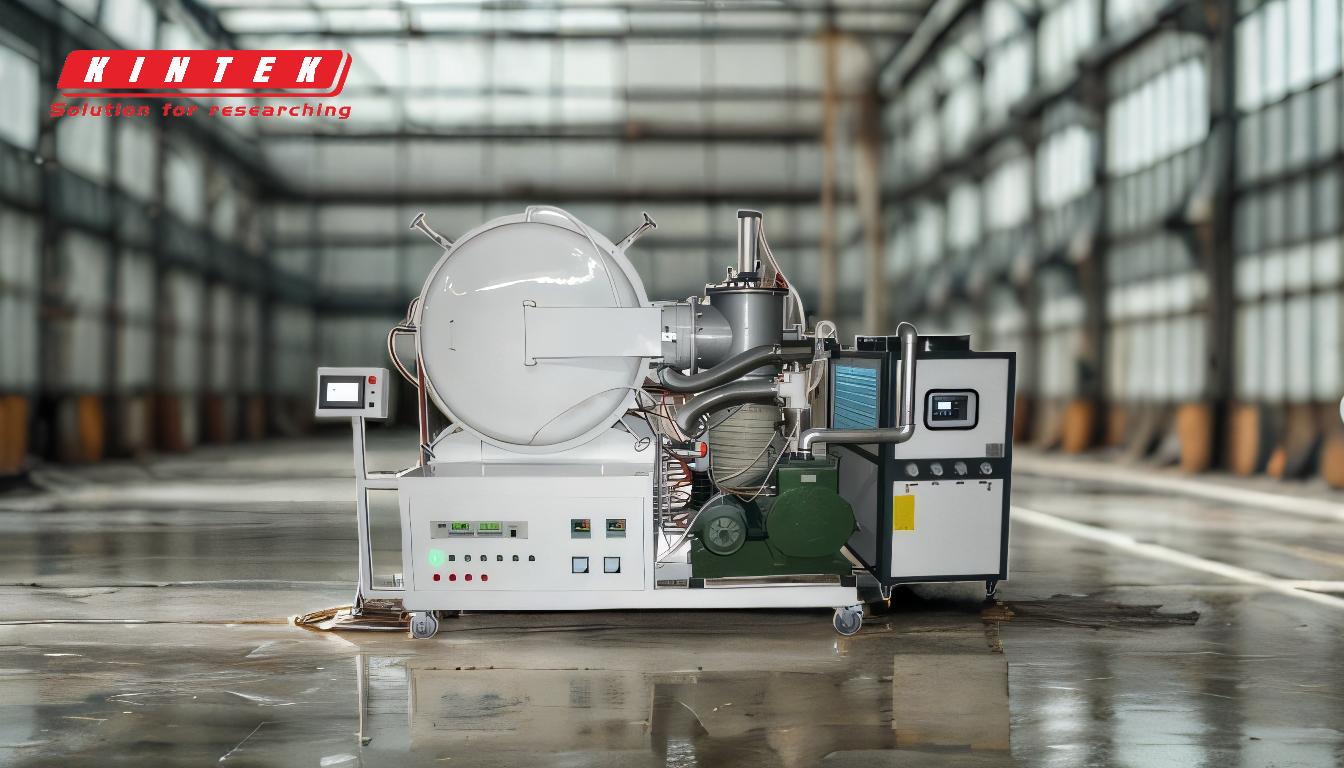
-
Industries and Applications:
- Brazing is extensively used in industries such as automotive, aerospace, electronics, HVAC, and medical devices.
- Common applications include:
- Automotive: Engine components, hydraulic fittings, and structural parts.
- Aerospace: Aircraft components, space applications, and industrial gas turbine parts.
- Electronics: Sensors, electromechanical components, and electronic devices.
- HVAC: Heating and cooling assemblies, micro-channel heat exchangers, and pipe fittings.
- Medical Devices: Precision instruments and scientific equipment.
-
Joining Dissimilar Metals:
- Brazing is ideal for joining dissimilar metals, such as copper to steel or aluminum to stainless steel, which is often challenging with other welding methods.
- This capability is crucial in applications like heat exchangers, where different materials are used to optimize thermal conductivity and corrosion resistance.
-
Complex Geometries and Restricted Access:
- Brazing is well-suited for components with complex shapes or joints located below the surface or in hard-to-reach areas.
- Examples include:
- Tube manipulations in heat exchangers.
- Assemblies with a large number of joints, such as automotive engine components.
-
Thin or Thick Cross-Sections:
- Brazing can handle both thin and thick cross-sections, making it versatile for a wide range of applications.
- Thin cross-sections are common in electronics and medical devices, while thick cross-sections are found in structural components and industrial machinery.
-
High-Performance and High-Reliability Applications:
- Brazing is preferred for applications requiring high strength, leak-proof seals, and durability under extreme conditions.
- Examples include:
- Nuclear components and offshore petrochemical equipment.
- Aerospace and space applications, where reliability is critical.
-
Advantages Over Other Joining Methods:
- Brazing offers several advantages, including:
- Lower heat input compared to welding, reducing the risk of distortion or damage to components.
- Ability to join dissimilar metals without compromising their properties.
- Production of clean, precise joints with minimal post-processing required.
- Brazing offers several advantages, including:
-
Furnace Brazing:
- Furnace brazing is a specialized form of brazing used for high-volume production and complex assemblies.
- Applications include:
- Automotive components like engine parts and hydraulic fittings.
- Aerospace and industrial gas turbine components.
- Medical and scientific equipment requiring high precision.
-
Common Brazed Components:
- Examples of components commonly joined using brazing include:
- Metal housings and electromechanical components.
- Pipe fittings and HVAC system parts.
- Structural components in engineering and construction.
- Examples of components commonly joined using brazing include:
By leveraging its unique capabilities, brazing plays a critical role in modern manufacturing, enabling the production of high-quality, reliable, and efficient components across a wide range of industries.
Summary Table:
Key Aspect | Details |
---|---|
Industries | Automotive, aerospace, electronics, HVAC, medical devices |
Applications | Engine components, heat exchangers, sensors, precision instruments |
Joining Dissimilar Metals | Copper to steel, aluminum to stainless steel |
Complex Geometries | Tube manipulations, assemblies with restricted access |
Thin/Thick Cross-Sections | Suitable for electronics, medical devices, and structural components |
High-Reliability Uses | Aerospace, nuclear components, offshore petrochemical equipment |
Advantages | Lower heat input, clean joints, minimal post-processing |
Furnace Brazing | High-volume production, automotive, aerospace, and medical applications |
Discover how brazing can enhance your manufacturing process—contact our experts today!