A burnout furnace is a specialized type of furnace used primarily in dental laboratories and manufacturing processes to remove organic materials, such as wax or plastic, from molds or ceramic frameworks before sintering. It operates at high temperatures, typically up to 1200°C, and is designed to ensure safety, efficiency, and precision. The furnace features programmable controls, fast heating capabilities, and a ceramic fiber chamber for energy efficiency. It is essential for preparing materials for the sintering process, where the final product's mechanical strength, density, and translucency are achieved. Burnout furnaces are closely related to sintering furnaces, as they prepare materials for the sintering stage.
Key Points Explained:
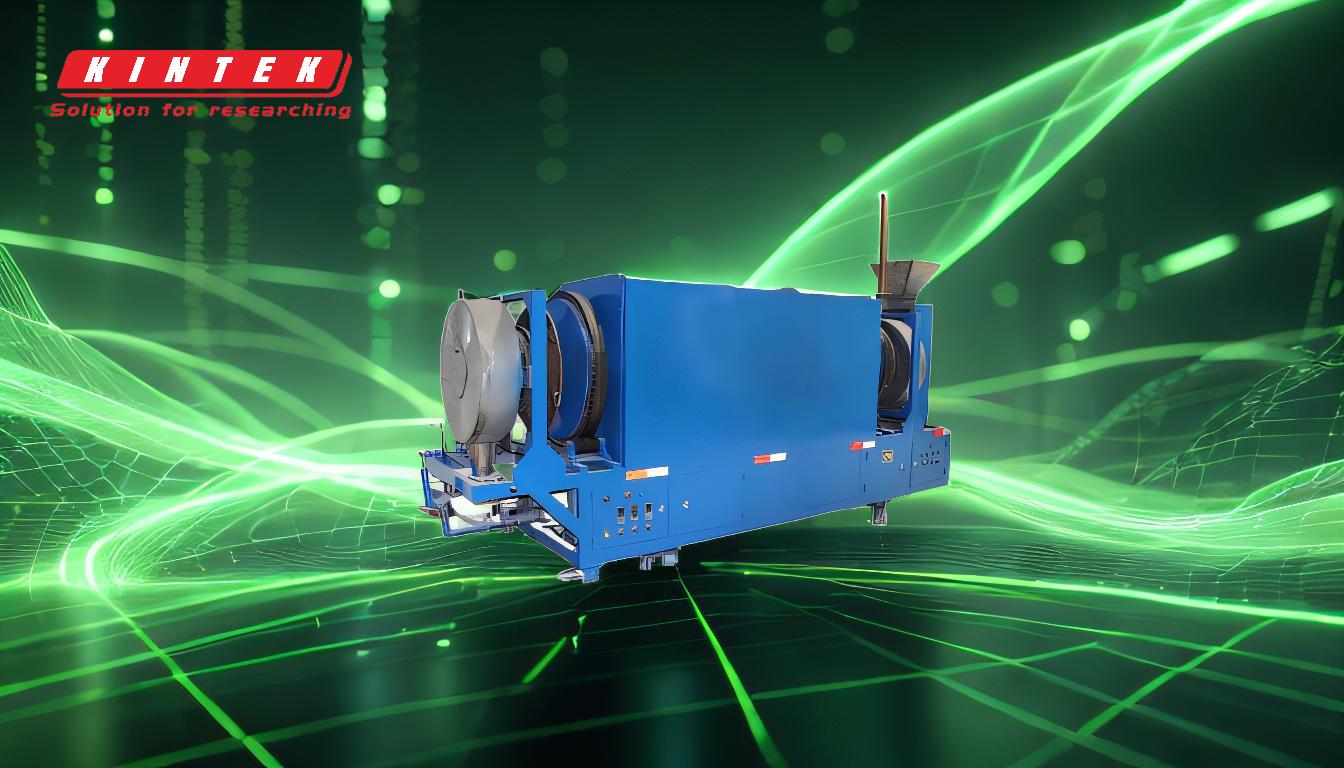
-
Purpose of a Burnout Furnace:
- A burnout furnace is used to eliminate organic materials, such as wax or plastic, from molds or ceramic frameworks. This step is crucial before sintering, as it ensures that the final product is free from impurities and achieves the desired properties like density and translucency.
-
Temperature Range and Control:
- Burnout furnaces can reach temperatures up to 1200°C, with a working range from room temperature to 1100°C. They feature programmable controls with up to 30 segments, allowing precise temperature regulation and automation. This ensures consistent results and reduces the risk of errors.
-
Design and Safety Features:
- The furnace is designed with a ceramic fiber chamber, which enables fast heating and energy efficiency. It also includes a double-layer steel casing with fan cooling to keep the surface temperature below 50°C, ensuring operator safety during use.
-
Relationship to Sintering Furnaces:
- Burnout furnaces are closely linked to sintering furnaces, as they prepare materials for the sintering process. After burnout, the materials are transferred to a sintering furnace, where they are heated to achieve the final product's mechanical strength, density, and translucency.
-
Applications in Dental Laboratories:
- In dental labs, burnout furnaces are used to process restorations like crowns, bridges, or frameworks. They remove wax or plastic patterns from ceramic molds, ensuring that the final zirconia restorations are dense and free from defects.
-
Efficiency and Maintenance:
- Modern burnout furnaces are designed for low failure rates and easy routine maintenance. Their intuitive controls and accurate displays make them user-friendly, reducing downtime and operational costs.
-
Comparison to Other Furnaces:
- Unlike vacuum sintering furnaces, which operate in a vacuum or hydrogen-protected environment, burnout furnaces focus on removing organic materials. However, both types of furnaces play critical roles in the manufacturing and dental industries, ensuring high-quality end products.
By understanding these key points, purchasers can evaluate burnout furnaces based on their specific needs, such as temperature range, safety features, and compatibility with sintering processes.
Summary Table:
Key Features | Details |
---|---|
Purpose | Removes wax or plastic from molds before sintering. |
Temperature Range | Up to 1200°C, with programmable controls for precise regulation. |
Design & Safety | Ceramic fiber chamber, double-layer steel casing, and fan cooling. |
Applications | Used in dental labs for crowns, bridges, and zirconia restorations. |
Efficiency | Fast heating, energy-efficient, and low maintenance. |
Relation to Sintering | Prepares materials for sintering furnaces to achieve final product quality. |
Discover how a burnout furnace can optimize your lab or manufacturing process—contact us today!