Carbon coatings are primarily used in electron microscopy to prepare non-conductive specimens for imaging and analysis, particularly in energy-dispersive x-ray spectroscopy (EDS). They prevent charging mechanisms that degrade material surfaces and allow for efficient imaging of biological and non-conductive samples. Additionally, carbon coatings are amorphous, conductive, and transparent to electrons, making them ideal for minimizing imaging artifacts. Beyond microscopy, carbon coatings, including graphene-based ones, have applications in anti-corrosion paints, advanced sensors, electronics, and solar panels. The process involves thermal evaporation of carbon in a vacuum system, ensuring a fine, uniform deposition on specimens.
Key Points Explained:
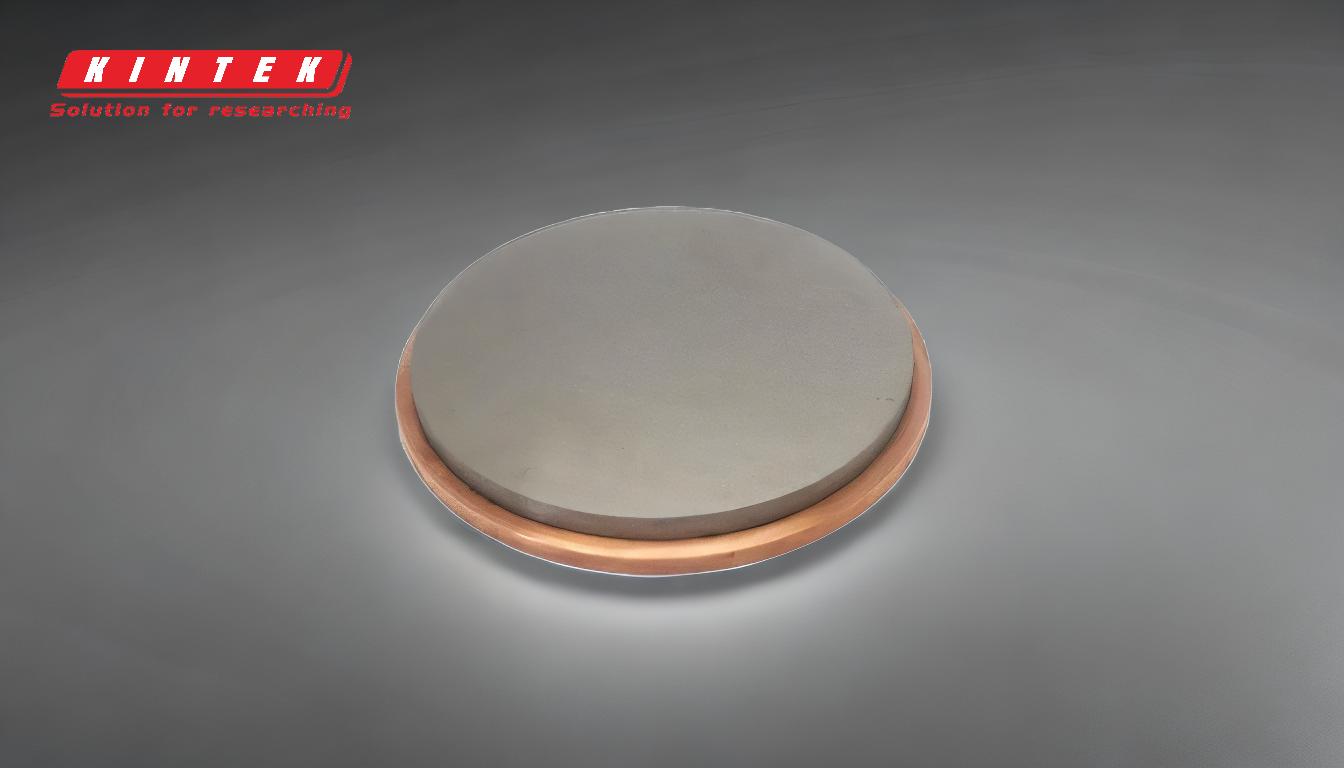
-
Applications in Electron Microscopy:
- Minimizing Imaging Interference: Carbon coatings are amorphous and transparent to electrons, which reduces interference during imaging. This property is crucial for obtaining clear and accurate images in electron microscopy.
- Preventing Charging Mechanisms: Non-conductive specimens can accumulate charge during electron microscopy, leading to surface deterioration and imaging artifacts. Carbon coatings provide conductivity, preventing these issues.
- Support for Energy-Dispersive X-ray Spectroscopy (EDS): Carbon coatings are essential for preparing non-conductive specimens for EDS analysis, as they ensure efficient electron flow and accurate spectroscopic data.
-
Technique of Carbon Coating:
- Thermal Evaporation Process: Carbon coating is achieved through thermal evaporation, where a carbon source (e.g., thread or rod) is heated to its evaporation temperature in a vacuum system. This deposits a fine, uniform layer of carbon onto specimens.
- Use in TEM Grids: Carbon coatings are commonly used to create specimen support films on transmission electron microscopy (TEM) grids, providing a stable and conductive surface for imaging.
-
Mechanisms and Benefits of Carbon Coating:
- Surface Chemical Stability: Carbon coatings modify the surface chemistry of materials, enhancing their stability and resistance to degradation.
- Structural Stability: The coating improves the structural integrity of specimens, making them more durable during imaging and analysis.
- Improved Li-ion Diffusion: In applications like battery technology, carbon coatings enhance the diffusion of lithium ions, improving performance.
-
Beyond Microscopy: Advanced Applications:
- Graphene-Based Coatings: Graphene, a form of carbon, is used in advanced coatings for anti-corrosion paints, sensors, electronics, and solar panels. Its unique properties enable more precise, efficient, and durable applications.
- Anti-Corrosion and Protective Layers: Carbon coatings provide protection against environmental factors, such as corrosion, extending the lifespan of materials.
- Enhanced Electronics and Sensors: The conductivity and stability of carbon coatings make them ideal for developing faster, more sophisticated electronic devices and sensors.
-
Advantages of Carbon Coatings:
- Conductivity: Carbon coatings are conductive, which is essential for preventing charge buildup in non-conductive specimens.
- Transparency to Electrons: Their transparency ensures minimal interference with electron beams, leading to clearer imaging.
- Versatility: Carbon coatings are suitable for a wide range of applications, from microscopy to industrial and technological uses.
In summary, carbon coatings are indispensable in electron microscopy for their ability to enhance imaging quality and prepare non-conductive specimens for analysis. Their applications extend to advanced technologies, including anti-corrosion coatings, sensors, and electronics, thanks to their unique properties and versatility. The thermal evaporation process ensures a precise and uniform coating, making carbon coatings a reliable solution across various fields.
Summary Table:
Key Aspect | Details |
---|---|
Applications in Microscopy | - Minimize imaging interference - Prevent charging mechanisms - Support EDS analysis |
Coating Technique | - Thermal evaporation in vacuum - Used for TEM grids |
Benefits | - Surface and structural stability - Improved Li-ion diffusion |
Advanced Applications | - Anti-corrosion paints - Sensors, electronics, solar panels |
Advantages | - Conductive - Transparent to electrons - Versatile |
Learn how carbon coatings can elevate your research and industrial applications—contact us today!