Chemical vapor deposition (CVD) is a sophisticated manufacturing process used to create thin films and coatings on substrates through chemical reactions in a vapor phase. This process is widely utilized in industries such as semiconductors, optics, and materials science due to its ability to produce high-purity, high-performance materials. The CVD process involves several key steps, including the vaporization of a volatile compound, thermal decomposition or chemical reaction of the vapor, and the deposition of the resultant material onto a substrate. The process can be tailored by adjusting parameters such as chamber pressure, substrate temperature, and the choice of target materials and deposition technologies.
Key Points Explained:
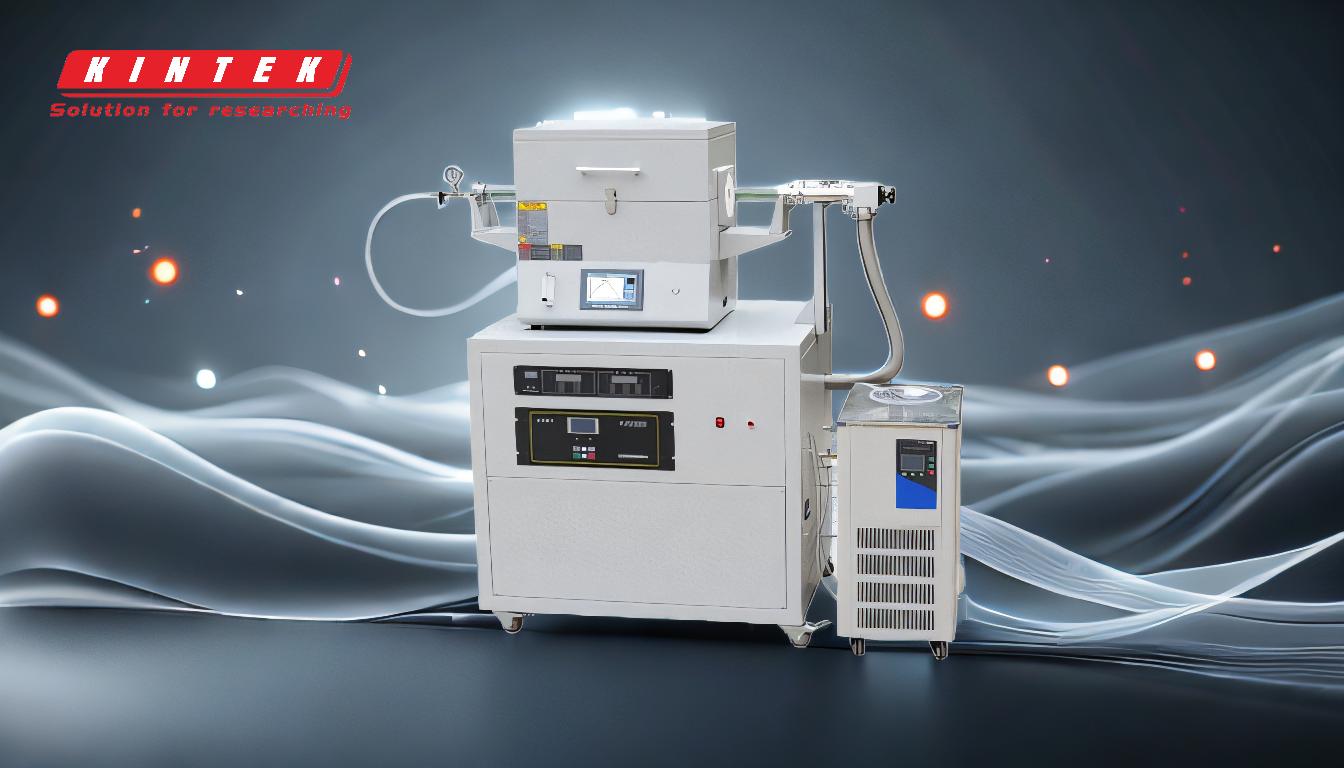
-
Overview of Chemical Vapor Deposition (CVD):
- CVD is a process where a solid material is deposited onto a substrate through chemical reactions in the vapor phase. This method is essential for creating thin films with precise thickness and composition.
- The process is widely used in industries requiring high-purity materials, such as semiconductor manufacturing, where it is used to deposit silicon, silicon dioxide, and other materials.
-
Steps Involved in CVD:
- Transport of Reacting Gaseous Species: The first step involves transporting the gaseous reactants to the substrate surface. This is typically done in a vacuum chamber to ensure controlled conditions.
- Adsorption on the Surface: Once the gaseous species reach the substrate, they adsorb onto its surface. This step is crucial for the subsequent chemical reactions.
- Surface-Catalyzed Reactions: The adsorbed species undergo chemical reactions on the substrate surface, often catalyzed by the surface itself. These reactions can include decomposition, oxidation, or reduction.
- Surface Diffusion: The reacted species diffuse across the substrate surface to find suitable growth sites.
- Nucleation and Growth: The species then nucleate and grow into a continuous film. This step determines the quality and uniformity of the deposited film.
- Desorption and Transport of By-products: Finally, any gaseous by-products desorb from the surface and are transported away from the reaction zone, ensuring the purity of the deposited film.
-
Types of CVD Processes:
- Atmospheric Pressure CVD (APCVD): Conducted at atmospheric pressure, this method is simpler but can result in less uniform films.
- Low-Pressure CVD (LPCVD): Performed under reduced pressure, LPCVD offers better film uniformity and is commonly used in semiconductor manufacturing.
- Plasma-Enhanced CVD (PECVD): Utilizes plasma to enhance the chemical reactions, allowing for lower deposition temperatures. This is particularly useful for depositing films on temperature-sensitive substrates.
- Atomic Layer Deposition (ALD): A variant of CVD that allows for atomic-level control of film thickness, resulting in extremely uniform and conformal coatings.
-
Key Parameters in CVD:
- Chamber Pressure: The pressure within the deposition chamber affects the rate and uniformity of the deposition. Lower pressures generally result in more uniform films.
- Substrate Temperature: The temperature of the substrate influences the rate of chemical reactions and the quality of the deposited film. Higher temperatures can improve film quality but may also introduce defects.
- Target Materials: The choice of target materials, which can range from metals to semiconductors, determines the properties of the deposited film. For example, silicon is commonly used in semiconductor applications, while titanium nitride is used for wear-resistant coatings.
-
Applications of CVD:
- Semiconductors: CVD is extensively used in the semiconductor industry to deposit thin films of silicon, silicon dioxide, and other materials used in integrated circuits.
- Optics: CVD is used to create optical coatings, such as anti-reflective coatings on lenses and mirrors.
- Protective Coatings: CVD is employed to deposit hard, wear-resistant coatings on tools and components, extending their lifespan.
- Nanotechnology: CVD is a key technique in the fabrication of nanostructures, such as carbon nanotubes and graphene.
-
Advantages and Challenges:
- Advantages: CVD offers high purity, excellent film uniformity, and the ability to deposit a wide range of materials. It is also highly scalable, making it suitable for both research and industrial applications.
- Challenges: The process can be complex and requires precise control of parameters. Additionally, the use of hazardous gases and high temperatures can pose safety and environmental challenges.
In summary, chemical vapor deposition is a versatile and powerful manufacturing process that plays a critical role in modern technology. By understanding the key steps, parameters, and applications of CVD, manufacturers can optimize the process to produce high-quality thin films for a wide range of applications.
Summary Table:
Aspect | Details |
---|---|
Overview | CVD deposits solid materials onto substrates through vapor-phase chemical reactions. |
Key Steps | 1. Transport of gaseous species 2. Adsorption 3. Surface reactions 4. Nucleation 5. Desorption |
Types of CVD | APCVD, LPCVD, PECVD, ALD |
Key Parameters | Chamber pressure, substrate temperature, target materials |
Applications | Semiconductors, optics, protective coatings, nanotechnology |
Advantages | High purity, film uniformity, scalability |
Challenges | Complex process, hazardous gases, high temperatures |
Discover how CVD can revolutionize your manufacturing process—contact our experts today for tailored solutions!