Chemical vapor deposition (CVD) is a cutting-edge technology used to deposit high-quality, high-performance solid materials onto substrates. It involves the use of precursor gases that undergo chemical reactions under controlled conditions of temperature, pressure, and flow rate. The process typically includes steps such as gas transport, adsorption, surface reactions, and film growth, resulting in the formation of thin films or coatings. CVD is widely used in industries such as semiconductors, optics, and coatings due to its ability to produce defect-free materials at relatively low temperatures. Recent advancements in CVD technology focus on improving precision, reducing energy consumption, and enabling the deposition of complex materials.
Key Points Explained:
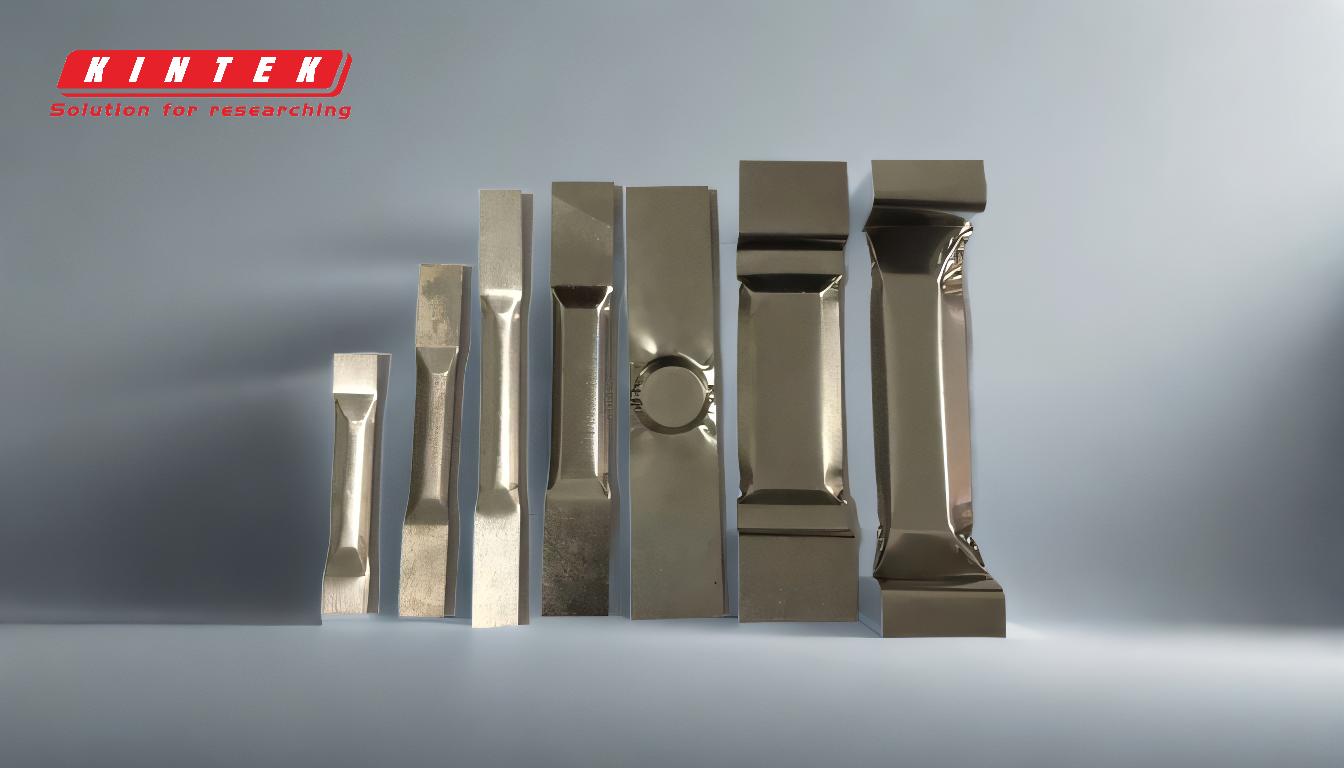
-
Fundamental Steps of CVD:
- Transport of Gaseous Species: Precursor gases are introduced into a reaction chamber and transported to the substrate surface.
- Adsorption: The gases adsorb onto the substrate surface, where they undergo chemical reactions.
- Surface Reactions: Heterogeneous reactions occur on the substrate surface, leading to the formation of solid materials.
- Film Growth: The reaction products form a thin film or coating on the substrate.
- Desorption and Removal: Byproducts of the reaction are desorbed and removed from the chamber.
-
Types of CVD Processes:
- Thermal CVD: Uses heat to decompose precursor gases.
- Plasma-Enhanced CVD (PECVD): Employs plasma to lower the reaction temperature, enabling deposition on heat-sensitive substrates.
- Atomic Layer Deposition (ALD): A variant of CVD that allows for atomic-level control of film thickness.
- Low-Pressure CVD (LPCVD): Operates under reduced pressure to improve film uniformity.
-
Advantages of CVD:
- High-Quality Films: Produces films with excellent purity, density, and uniformity.
- Versatility: Can deposit a wide range of materials, including metals, ceramics, and polymers.
- Low-Temperature Processing: Certain CVD techniques, like PECVD, enable deposition at lower temperatures, reducing thermal stress on substrates.
-
Applications of CVD:
- Semiconductors: Used to deposit thin films for integrated circuits and microelectronics.
- Optics: Produces anti-reflective coatings and optical filters.
- Coatings: Creates wear-resistant and corrosion-resistant coatings for industrial components.
- Energy: Enables the fabrication of solar cells and battery materials.
-
Recent Technological Advancements:
- Precursor Innovation: Development of new precursor gases to enable the deposition of complex materials.
- Energy Efficiency: Optimization of reaction conditions to reduce energy consumption.
- Scalability: Advances in reactor design to enable large-scale production.
- Nanotechnology: Use of CVD to fabricate nanomaterials with unique properties.
-
Challenges and Future Directions:
- Cost: High equipment and precursor costs can limit accessibility.
- Complexity: Requires precise control of process parameters.
- Environmental Impact: Development of eco-friendly precursors and processes is a focus area.
For more detailed information on chemical vapor deposition, refer to the linked topic.
Summary Table:
Aspect | Details |
---|---|
Fundamental Steps | Gas transport, adsorption, surface reactions, film growth, desorption. |
Types of CVD | Thermal CVD, Plasma-Enhanced CVD (PECVD), Atomic Layer Deposition (ALD). |
Advantages | High-quality films, versatility, low-temperature processing. |
Applications | Semiconductors, optics, coatings, energy. |
Recent Advancements | Precursor innovation, energy efficiency, scalability, nanotechnology. |
Challenges | High cost, process complexity, environmental impact. |
Ready to explore how CVD technology can transform your industry? Contact our experts today for tailored solutions!