Chemical vapor deposition (CVD) is a sophisticated process used to deposit thin films of materials onto a substrate through chemical reactions in the vapor phase. This method involves the use of volatile precursors that are vaporized and then decomposed or reacted on a heated substrate surface to form a solid film. The process is widely used in industries such as semiconductors, optics, and coatings due to its ability to produce high-purity, high-performance materials. The steps typically include the transport of gaseous reactants to the substrate, adsorption, surface reactions, nucleation, and film growth, followed by the removal of by-products. CVD is versatile, allowing for the deposition of a wide range of materials, including metals, ceramics, and polymers, with precise control over film properties.
Key Points Explained:
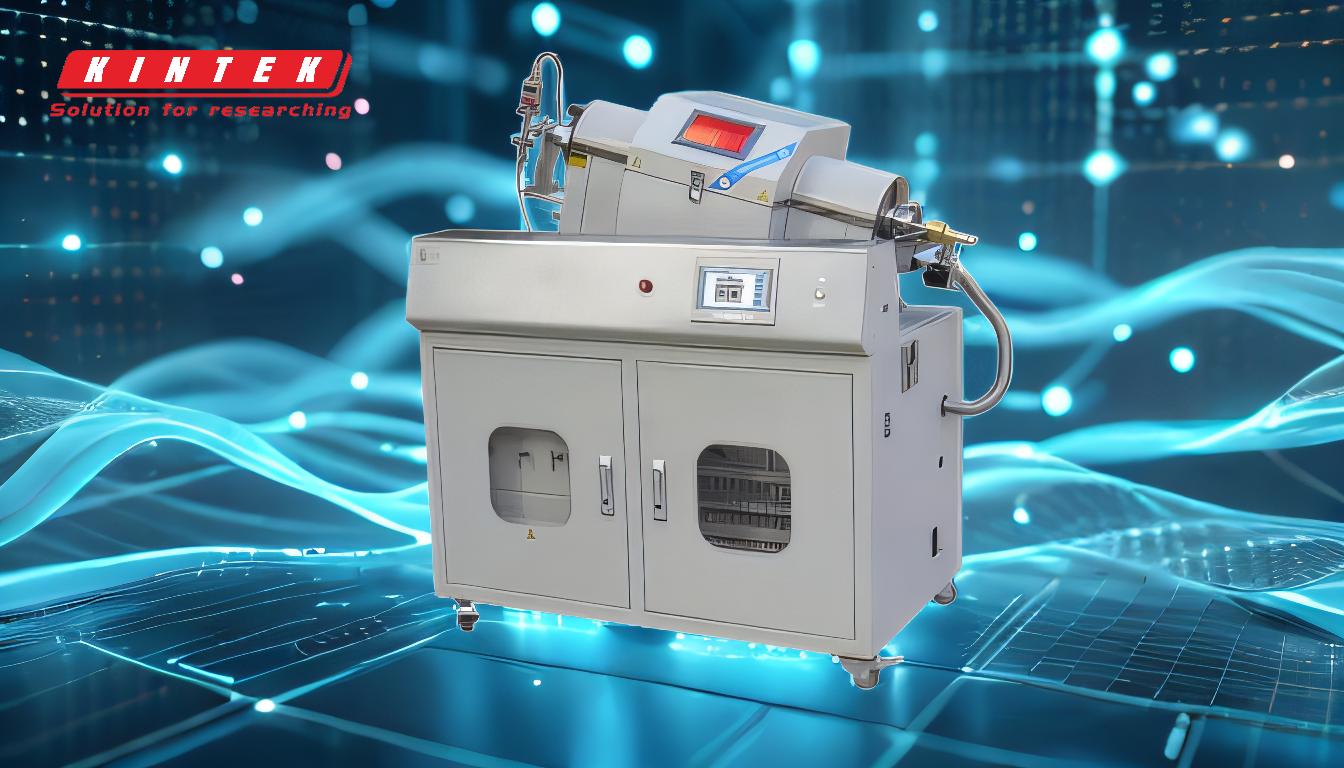
-
Definition and Purpose of CVD:
- Chemical vapor deposition (CVD) is a process used to deposit thin films of materials onto a substrate. It is widely utilized in industries such as semiconductors, optics, and coatings due to its ability to produce high-purity, high-performance materials.
-
Steps Involved in CVD:
- Transport of Gaseous Reactants: The volatile precursor compounds are transported to the substrate surface in a gaseous state.
- Adsorption: The gaseous species adsorb onto the substrate surface.
- Surface Reactions: The adsorbed species undergo chemical reactions on the substrate surface, often catalyzed by the surface itself.
- Nucleation and Film Growth: The reaction products form nuclei, which grow into a continuous film.
- Desorption and By-product Removal: Gaseous by-products desorb from the surface and are transported away from the reaction zone.
-
Types of Reactions in CVD:
- Thermal Decomposition: The precursor gas decomposes into its constituent atoms or molecules upon heating.
- Chemical Reaction: The precursor gas reacts with other gases, vapors, or liquids present in the chamber to form the desired film.
-
Role of Vacuum and Heat:
- Vacuum Environment: A vacuum is often used to reduce contamination and control the pressure, which influences the reaction kinetics and film quality.
- Heated Substrate: The substrate is heated to provide the necessary energy for the chemical reactions to occur.
-
Materials Deposited by CVD:
- CVD can deposit a wide range of materials, including metals (e.g., tungsten, titanium), ceramics (e.g., silicon carbide, aluminum oxide), and polymers (e.g., poly(paraxylene)).
-
Applications of CVD:
- Semiconductors: CVD is used to deposit thin films of silicon, silicon dioxide, and other materials in the fabrication of integrated circuits.
- Optics: CVD is used to create anti-reflective coatings, optical filters, and other optical components.
- Coatings: CVD is used to apply protective and functional coatings on tools, molds, and other components.
-
Advantages of CVD:
- High Purity: The process can produce films with very high purity levels.
- Uniformity: CVD can deposit films uniformly over complex shapes and large areas.
- Versatility: A wide range of materials can be deposited using CVD.
-
Challenges and Considerations:
- Precursor Selection: The choice of precursor is critical as it affects the reaction kinetics and film properties.
- Process Control: Precise control over temperature, pressure, and gas flow rates is necessary to achieve desired film characteristics.
- Safety: Handling of volatile and potentially hazardous precursor gases requires strict safety protocols.
By understanding these key points, one can appreciate the complexity and versatility of the chemical vapor deposition process, making it a valuable technique in modern material science and engineering.
Summary Table:
Aspect | Details |
---|---|
Definition | A process to deposit thin films on substrates via chemical reactions. |
Key Steps | Transport, adsorption, surface reactions, nucleation, film growth, by-product removal. |
Materials Deposited | Metals, ceramics, polymers (e.g., tungsten, silicon carbide, poly(paraxylene)). |
Applications | Semiconductors, optics, coatings. |
Advantages | High purity, uniformity, versatility. |
Challenges | Precursor selection, process control, safety protocols. |
Discover how chemical vapor deposition can enhance your projects—contact our experts today for more information!