Cold Isostatic Pressing (CIP) is a manufacturing process that involves applying uniform pressure from all directions to a material, typically a powdered substance, using a high-pressure fluid medium. This technique is highly effective for shaping and consolidating powdered materials, enabling the creation of intricate shapes and achieving high green density. CIP is performed at ambient temperatures and is widely used in industries such as ceramics, metallurgy, and food processing. The process can be categorized into two methods: wet bag and dry bag. CIP is particularly useful for materials that require uniform density and complex geometries, such as refractory materials, insulators, and tool steels.
Key Points Explained:
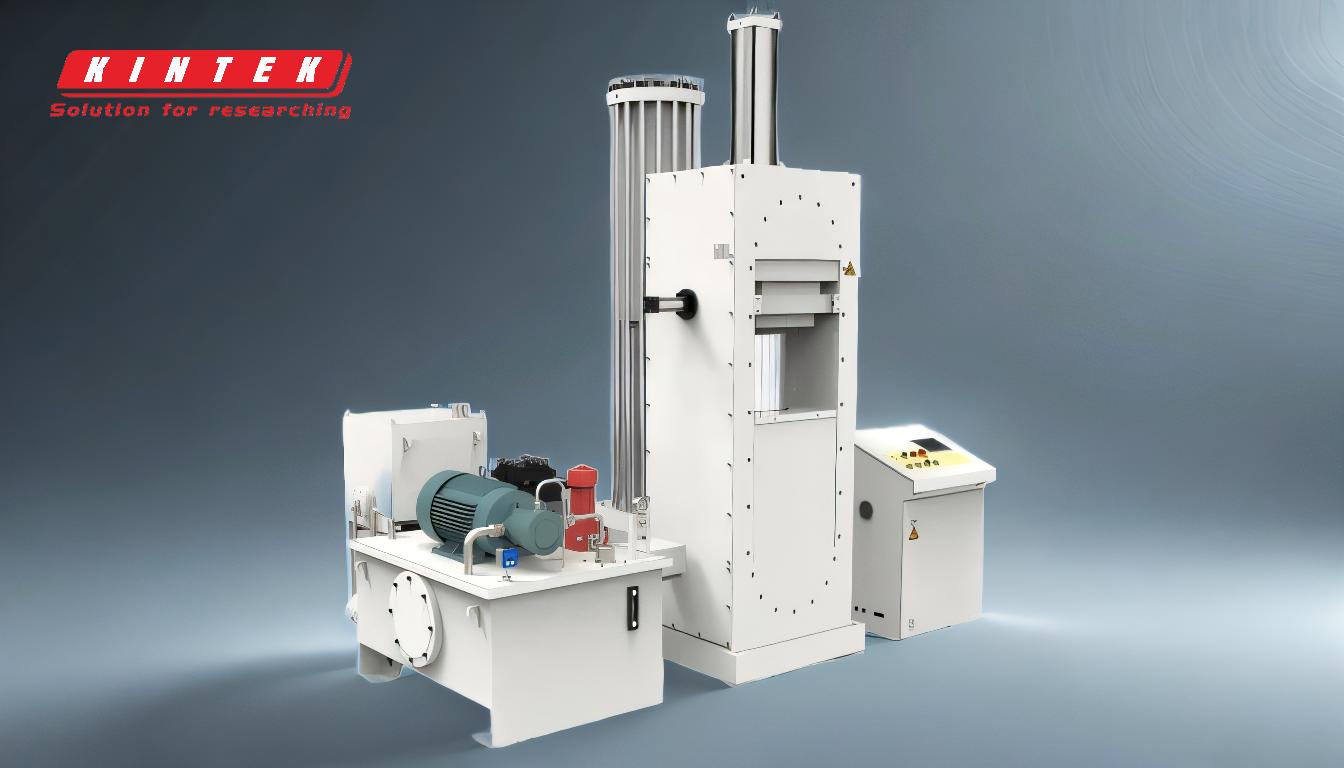
-
Definition and Process of Cold Isostatic Pressing (CIP):
- CIP involves immersing a material, usually in powdered form, in a high-pressure fluid medium (often an oil-water mixture) within a closed container.
- Hydraulic pressure is applied uniformly from all sides, ensuring equal pressure on every surface of the material.
- This uniform pressure increases the material's density, resulting in a compacted product with the desired shape.
-
Applications of CIP:
- CIP is used in the powder forming of a wide range of materials, including:
- Refractory materials
- Insulators
- Isotropic graphite
- High-melting-point metals
- Cemented carbides
- Tool steel
- Sintered filters
- Artificial bones
- Resin powder
- Food processing
- This versatility makes CIP a valuable process in industries requiring high precision and uniformity.
- CIP is used in the powder forming of a wide range of materials, including:
-
Wet Bag vs. Dry Bag Methods:
- Wet Bag Method: The material is placed in a flexible mold (bag) and submerged in the high-pressure fluid. After pressing, the mold is removed from the fluid for extraction of the compacted product.
- Dry Bag Method: The mold is fixed within the pressure vessel, and the fluid is pumped directly around it. This method is more suitable for mass production due to its efficiency.
-
Advantages of CIP:
- Uniform Density: The equal pressure from all sides ensures uniform density throughout the material, which is critical for high-performance applications.
- Complex Shapes: CIP can produce intricate shapes that are difficult to achieve with other pressing methods.
- High Green Density: The process results in high green density, which improves the material's mechanical properties after sintering.
-
Pressure Range in CIP:
- The pressure in a CIP chamber can reach up to 100,000 psi (pounds per square inch), making it capable of compacting even the most challenging materials.
-
Industries and Materials Benefiting from CIP:
- CIP is particularly beneficial for industries requiring materials with high strength, uniformity, and complex geometries. Examples include aerospace, medical devices, and advanced ceramics.
-
Environmental and Operational Considerations:
- CIP operates at ambient temperatures, reducing energy consumption compared to hot isostatic pressing (HIP).
- The use of a liquid medium (oil-water mixture) ensures efficient and consistent pressure application.
In summary, Cold Isostatic Pressing is a versatile and efficient process for compacting powdered materials into high-density, complex shapes. Its ability to apply uniform pressure makes it indispensable in industries requiring precision and uniformity in material properties.
Summary Table:
Aspect | Details |
---|---|
Process | Uniform pressure applied to powdered materials using a high-pressure fluid. |
Applications | Refractory materials, insulators, tool steels, food processing, and more. |
Methods | Wet bag (flexible mold) and dry bag (fixed mold). |
Advantages | Uniform density, complex shapes, high green density. |
Pressure Range | Up to 100,000 psi. |
Industries | Aerospace, medical devices, advanced ceramics. |
Environmental Impact | Operates at ambient temperatures, energy-efficient. |
Interested in how Cold Isostatic Pressing can benefit your industry? Contact our experts today to learn more!