Brazing is a versatile joining process that uses a filler metal to bond two or more materials together. It is commonly used in various industries due to its ability to create strong, leak-proof joints without melting the base materials. The process involves several key components and methods, including the selection of appropriate filler metals, heating techniques, and brazing pastes. Understanding these elements is crucial for achieving high-quality brazed joints.
Key Points Explained:
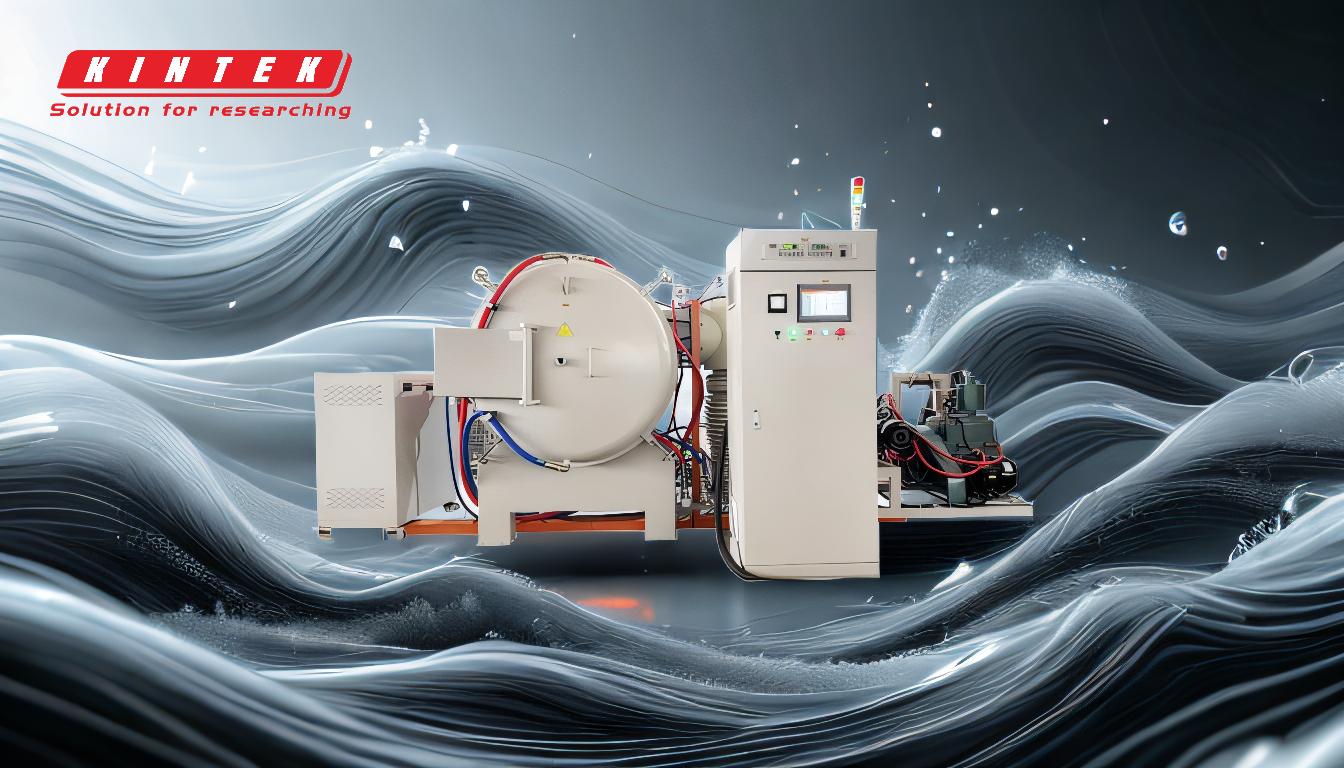
-
Common Filler Metals Used in Brazing:
- Aluminium-Silicon Alloys: These are widely used for brazing aluminium and its alloys due to their excellent corrosion resistance and compatibility with aluminium.
- Copper and Copper Alloys: Copper, copper-silver, copper-zinc (brass), and copper-tin (bronze) are commonly used for brazing copper and steel. They offer good thermal and electrical conductivity.
- Gold-Silver-Nickel Alloys: These are used in high-temperature applications and provide excellent strength and corrosion resistance.
- Silver-Based Filler Metals: Silver is a popular choice for brazing due to its good flow characteristics and ability to form strong joints with various base metals.
- Amorphous Brazing Foils: These foils, made from nickel, iron, copper, silicon, boron, and phosphorus, are used in specialized applications where precise control of the brazing process is required.
-
Common Heating Methods in Brazing:
- Torch Brazing: This method uses a gas flame to heat the filler metal and base materials. It is versatile and suitable for small-scale or repair work.
- Furnace Brazing: This involves heating the components in a furnace, often with controlled atmospheres like exothermic, hydrogen, argon, or vacuum to prevent oxidation.
- Induction Brazing: This method uses electromagnetic induction to heat the filler metal and base materials. It is fast and provides localized heating.
- Dip Brazing: The components are submerged in a molten salt or metal bath to achieve uniform heating.
- Resistance Brazing: This technique uses electrical resistance to generate heat at the joint interface, making it suitable for precise applications.
- Infrared Brazing: Infrared radiation is used to heat the materials, offering precise control over the heating process.
- Blanket Brazing: This method uses flexible heating blankets to apply heat uniformly over large or complex shapes.
- Electron Beam and Laser Brazing: These advanced techniques use focused energy beams for high-precision brazing, often used in aerospace and electronics industries.
- Braze Welding: This is a hybrid process that combines brazing and welding techniques, often used for repairing cast iron components.
-
Key Components of Brazing Paste:
- Brazing Alloy Powder: This makes up 80%-90% of the brazing paste and acts as the filler metal. It is crucial for forming the braze joint.
- Brazing Flux: The flux cleans oxides from the surfaces of the weldments and alloy powder, enhancing the wetting property and spread of the brazing alloy.
- Adhesive: The adhesive ensures proper mixing of the alloy powder and brazing flux, achieving the desired viscosity for easy dispensing and application.
By understanding these key elements, a purchaser can make informed decisions about the materials and methods best suited for their specific brazing applications. Whether selecting the appropriate filler metal, heating method, or brazing paste, each component plays a vital role in achieving a successful brazed joint.
Summary Table:
Category | Details |
---|---|
Common Filler Metals | Aluminium-Silicon, Copper Alloys, Gold-Silver-Nickel, Silver, Amorphous Foils |
Heating Methods | Torch, Furnace, Induction, Dip, Resistance, Infrared, Blanket, Electron Beam, Laser, Braze Welding |
Brazing Paste | Alloy Powder (80%-90%), Flux, Adhesive |
Need help choosing the right brazing materials or methods? Contact our experts today for personalized advice!