To prevent oxides from forming during brazing, a combination of chemical and mechanical methods, as well as controlled atmospheric conditions, are commonly employed. Chemical methods include the use of corrosive fluxes, base or acid attacks, or magnesium to suppress oxide layers in-situ. Mechanical methods such as sanding can also be used for preliminary external preparation. Additionally, inert atmospheres like hydrogen and dissociated ammonia are widely used to reduce or eliminate oxidation during brazing. Controlled atmosphere brazing (CAB) specifically removes oxygen from the brazing environment and replaces it with a hydrogen-nitrogen mixture to prevent oxidation. These techniques ensure oxide-free surfaces, which are critical for the proper bonding and flow of brazing filler metals, ultimately leading to high-quality joints.
Key Points Explained:
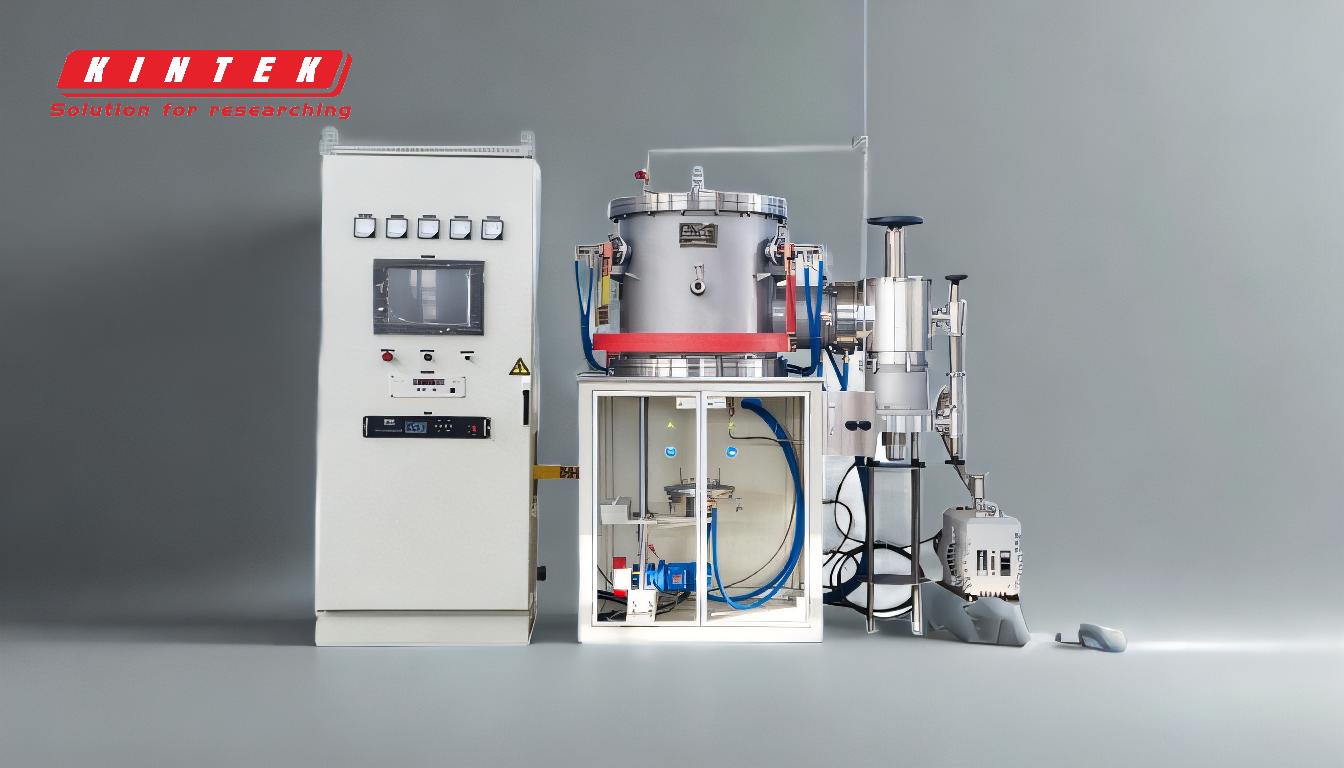
-
Chemical Methods to Suppress Oxide Formation:
- Corrosive Flux: Fluxes are chemical agents that remove oxides and prevent their formation during brazing. They are particularly effective for materials like aluminum, which naturally forms a stubborn oxide layer.
- Base or Acid Attack: Chemical treatments using bases or acids can dissolve or weaken the oxide layer, making it easier to remove before brazing.
- Magnesium: Magnesium can be used as a reducing agent to suppress oxide formation, especially in aluminum brazing, by reacting with the oxide layer and reducing it.
-
Mechanical Methods for Oxide Removal:
- Sanding or Abrasion: Mechanical methods like sanding or grinding can physically remove the oxide layer from the surface of the material before brazing. This is particularly useful for preliminary preparation, ensuring a clean surface for the brazing process.
-
Inert Atmospheres for Oxidation Prevention:
- Hydrogen and Dissociated Ammonia: These gases are commonly used in brazing furnaces to create an oxygen-free environment. By replacing oxygen with inert gases, oxidation is minimized, resulting in a clean and bright finished product.
- Reduction of Oxidation, Scaling, and Soot: Inert atmospheres not only prevent oxidation but also reduce issues like scaling (surface degradation) and carbon buildup (soot), which can negatively impact the brazing process.
-
Controlled Atmosphere Brazing (CAB):
- Oxygen Removal: CAB involves removing oxygen from the brazing oven and replacing it with a mixture of hydrogen and nitrogen. This ensures that no oxygen molecules are present to react with the metal surfaces.
- Prevention of Electron Transfer: Oxidation occurs when electrons move from metal atoms to oxygen atoms. By eliminating oxygen, this electron transfer is prevented, ensuring that the molten filler material can flow properly and form strong joints.
-
Importance of Oxide-Free Surfaces:
- Proper Bonding and Flow: Oxide layers can prevent brazing filler metals from bonding effectively or flowing properly across the surface. Oxide-free surfaces are essential for achieving strong, reliable joints.
- Furnace Type Influence: The choice of furnace type can significantly impact the ability to maintain oxide-free conditions. Furnaces designed for controlled atmospheres or inert gas environments are particularly effective for preventing oxidation.
By combining these methods, manufacturers can effectively prevent oxide formation during brazing, ensuring high-quality, durable joints in the final product.
Summary Table:
Method | Description |
---|---|
Chemical Methods | - Corrosive Flux: Removes oxides and prevents formation. |
- Base/Acid Attack: Dissolves or weakens oxide layers. | |
- Magnesium: Reduces oxide layers in-situ. | |
Mechanical Methods | - Sanding/Abrasion: Physically removes oxide layers for surface preparation. |
Inert Atmospheres | - Hydrogen/Dissociated Ammonia: Creates oxygen-free environments. |
Controlled Atmosphere | - Removes oxygen, replaces with hydrogen-nitrogen mix to prevent oxidation. |
Oxide-Free Surfaces | - Ensures proper bonding and flow of filler metals for strong, reliable joints. |
Achieve flawless brazing results with oxide-free surfaces—contact our experts today for tailored solutions!