A continuous furnace is an industrial heat treatment system designed for high-volume production, where workpieces are moved through the furnace on a conveyor or automated system. It ensures uniform heating, consistent material properties, and improved product quality. Continuous furnaces operate at a constant temperature, with items traveling at a constant speed, eliminating the need for racks or baskets and reducing energy consumption. These furnaces are ideal for medium to high-volume manufacturing, offering benefits such as high production rates, reduced labor requirements, and lower upfront investment. They are commonly used in industries requiring rapid thermal processing, such as drying, curing, and heat treatment of small to medium-sized products.
Key Points Explained:
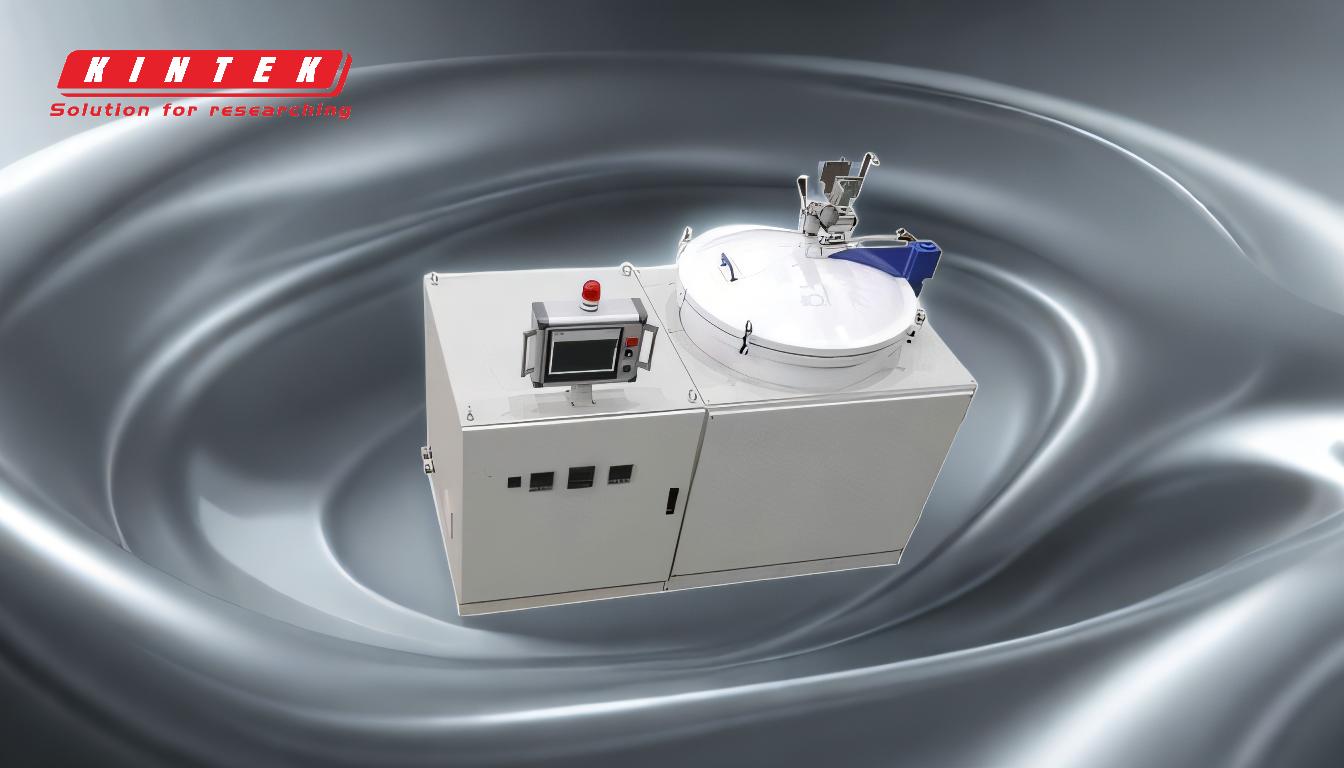
-
Definition and Purpose of Continuous Furnaces:
- A continuous furnace is an industrial furnace designed for high-volume production, where workpieces are moved through the furnace on a conveyor or automated system.
- It is used for rapid thermal processing, such as drying, curing, and heat treatment, ensuring uniform heating and consistent material properties.
-
Operation Mechanism:
- Continuous furnaces operate at a constant temperature, with items traveling through the furnace at a constant speed.
- The furnace uses conveyor belts, 'walking beams', rotary screws, or other automated systems to move parts through the heating chamber.
- The process time is usually measured in minutes, making it suitable for high production environments.
-
Key Features:
- Uniform Heating: Ensures consistent heat distribution, leading to uniform material properties and improved product quality.
- High Production Rates: Continuous processing allows for high throughput, making it ideal for medium and high-volume manufacturing.
- Energy Efficiency: Eliminates the need for racks or baskets, reducing overall energy consumption.
- Reduced Labor Requirements: Automation reduces the need for manual labor, lowering operational costs.
-
Advantages of Continuous Furnaces:
- Superior Temperature Uniformity: Ensures part-to-part temperature uniformity, leading to consistent product quality.
- Increased Throughput: High production rates due to continuous processing.
- Process Combination: Can include multiple heating zones and a cooling section, reducing cooling times and improving efficiency.
- Lower Upfront Investment: Compared to batch furnaces, continuous furnaces often require a lower initial investment.
- Reduced Changeover Times: Minimizes downtime between production runs, increasing overall efficiency.
- Part Loading Flexibility: Can handle a variety of part sizes and shapes, making it versatile for different manufacturing needs.
-
Applications:
- Continuous furnaces are suitable for industries requiring rapid thermal processing, such as automotive, aerospace, and electronics.
- They are ideal for manufacturing medium and high-volume products, where consistent quality and high production rates are critical.
-
Design Considerations:
- Conveyor System: The type of conveyor system depends on the production line, volume of production, and required temperature.
- Heating Zones: The furnace can include multiple heating zones and a cooling section to optimize the heat treatment process.
- Automation: High levels of automation are typical, with manual loading and unloading still possible but less common.
-
Comparison with Batch Furnaces:
- Continuous Processing: Unlike batch furnaces, continuous furnaces operate without interruption, leading to higher efficiency and throughput.
- Energy Consumption: Continuous furnaces generally consume less energy due to the elimination of racks or baskets and the constant temperature operation.
- Production Volume: Continuous furnaces are better suited for high-volume production, while batch furnaces are more flexible for low to medium volumes.
In summary, continuous furnaces are a critical component in modern industrial heat treatment, offering significant advantages in terms of efficiency, uniformity, and production rates. Their design and operation make them ideal for high-volume manufacturing environments, where consistent quality and rapid processing are essential.
Summary Table:
Key Feature | Description |
---|---|
Uniform Heating | Ensures consistent heat distribution for uniform material properties. |
High Production Rates | Ideal for medium to high-volume manufacturing with continuous processing. |
Energy Efficiency | Reduces energy consumption by eliminating racks or baskets. |
Reduced Labor Needs | Automation minimizes manual labor, lowering operational costs. |
Applications | Used in automotive, aerospace, and electronics for rapid thermal processing. |
Discover how a continuous furnace can optimize your production process—contact our experts today!