Controlled atmosphere heat treatment is a specialized process used to alter the physical and sometimes chemical properties of materials, typically metals, by heating them in a controlled environment. This environment is carefully regulated in terms of temperature, gas composition, and pressure to achieve specific outcomes such as hardening, annealing, or brazing. The process is crucial in industries where precision and consistency are paramount, such as aerospace, automotive, and electronics manufacturing. By maintaining a tightly sealed and controlled atmosphere, the process ensures that the material undergoes the desired transformation without contamination or oxidation, leading to high-quality, durable products.
Key Points Explained:
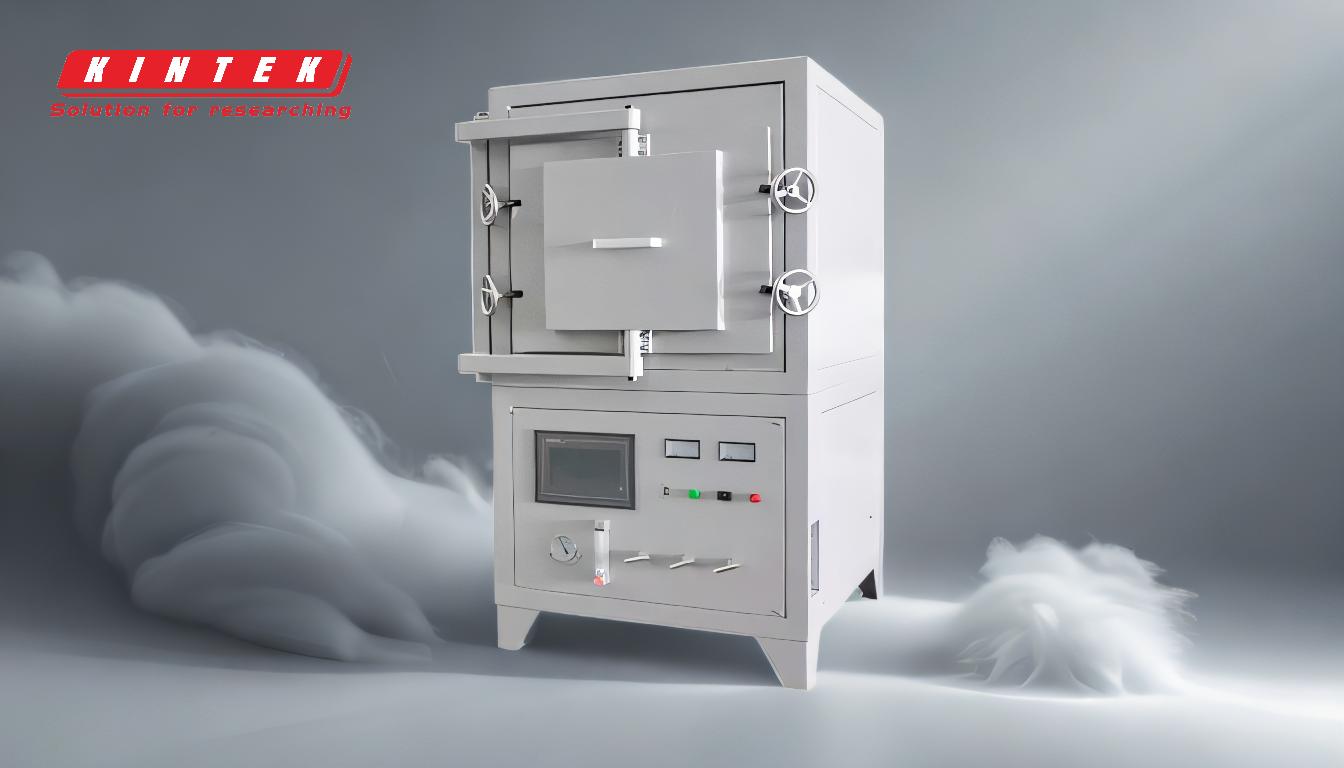
-
Definition and Purpose of Controlled Atmosphere Heat Treatment:
- Controlled atmosphere heat treatment involves heating materials in an environment where the atmosphere is precisely controlled. This is essential for processes like hardening, annealing, and brazing, where the material's properties need to be altered without exposure to external contaminants.
- The primary purpose is to achieve specific material characteristics, such as increased hardness, improved ductility, or enhanced corrosion resistance, by controlling the heating and cooling processes in a controlled environment.
-
Components of a Controlled Atmosphere Furnace:
- Temperature Control: The furnace maintains exact temperatures, which is crucial for processes that require precise thermal conditions.
- Atmosphere Regulation: The furnace controls the composition of gases within the chamber, ensuring that the material is not exposed to harmful elements like oxygen, which could cause oxidation.
- Sealed Environment: The furnace is tightly sealed to maintain the stability of the internal atmosphere, preventing any external air from entering and disrupting the process.
-
Advantages of Controlled Atmosphere Heat Treatment:
- Clean Appearance: Unlike traditional methods that may require post-process cleaning, controlled atmosphere heat treatment often results in a clean finish, especially in processes like controlled atmosphere brazing (CAB), where no flux is used.
- Consistency: The process is highly repeatable and consistent, as the controlled environment eliminates variables that could affect the outcome.
- Cost-Effectiveness: In processes like CAB, the use of conveyor belt-style ovens can reduce the cost per part, making it an economical choice for large-scale production.
-
Applications in Various Industries:
- Aerospace: Used for heat-treating critical components that require high strength and resistance to extreme conditions.
- Automotive: Essential for manufacturing parts like gears and engine components that need to withstand high stress and wear.
- Electronics: Used in the production of components that require precise thermal management and resistance to oxidation.
-
Comparison with Other Processes:
- Physical Vapor Deposition (PVD): Unlike PVD, which is a coating process that involves depositing thin layers of material onto a substrate, controlled atmosphere heat treatment focuses on altering the internal structure of the material itself.
- Traditional Heat Treatment: Compared to traditional methods, controlled atmosphere heat treatment offers superior control over the environment, leading to more consistent and higher-quality results.
-
Role of the Front Room in Controlled Atmosphere Furnaces:
- The front room in a controlled atmosphere furnace acts as a transitional area where workpieces are prepared before entering the main heating chamber. It prevents oxidation by maintaining a controlled environment and also serves as a slow-cooling area after the heat treatment process.
- This area is crucial for maintaining the integrity of the furnace's atmosphere, especially when the furnace door is opened, as it prevents external air from disrupting the controlled environment.
In summary, controlled atmosphere heat treatment is a highly specialized and precise process that offers numerous advantages in terms of quality, consistency, and cost-effectiveness. By maintaining a controlled environment, it ensures that materials undergo the desired transformations without contamination, making it indispensable in industries where precision and durability are critical.
Summary Table:
Aspect | Details |
---|---|
Purpose | Alters physical/chemical properties of materials in a controlled environment. |
Key Components | Temperature control, atmosphere regulation, sealed environment. |
Advantages | Clean finish, consistency, cost-effectiveness. |
Applications | Aerospace, automotive, electronics. |
Comparison | Superior to traditional heat treatment and PVD processes. |
Front Room Role | Prevents oxidation and maintains atmosphere integrity. |
Discover how controlled atmosphere heat treatment can elevate your material quality—contact our experts today!